Azienda a conduzione familiare, guidata oggi dalla quarta generazione di proprietari, Dolder Massara è un distributore internazionale di un’ampia gamma di compound polimerici e materie prime, quali: plastiche sostenibili, polimeri ad alte prestazioni, tecnopolimeri, elastomeri, masterbatch e specialità. In collaborazione con i propri clienti e fornitori, crea valore duraturo per tutti gli stakeholder attraverso l’impegno personale dei suoi dipendenti, la conoscenza specializzata e una grande trasparenza.
Il gruppo Dolder è responsabile dell’impatto sociale e ambientale generato dalle proprie attività. Promuove la sostenibilità e contribuisce attivamente al benessere della comunità in cui opera e alla protezione dell’ambiente.
Proprio nell’ambito della sostenibilità ambientale, lo scorso 21 novembre, in occasione del XXIX Congresso nazionale delle materie plastiche organizzato a Milanofiori dall’Associazione italiana dei Tecnici delle Materie Plastiche (TMP) e dalla rivista Plastix, Dolder ha voluto presentare la propria partnership con l’azienda svedese Polykemi, grazie ai relatori Henrik Palokangas, Global Sustainability Specialist di Polykemi, e Sara Bianchi, Sector Manager Plastics di Dolder Massara.
Polykemi e il metodo Materialsmart®
Fondato nel 1968 da Hugo Jönsson, con quartier generale a Ystad (Svezia), due stabilimenti in Cina e uno negli Stati Uniti, Polykemi è un compoundatore a conduzione familiare che produce principalmente resine termoplastiche su misura per il cliente e ottimizzate in modo da ridurne l’impatto ambientale.
La scelta delle materie prime può infatti avere un effetto importante sull’impatto ambientale di un prodotto. Polykemi ha quindi introdotto il metodo Materialsmart® per semplificare la scelta dei materiali plastici per una progettazione sostenibile.
Questo strumento si basa sull’analisi del ciclo di vita (LCA) di un prodotto ed è efficace per confrontare diversi materiali durante le scelte di progettazione. Fornisce dati precisi sull’impatto ambientale dei prodotti Polykemi “from cradle to gate”, cioè dalla produzione delle materie prime fino al momento in cui il prodotto finito esce dal cancello della fabbrica (gate). Materialsmart® consente quindi la quantificazione delle diverse composizioni, dell’impatto climatico (anche in base alla fonte energetica utilizzata per la produzione) e dell’impatto ambientale nell’ambito prescelto. Può essere utilizzato per calcolare e confrontare un’ampia gamma di articoli, prodotti a partire da vari polimeri sia vergini che riciclati, o con l’aggiunta di rinforzi, additivi e pigmenti.
Come metodo LCA, Polykemi ha scelto Environmental Footprint 3.1. Tutti i risultati, le conclusioni e i dati sono stati ottenuti da un esperto esterno (Report n. 778 & 944 Miljögiraff AB, Annie Johansson, in accordo con la norma ISO 14044:2006). Il rapporto è stato esaminato e verificato da una terza parte (Critical rewiev statement for 778 & 944 ESU Services, Niels Jungbluth) per garantire ulteriore correttezza e trasparenza. In base al volume utilizzato, Materialsmart® può coprire oltre il 98% di tutti i materiali utilizzati all’interno di Polykemi.
Materiale plastico vergine o riciclato
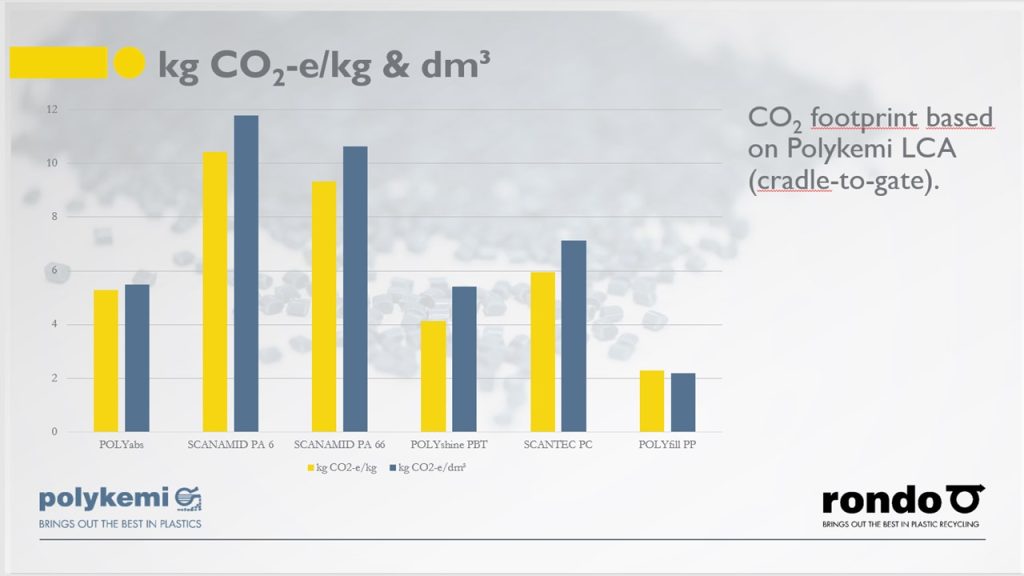
La scelta del materiale ha l’impatto più elevato sulla CO2-e/kg di un prodotto (se si escludono la fase di utilizzo e la fine del ciclo di vita): tra il 60 e l’80% dell’impronta di carbonio.
