Nella nuova rubrica “Tecnologie e attrezzature”, pubblicata mensilmente sulla rivista Plastix e in seguito anche su questo sito web, scopriremo insieme i principi di funzionamento di ciascuna tecnologia di lavorazione dei materiali polimerici. Esamineremo anche le attrezzature chiave utilizzate in ogni processo, dai componenti essenziali delle macchine ai sistemi ausiliari. Il settore delle materie plastiche è in continua evoluzione, con nuove tecnologie e dispositivi che emergono costantemente. L’obiettivo di questa rubrica è quindi quello di fornire informazioni aggiornate e approfondite, utili sia per i professionisti esperti sia per i neofiti del settore.
di Giovanni Lucchetta, Università di Padova
La vite di Archimede ha svolto un ruolo cruciale nel sollevamento di liquidi e materiali granulari per millenni. Questo dispositivo, costituito da una vite all’interno di un cilindro inclinato, sfrutta il principio della rotazione per trasportare acqua, sabbia o solidi particellari verso l’alto. Ad ogni rotazione della vite, il liquido o le particelle trasportate non aderiscono alla superficie della vite stessa, ma scivolano su di essa. Questo avviene perché la forza di gravità mantiene il materiale nello spazio ricavato tra il nocciolo della vite e la parte più bassa del cilindro. In altre parole, il materiale si trova confinato in un volume a forma di “C” che trasla verso l’uscita del cilindro (vedi figura d’apertura, ndr).
Non c’è da stupirsi se, con l’avvento dei primi termoplastici negli Anni Trenta del XX secolo, cilindri e viti furono adottati per spostare polveri e granuli.
Per fondere la plastica, invece, si utilizzavano cilindri vuoti riscaldati dall’esterno. Tuttavia, poiché la plastica ha una bassa conducibilità termica, la temperatura non era uniformemente distribuita (vedi figura 1), o la parte centrale della sezione era troppo fredda e non completamente fusa, o le regioni a contatto con il cilindro erano troppo calde e degradavano la plastica.
La soluzione a questo problema fu trovata nel 1939 dall’azienda Paul Troester Maschinenfabrick (PTM), che sviluppò un estrusore monovite elettricamente riscaldato e raffreddato ad aria, dotato di controllo automatico della temperatura e velocità variabile della vite. Questo rappresentò il precursore della moderna tecnologia di estrusione automatizzata per l’industria delle materie plastiche in rapida crescita.
L’estrusore monovite
Nelle prime macchine, la plastica riempiva completamente il cilindro, ma, come detto sopra, non era a temperatura uniforme. L’estrusore monovite ha superato questo problema in tre modi:
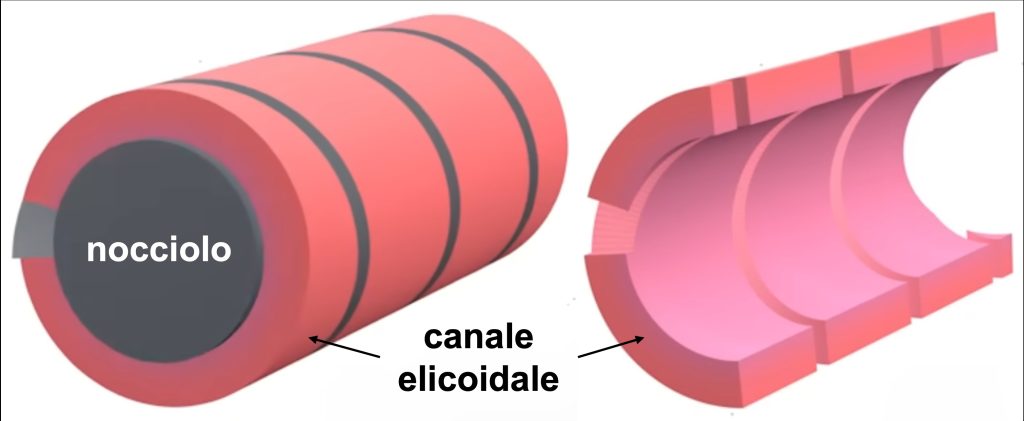
- Grazie alla presenza della vite, la plastica riempie solo il canale elicoidale avvolto attorno al nocciolo della vite (figura 2). Questo elimina la regione centrale più fredda, lasciando uno strato di plastica più sottile e riscaldato uniformemente.
