Agli inizi degli Anni Ottanta la situazione politica in Italia non è tra le più tranquille. Divampano gli scandali che coinvolgono personaggi dell’alta finanza, società assicurative, persino potenti prelati. Accanto agli scandali emerge la lotta tra istituzioni e criminalità organizzata in un’escalation che porterà all’assassinio del Generale Dalla Chiesa e, dieci anni dopo, alle stragi di Capaci e via D’Amelio.
In questo contesto destabilizzante, l’economia è in difficoltà, ma un evento porta a un nuovo inizio: nel settembre del 1980, con la celebre disputa Fiat, che si concluderà a favore dell’azienda automobilistica, si chiude un periodo di forte conflittualità tra lavoratori e imprese, una delle cause delle difficoltà economiche di quegli anni. Questo segna l’inizio di una nuova era nei rapporti sindacali, creando le condizioni per l’introduzione di nuovi sistemi produttivi.
In quegli anni, l’inflazione era molto elevata e l’industria, non potendo più fare affidamento sulla svalutazione competitiva della lira per stimolare le esportazioni, dovette investire in tecnologie innovative per ridurre i costi. Pur in mezzo a tanti eventi drammatici che hanno caratterizzato la nostra storia fin dalla fine della seconda guerra mondiale, l’Italia ha saputo conservare molte eccellenze in campo industriale e in quello delle maestranze. Con l’inizio di una nuova stagione di investimenti e di rinascita dell’economia, molti tecnici con grandi competenze hanno avuto il coraggio di lasciare le aziende per cui lavoravano per aprire delle loro attività. È così che nel nostro Paese sono proliferate le tante PMI che ancora oggi ne rappresentano l’ossatura economica.
Dalle parti di Campi Bisenzio…
Nel 1983, nel cuore della Toscana, a Campi Bisenzio (Firenze), tre soci dalla comprovata esperienza nel settore dell’estrusione-soffiaggio di materie plastiche decidono di fondare la società Meccanoplastica. È l’inizio di una grande storia di imprenditoria italiana, capace di conservare valori e passione nel proprio lavoro fino ai giorni nostri. A due anni dalla fondazione dell’azienda, vengono progettati e prodotti i primi impianti di estrusione-soffiaggio a funzionamento oleodinamico della serie MP, che andavano fino a una taglia di “corpi cavi” di 5 litri.
Dopo quindici anni dall’inizio di questa prima serie di macchine, verso la fine degli Anni Novanta, parte la produzione della serie HL, anch’essa a funzionamento oleodinamico ma con tonnellaggi maggiori, dedicata alla realizzazione di contenitori con volumi più ampi. Parallelamente al core business aziendale degli impianti di estrusione-soffiaggio, Meccanoplastica inizia a sviluppare il suo secondo filone tecnologico, quello dell’iniezione-soffiaggio, che rappresenta anche la svolta verso il funzionamento “full electric”.
“Con le macchine per iniezione-soffiaggio serie JET siamo diventati un punto di riferimento del settore sul mercato europeo”, dichiara Alberto Mencherini, figlio di uno dei tre storici fondatori dell’azienda, ora direttore vendite e marketing. “Nell’arco di vent’anni, dai primi modelli a oggi, la gamma è stata completata coprendo un range di forza di chiusura che va da 55 a 175 t”.
“Ciò che caratterizza la nostra azienda è l’attenzione per la qualità”, prosegue Mencherini. “Prima mio padre con i suoi soci e ora io, insieme al mio socio Rolando Fantini, abbiamo sempre puntato alla qualità e alla sostenibilità dei nostri prodotti. Già agli inizi degli Anni Duemila, siamo stati tra le prime aziende a ottenere la Certificazione ISO 9001 per la qualità di prodotto per le macchine a estrusione-soffiaggio, poi estesa anche alla tecnologia di iniezione-soffiaggio. La strada delle Certificazioni però non si arresta perché nel 2014 abbiamo ottenuto la Certificazione Ambientale ISO 9014”.
La tendenza a sviluppare macchine a funzionamento totalmente elettrico coinvolge anche le macchine di estrusione-soffiaggio (dallo sviluppo del progetto porta, nel 2010, al lancio della linea HE), per andare incontro alle esigenze del mercato.