Il polipropilene non richiede molte fasi di conversione, producendo solitamente un valore inferiore a 2 kg CO2-e/kg. I polimeri con strutture chimiche più complesse, come la poliammide 6, richiedono più fasi di conversione e producono una CO2-e/kg più elevata, circa 10 kg CO2-e/kg (vedi figura 2).
I materiali provenienti da recupero e riciclo hanno anch’essi un impatto sul clima. Quando il materiale è classificato come scarto, l’impronta di carbonio è considerata prossima allo zero, ma tutti i processi e la logistica sono contabilizzati nel ciclo successivo.
Il fattore principale per valutare l’impronta di carbonio di un polimero riciclato è l’utilizzo d’energia dal momento della classificazione come rifiuto fino alla lavorazione di un nuovo materiale. Questo è il motivo di una differenza significativa in CO2-e/kg tra materiali post industriali (PIR) e post consumo (PCR), i quali richiedono il lavaggio: un processo altamente energivoro.
Conclusioni
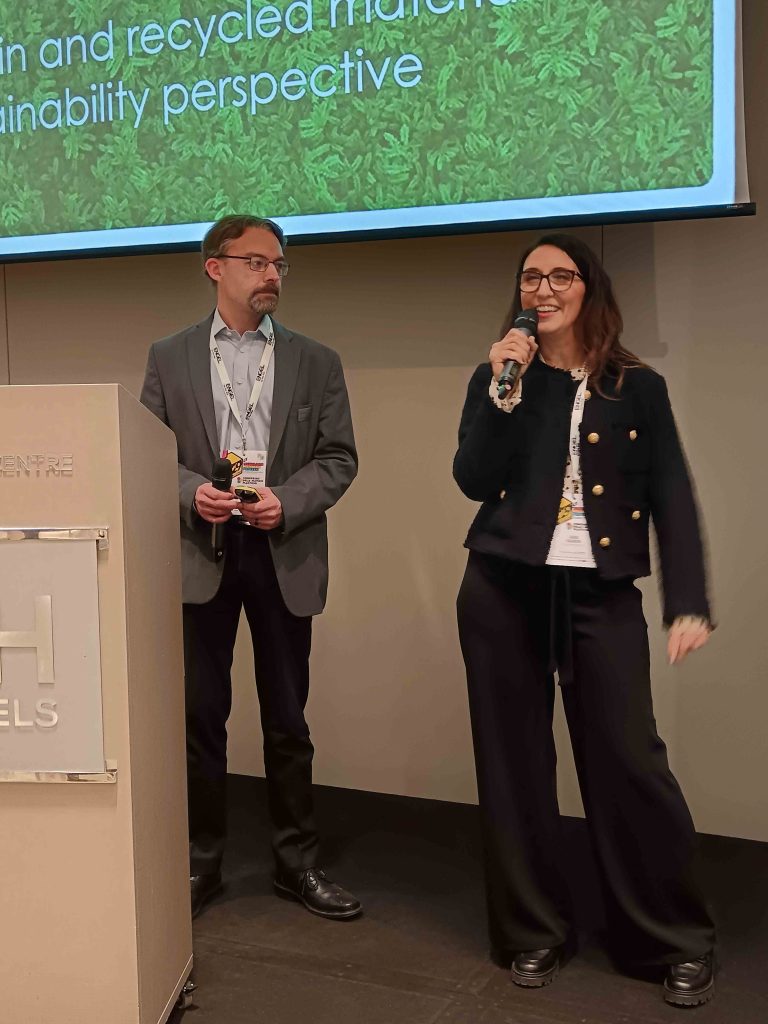
La selezione del materiale è sempre un compromesso di diverse proprietà. È difficile trovare un materiale che soddisfi subito tutte le richieste al livello desiderato. È quindi molto importante mettere in discussione la selezione il più rapidamente possibile durante la fase di sviluppo del prodotto, utilizzando la combinazione ottimale di proprietà, inclusa l’impronta di carbonio.
Con la possibilità di confrontare materiali diversi tramite lo strumento Materialsmart®, si apre l’opportunità di utilizzare l’impronta di carbonio come una proprietà tecnica. Trovare l’equilibrio per ogni singolo componente basato, non solo sugli aspetti ingegneristici, ma anche tenendo presente il riscaldamento globale, può consentire di “decarbonizzare” il proprio prodotto finale.
Secondo Polykemi, la chiave per “decarbonizzare” sta nell’identificare le reali esigenze di ogni singolo componente e scegliere il materiale per soddisfarle. È però necessario sfidare le vecchie convenzioni. La specifica originale non solo limita la capacità di ridurre l’impronta, ma aggiunge anche costi. Questo è il principio fondamentale su cui si basa Materialsmart®, che, quantificando il presente, consente anche di stabilire obiettivi e un modo più semplice di misurare i progressi, a livello di prodotto.
Un processo di sviluppo è solitamente di tipo iterativo, con piccoli cambiamenti costanti a un ritmo rapido. Essere in grado di simulare rapidamente l’impatto di cambiamenti grandi e piccoli al costo minimo sulla maggior parte delle emissioni di carbonio dei prodotti consente di considerare anche questo aspetto.