- Mentre la vite ruota, il filetto trasporta la plastica in avanti sfruttando il maggior attrito che i granuli hanno a contatto con il cilindro (vedi sempre figura d’apertura, ndr). L’effetto della gravità è infatti trascurabile perché i granuli vengono compattati in un agglomerato che occupa tutto il canale elicoidale (figura 3). Per comprendere questo meccanismo e il ruolo fondamentale dell’attrito con il cilindro, provate a pensare all’azione che compiamo per togliere un tappo di sughero dal cavatappi dopo aver stappato una bottiglia di vino. La mano che tiene il tappo deve creare un forte attrito per causarne lo scivolamento lungo la vite del cavatappi e il conseguente avanzamento dovuto allo svitamento.
- L’azione della vite stessa riscalda la plastica in modo uniforme. Il diametro del nocciolo aumenta lungo la vite, in modo che la distanza tra la parete e il nocciolo diminuisca. Il filetto, quindi, sposta la plastica in avanti mentre espelle l’aria nella direzione opposta e sottopone i granuli a sforzi di compressione e taglio, premendoli contro la parete riscaldata del cilindro (figura 3). Questa azione crea attrito e quindi contribuisce a riscaldare ulteriormente la plastica in modo uniforme.
La figura 4 presenta una versione semplificata di una vite monoblocco a singola elica di un estrusore monovite convenzionale. Mostra tre distinte sezioni geometriche con un canale a profondità variabile e passo costante:
- La zona di alimentazione ha un canale profondo e ha la funzione di convogliare i granuli solidi lungo la vite.
- Nella zona di compressione il materiale viene compresso sotto l’effetto della riduzione della profondità del canale e passa dallo stato solido particellare allo stato fuso (fluido viscoso). Questa è la sezione più lunga ed è essenziale per il corretto funzionamento dell’estrusore, in quanto deve essere progettata in modo da fondere completamente i granuli polimerici. I polimeri semicristallini attraversano un punto di fusione netto, mentre i polimeri amorfi continuano a rammollirsi al di sopra della temperatura di transizione vetrosa, fino a quando la viscosità non è sufficientemente bassa per processare il polimero. Due sono le fonti di calore per la fusione o la plastificazione del polimero: la conduzione dal cilindro e soprattutto l’azione meccanica della vite.
- Nella zona di pompaggio (o dosaggio), la pressione del polimero fuso, che è aumentata progressivamente lungo la sezione di fusione, viene (solitamente) incrementata per vincere le perdite di carico che caratterizzano l’attraversamento della matrice.
Ma come avviene esattamente la fusione dei granuli? E perché avviene così velocemente?
Fusione del solido contiguo
I primi esperimenti sul meccanismo di fusione furono condotti da Bruce H. Maddock nel 1959. La procedura prevede che l’estrusore sia alimentato con una miscela composta da un polimero bianco e una piccola percentuale di masterbatch colorante: una resina con elevata concentrazione di pigmenti che, fondendo a temperature più basse, va a miscelarsi solo con il polimero fuso, provocandone il cambio di colore. In questo modo è possibile distinguere il polimero fuso (colorato) da quello ancora solido (bianco). Una volta portato l’estrusore a regime, la rotazione della vite viene interrotta e l’estrusore viene lasciato raffreddare fino alla completa solidificazione della plastica. Infine, la vite è estratta dal cilindro attraverso un’operazione che ricorda i carotaggi effettuati per l’analisi del suolo (figura 5).
L’estrazione permette di osservare lo stato del materiale lungo il canale elicoidale, come se avessimo fermato il tempo all’istante di spegnimento dell’estrusore. Esaminando le sezioni trasversali del polimero solidificato dopo averlo estratto dal canale della vite, si ottiene un’immagine chiara del comportamento del polimero durante la fusione, come mostrato nella figura 6. In questa foto, la regione essenzialmente bianca (colore base del polimero utilizzato) era solida appena prima dell’arresto della vite. Le regioni nella fotografia che sono per lo più rosa o rosa con striature bianche erano resina fusa appena prima dell’arresto della vite.
