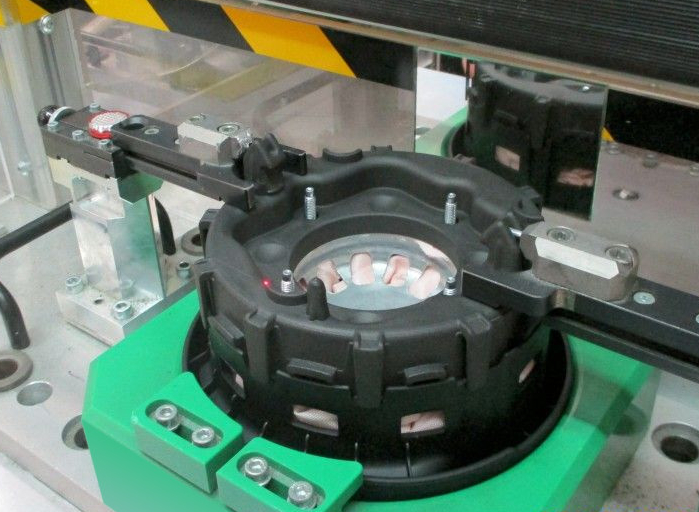
Il Centro Innovazioni della Joyson Safety Systems, fornitore statunitense di dispositivi di sicurezza attivi e passivi ai principali OEM dell’automotive, ha deciso di esplorare le potenzialità dell’additive manufacturing nella produzione di supporti per airbag (Airbag housing container) avviando un progetto dedicato all’airbag frontale del conducente (Driver Airbag o DAB). Il team di esperti ha così effettuato un’analisi di mercato al fine di individuare un materiale che corrispondesse alla poliammide rinforzata con fibra di vetro al 40% tradizionalmente utilizzata per lo stampaggio a iniezione dl pezzo.
Poliammide rinforzata con fibra di carbonio
In caso di urto, il cuscino dell’airbag si gonfia a una velocità di circa 30-50 millisecondi per evitare lesioni al conducente. Il supporto dell’airbag mantiene in posizione tutto il dispositivo di sicurezza passivo, quindi è un componente critico per l’intero sistema.
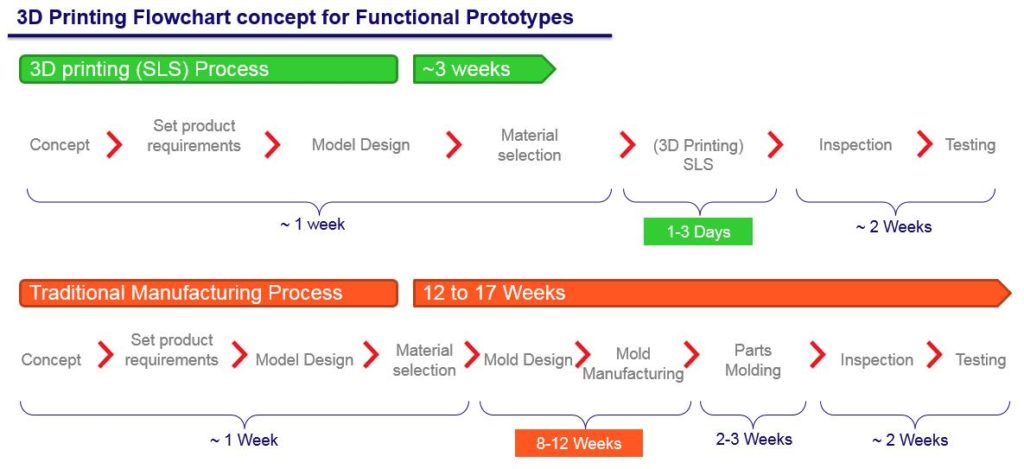
Per la messa a punto del pezzo stampato in 3D, il team Joyson Safety Systems ha fissato un programma molto rigoroso, che puntava allo sviluppo di un prototipo funzionale in pochi giorni anziché mesi e alla verifica delle prestazioni con sistemi di collaudo reali, sottoponendo il componente a sbalzi termici e a forti sollecitazioni meccaniche. Il pezzo è stato realizzato mediante Sinterizzazione Laser Selettiva (SLS) da CRP Technology utilizzando il Windform® SP, composito a base poliammidica rinforzato con fibra di carbonio proprietario dell’azienda modenese.
Il supporto è stato testato in un modulo airbag completo da Joyson Safety Systems. Le prove hanno evidenziato le ottime prestazioni meccaniche del materiale in termini di elevata robustezza e resistenza agli urti, nonché una buona stabilità termica, riscontrata in una gamma di temperature variabili (23 °C, -35 °C e 85 °C).