Nata grazie alla lungimiranza di tre laureati del MIT, oggi Formlabs è punto di riferimento globale nella fornitura di stampanti 3D professionali, stereolitografiche (SLA) e a sinterizzazione laser selettiva (SLS), oltre che di software e servizi
Fornitore di hardware, ma anche di software e servizi, e con un ampio ventaglio di materiali per la stampa 3D, Formlabs rende disponibili sistemi che sfruttano la tecnologia SLA, ovvero i modelli Form 3+ e Form 3L, a cui si aggiungono anche le versioni 3B+ e 3BL sviluppate appositamente per il settore sanitario, e sistemi a tecnologia di stampa a polvere, SLS, come la recente Fuse 1+ 30 W. Sia la stampante Form 3+ che la Form 3L (quest’ultima è la versione con un volume di stampa più ampio) offrono una tecnologia e un’assistenza di rilievo, per parti sempre di qualità grazie all’affidabilità e alla precisione di stampa, che permettono di avere ciò di cui si ha bisogno al primo tentativo.
Per questi sistemi, l’azienda rende disponibili più di 35 materiali convalidati pronti per l’uso. Ogni materiale è caratterizzato da impostazioni di stampa ottimizzate per ottenere risultati di livello ed elevata affidabilità, oltre a biocompatibilità e a proprietà meccaniche e termiche superiori.
«Offriamo materiali specializzati», sottolinea Luca Valentino Colmi, product engineer a supporto della rete vendite per Formlabs, «che assicurano stabilità ai raggi UV, resistenza al fuoco, protezione da scariche elettrostatiche, biocompatibilità, maggiore rigidità grazie al rinforzo in vetro e molto altro. Il punto laser da 85 micron garantisce una precisione dettagliata e finiture di alta qualità. Tra i tanti disponibili, per gli stampatori sono particolarmente raccomandate le resine Rigid 10K, High Temp e Grey Pro».
La citata Fuse 1+ 30 W è invece la più recente stampante SLS di Formlabs per la stampa 3D di parti ad alta precisione in sole 24 ore, grazie al potente laser da 30 W e al workflow semplificato. Il sistema è compatibile con la famiglia di polveri SLS dell’azienda, sviluppata appositamente per le stampanti della serie Fuse, che permette di stampare in 3D parti per utilizzo finale adatte alla produzione.
Nonostante la sempre maggiore diffusione, la stampa 3D si trova ancora ad affrontare alcune sfide per diventare una metodologia operativa largamente adottata anche tra gli stampatori. Quali ostacoli devono ancora essere superati e, soprattutto, come state lavorando per superarli?
«I limiti», osserva Colmi, «sono relativi allo stress meccanico subito dai pezzi prodotti in additive. I cicli ripetuti di pressione e temperatura a cui le forme “vecchia scuola” in metallo sono sottoposte sono enormi. Anche se le resine sono performanti, essendo a base polimerica, hanno un limite. Per superare queste restrizioni, lavoriamo costantemente all’elaborazione di nuove formule o materiali completamente innovativi. La stampa 3D, tuttavia, non deve essere considerata sostitutiva del metallo, ma piuttosto un mezzo per convalidare i design in fase pre-produzione».
Con riferimento alle vostre tecnologie di stampa 3D, quali sono i vantaggi e i benefici ottenibili dall’utilizzatore?
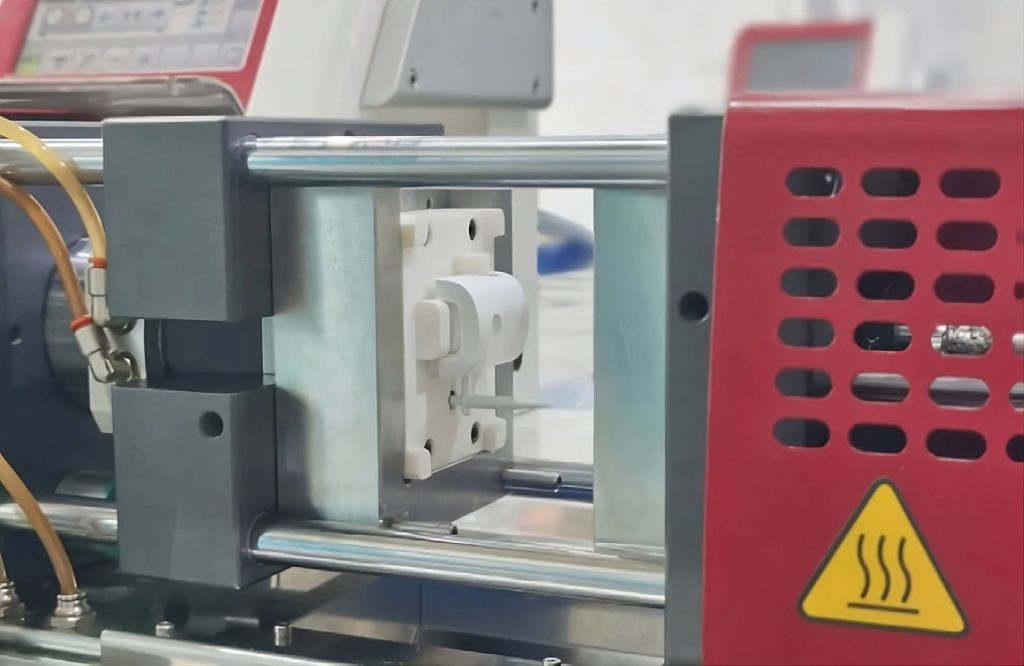
«I vantaggi principali», rileva e conclude Colmi, «si concentrano sulla flessibilità, la riduzione dei costi e del time-to-market.