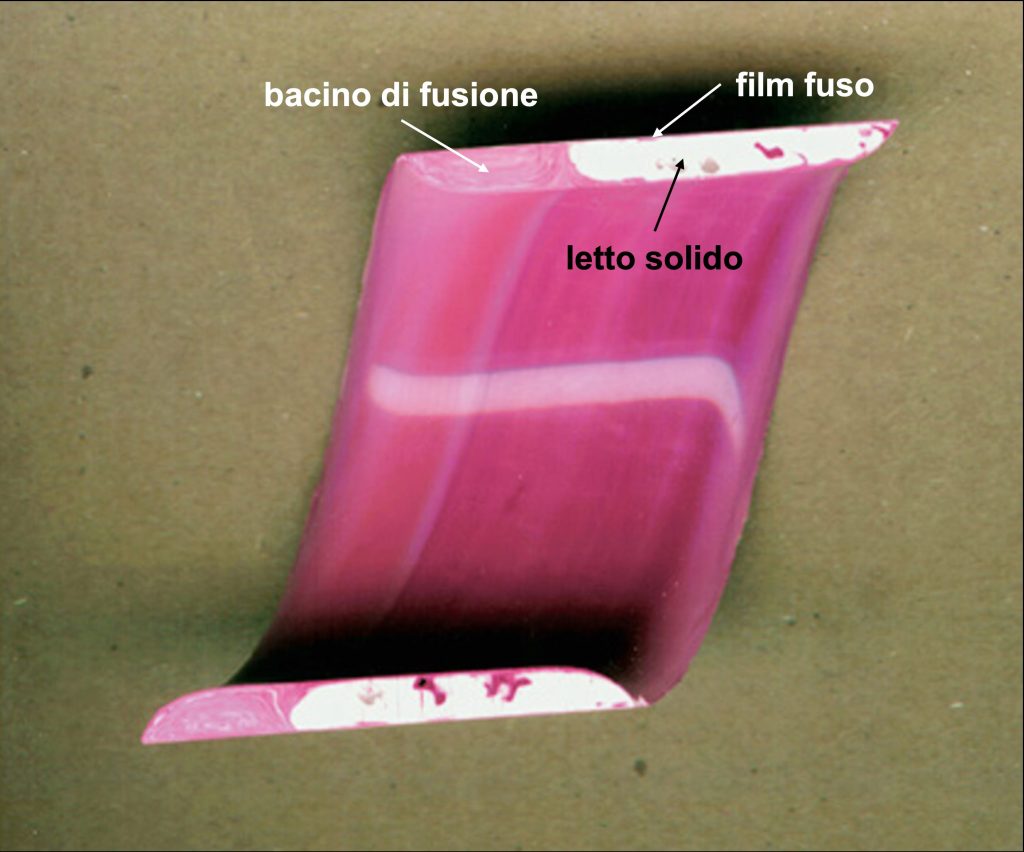
Gli studi sperimentali di Maddock ci permettono di illustrare il progresso della fusione negli estrusori monovite, dalla fine della zona di alimentazione (figura 7a) fino alla completa fusione dei granuli di polimero (figura 7d). Al contatto con la parete calda del cilindro, i granuli si fondono e formano un sottile film di polimero fuso tra il cilindro e il polimero solido (figura 7b). Il film fuso poi cresce e quando il suo spessore diventa maggiore del gioco del filetto, il fuso in eccesso scorre verso il fianco del filetto attivo, formando così un accumulo di fuso nella parte posteriore del canale (figura 7c).
Il gioco ridotto tra la cresta del filetto e il cilindro è cruciale per mantenere un’efficace barriera al flusso del materiale fuso. Si garantisce così che il film fuso si accumuli correttamente nel bacino di fusione, ottimizzando così il processo di fusione del materiale. Una vite usurata che presenti un gioco significativo permette al materiale fuso di rifluire più facilmente oltre la cresta del filetto, riducendo l’efficacia della fusione.