“Non solo”, spiega Alberto Mencherini. “Le soluzioni full electric ci permettono di essere più attinenti ad alcune tipologie di applicazioni nei settori farmaceutico e alimentare, in cui, oltre al risparmio energetico, conta il fatto di dover installare un impianto che impatti il meno possibile sull’ambiente di produzione sotto l’aspetto degli agenti inquinanti. Con la soluzione full electric non solo si è eliminato il rischio di perdite d’olio, ma si è ridotta notevolmente la rumorosità dell’impianto in produzione, venendo a mancare la centralina oleodinamica. L’elettrificazione delle nostre macchine non è la sola tendenza che ci vede coinvolti. Il mercato chiede macchine di grandi dimensioni per inserire un numero maggiore di cavità-stampo e, di conseguenza, raggiungere una maggiore produttività. Anche noi, pertanto, ci stiamo orientando verso taglie di macchine sempre più potenti con corsa di traslazione adeguata ad alloggiare stampi sempre più grandi”.
La nascita di Meccanoplastica Iberica
Il percorso di crescita di Meccanoplastica è passato anche attraverso l’acquisizione di un piccolo concorrente locale nel 2011 e una partnership con un socio di Barcellona che ha dato vita a Meccanoplastica Iberica, con sede nella capitale catalana. Qui viene progettata e costruita la terza tipologia tecnologica dell’azienda: quella delle macchine bistadio completamente elettriche, per la produzione di contenitori in PET fino a un volume massimo di 25 l, partendo da una preforma esistente.
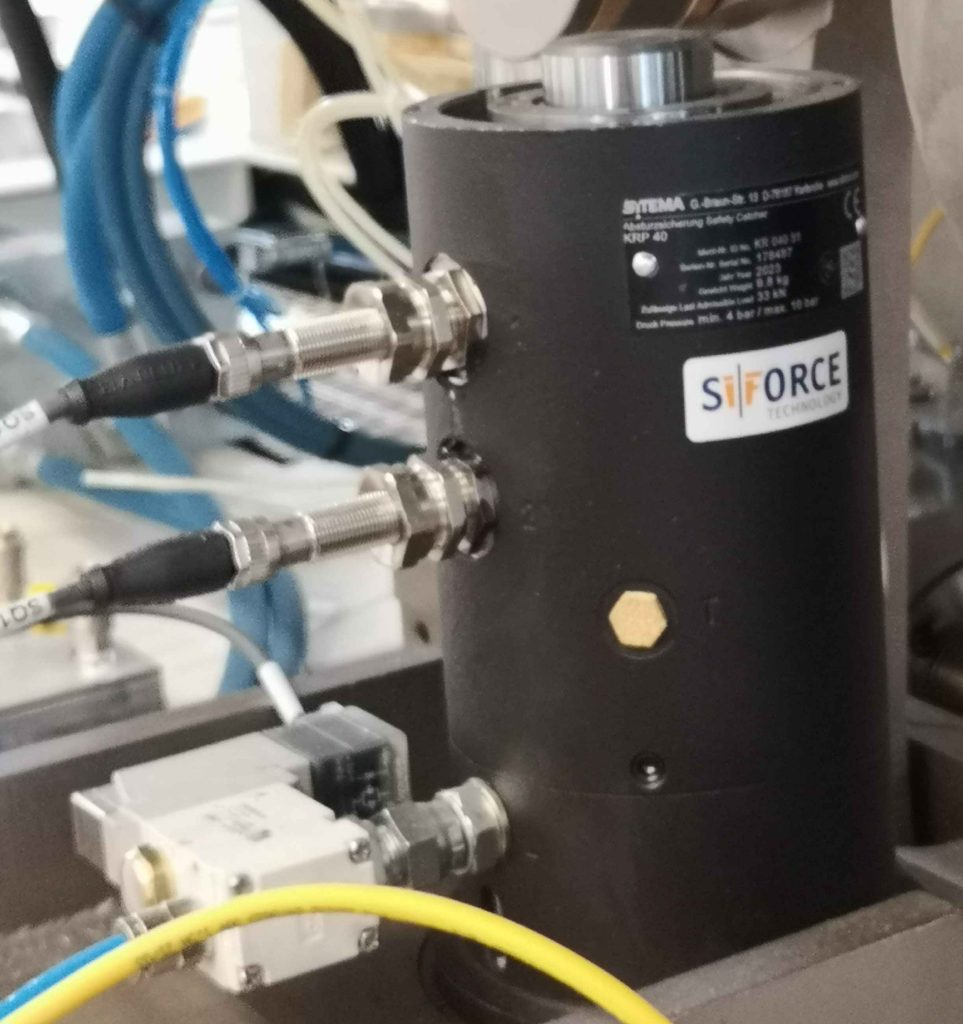
“Questa linea”, continua Mencherini, “ci ha consentito di chiudere il nostro cerchio tecnologico per presentarci ai clienti con un’offerta completa nel campo del packaging per la produzione di contenitori in plastica. Meccanoplastica è oggi full electric con classe di efficienza energetica 10 secondo la certificazione Euromap sia per l’estrusione-soffiaggio, che è il nostro business storico, sia per l’iniezione-soffiaggio, che è in forte espansione (dove sono applicati i prodotti di Sitema), sia per lo stiro-soffiaggio, che è la tecnologia che s’impiega per produrre le bottiglie d’acqua minerale. La differenza tra le nostre macchine per contenitori in PET e le altre presenti sul mercato è che i nostri impianti sono lineari, ovvero, gli stampi sono fermi in linea e sono le preforme a muoversi”.