In termini di flessibilità, la stampa 3D trasforma il concetto nella produzione favorendo la libertà di iterazione ed eleva le opportunità di personalizzazione di quanto si deve realizzare. Nel caso di uno stampo, è possibile crearlo, modificarlo aggiornando il disegno 3D e ristamparlo a costi contenuti: un cambiamento fondamentale. Questo metodo permette di produrre diversi inserti mantenendo la stessa base dello stampo, incrementando l’adattabilità. Economicamente, gli stampi per iniezione creati con la stampa 3D costano tra 25 e 200 euro, a seconda delle dimensioni, cioè molto meno degli stampi metallici tradizionali, che possono superare i 10 mila euro, variando per dimensioni, complessità e uso di macchinari CNC.
La stampa 3D riduce anche il time-to-market, con un investimento iniziale molto minore rispetto agli stampi in acciaio. Sebbene questi siano più duraturi e ammortizzino nel tempo il costo, richiedono un investimento iniziale maggiore. Gli stampi in 3D, con una durata minore, comportano un investimento iniziale ridotto, favorendo innovazione e velocità di produzione.
La produzione interna degli stampi abbrevia i tempi di attesa, un beneficio rilevante in contesti di incertezza e ritardi nella catena di fornitura, consentendo di ottenere uno stampo in poche ore. Inoltre, può avvenire a volte che le tirature richieste siano basse al punto tale da non giustificare l’investimento in stampo e attrezzature, quindi vi si rinuncia. Avere un sistema SLS in casa in grado di sintetizzare pezzi in poliammide (Nylon), come la nostra stampante Fuse 1+, permette di catturare queste fette di mercato altrimenti perse, aggiungendo mercato al business».
Pulizia e lucidatura completamente automatizzata per la stampa 3D SLS
La Fuse Blast (nella foto d’apertura, ndr) è una soluzione di pulizia e lucidatura completamente automatizzata, che si propone di rivoluzionare la post-elaborazione delle parti realizzate con la stampa 3D SLS. New entry dell’ecosistema SLS di Formlabs, riduce la manodopera e i costi fissi, accorcia il tempo di post-elaborazione dell’80% e consente di ottenere parti per utilizzo finale uniformi in soli 15 minuti. La Fuse Blast è dotata di un sistema di burattatura automatico per una pulizia automatizzata, che rimuove rapidamente la polvere semi-sinterizzata e residua, nonché di uno ionizzatore in linea che impedisce alla polvere di depositarsi nuovamente sulle parti, per garantire che queste risultino sempre pulite al tatto.
Riducendo i costi fissi e accelerando la produzione il sistema si propone di semplificare, migliorare e ottimizzare la post-elaborazione mediante la disponibilità di programmi definiti e anche di una modalità di pulizia assistita, o completamente manuale.
Rispetto ai programmi, le impostazioni predefinite, compatibili con i cicli multimateriale, eliminano le incertezze e consentono di ottenere risultati uniformi. Sebbene quasi tutte le parti possano essere pulite con l’impostazione Standard, è possibile utilizzare anche l’impostazione Nylon 12 GF Powder per eliminare l’armatura superficiale, e quella Delicate per un ciclo di burattatura più delicato.
Grazie al sistema di lucidatura Fuse Blast, il processo va oltre la pulizia e la finitura superficiale e consente di ottenere parti non solo pulite, ma anche lisce, resistenti ai graffi, pronte per la tintura e con un aspetto semilucido professionale.
Gianandrea Mazzola