L’accumulo di fuso e la riduzione progressiva della profondità del canale esercitano un’alta pressione, che deforma e spinge il letto solido di granuli verso il cilindro e verso il fianco del filetto passivo; il letto solido di polimero è quindi continuamente riorganizzato e mantenuto a contatto con il film fuso. Man mano che la fusione procede, l’accumulo di fuso cresce gradualmente a spese del letto solido di polimero, fino a quando il materiale fuso riempie l’intera sezione trasversale del canale della vite. Questo meccanismo prende il nome di “fusione del solido contiguo” (Contiguous Solid Melting, o CSM) e caratterizza la quasi totalità degli estrusori che operano con la tramoggia piena (“a bocca piena”), ovvero con una portata che è limitata dalla capacità di fusione del sistema.
Energia di fusione
L’azione della vite consente di mantenere un film fuso sottile e di sottoporlo a elevati stress di taglio, provocandone il riscaldamento per attrito viscoso. In pratica, man mano che si fonde il letto solido a contatto con il film, il polimero è rimosso e accumulato nel bacino di fusione, offrendo così una nuova superficie solida da fondere. Per utilizzare un’analogia che può essere a tutti familiare, è come se volessimo sciogliere una noce di burro in una padella. In quel caso la fusione avviene più velocemente se trasciniamo la noce su porzioni di superficie non coperte dal burro fuso, che agirebbe da isolante. Ecco perché in un estrusore monovite la fusione dei granuli avviene così velocemente.
L’energia per la fusione del letto solido si sviluppa nel film fuso principalmente attraverso il riscaldamento per attrito viscoso. La maggior parte dei trasformatori comprende il concetto di calore trasferito dal cilindro riscaldato, ma la dissipazione viscosa, che fornisce l’80-90% dell’energia necessaria per la fusione del polimero, non è altrettanto facilmente compresa. Di conseguenza, si verifica spesso un’errata impostazione delle temperature del cilindro.
La dissipazione viscosa si verifica quando il film fuso aderisce al cilindro e al polimero sottostante. Mentre la vite ruota all’interno del cilindro, il polimero fuso che aderisce a entrambi si deforma a taglio a elevata velocità. Per visualizzare questa deformazione, pensate a un mazzo di carte in cui ciascuna carta (o lamina, nella terminologia fluidodinamica) scorre relativamente alle adiacenti. La velocità relativa tra le lamine provoca lo scorrimento delle catene polimeriche che si orientano e si disimpigliano opponendo un’elevata resistenza. La deformazione del fuso richiede, quindi, una coppia meccanica per far ruotare la vite. L’energia spesa per esercitare tale coppia è quindi dissipata per vincere “l’attrito” tra le catene polimeriche.
Durante l’estrusione, la deformazione continua introduce sempre più calore nel fuso. Ciò ne aumenta la temperatura, e la quantità di fuso cresce a seguito della conduzione di calore dal film al polimero solido. Si noti che questo non descrive l’intero meccanismo di fusione, poiché anche la compressione dei granuli e il loro attrito influenzano la velocità di fusione. Tuttavia, trascurare questi effetti in prima approssimazione aiuta a chiarire la dissipazione viscosa. Quest’ultima è la principale fonte di energia per la fusione e l’aumento di temperatura nel fuso dopo che la fusione è completata.
La velocità di fusione è fortemente proporzionale alla velocità di rotazione della vite. L’energia fornita al polimero attraverso l’azione della vite è uguale al prodotto della coppia per la velocità di rotazione per l’intervallo di tempo considerato. Questo spiega perché la temperatura del fuso aumenta sensibilmente con la velocità di rotazione della vite. Il riscaldamento del cilindro ha un effetto molto minore, tranne che negli estrusori molto piccoli.
Ma allora a cosa servono le resistenze installate sul cilindro?
Sono necessarie essenzialmente per due motivi:
- In fase di avviamento del processo, per fondere il polimero che si era solidificato nella zona di compressione e di pompaggio prima di mettere in rotazione la vite. Un avvio prematuro potrebbe infatti comportare la rottura della vite.
- Per rendere indipendente il controllo di temperatura da quello di portata. Se tutta l’energia venisse fornita dall’azione della vite, un aumento di portata comporterebbe necessariamente un aumento della temperatura del fuso. Sottodimensionando il contributo della vite è possibile utilizzare quello delle resistenze per un controllo fine della temperatura.