Gli investimenti sopra citati, unitamente all’impennata della domanda durante il periodo Covid, ha fatto pressoché raddoppiare il numero di dipendenti presenti nella sede di Campi Bisenzio, a cui vanno aggiunti quelli della controllata di Barcellona. La crescita del fatturato è in buon parte dovuta all’espansione sui mercati esteri, dove il gruppo esporta ormai il 70% della propria produzione.
“Siamo nati e cresciuti grazie alla fiducia accordataci da aziende medio-piccole”, aggiunge Alberto Mencherini. “Con tali realtà l’ascolto del clientediventa fondamentale. Questo approccio, necessariamente molto tecnico, lo abbiamo poi sfruttato anche con aziende più grandi e strutturate. È evidente che studiare insieme ai clienti la soluzione migliore per le loro necessità è sempre estremamente importante. Tuttavia, anche per non stravolgere un flusso produttivo collaudato, cerchiamo di accontentare le richieste partendo come base da un impianto standard. Nello stabilimento toscano facciamo progettazione e assemblaggio, mentre ci rivolgiamo ad aziende esterne per la costruzione o per la fornitura della quasi totalità dei componenti delle macchine”.
La sicurezza sulle macchine a iniezione-soffiaggio
Il tema della sicurezza su macchine dove sono in gioco forze di chiusura che arrivano fino a 175 t, come per le presse a iniezione-soffiaggio di Meccanoplastica, è assolutamente centrale.
Dice Alberto Mencherini: “Il mercato che presidiamo oggi è composto essenzialmente da grandi aziende strutturate, spesso multinazionali, che sono particolarmente attente al rispetto di determinate procedure e capitolati sia in termini di qualità dei prodotti finali sia in termini di sicurezza. Innanzitutto, il nostro cliente tipo ha l’esigenza di mettere in sicurezza i propri operatori alle macchine, per cui le soluzioni che ci offre Sitema sono sinonimo di garanzia, poiché intervengono in modo puntuale e preciso in caso di guasto o manutenzione, affinché lo stampo non si muova mentre l’addetto sta operando nell’area di lavoro”.
“Sempre in tema di sicurezza, la nuova Direttiva Macchine, che entrerà in vigore nel 2027, sarà ancora più stringente, per cui ci siamo posti come obiettivo per il prossimo anno di valutare gli impianti in base a questa nuova normativa”, precisa Simone Nuti, responsabile R&D in Meccanoplastica.
“I prodotti Sitema sono certificati secondo le più rigide norme di sicurezza: CE, DGUV -ISO 16092-1 e ISO 16092-3, che rimpiazza la vecchia norma EN 693”, spiegano Giorgio Gamberale, responsabile commerciale per l’Italia e il Sud Europa di Sitema, e Nico Malorgio, nuovo ingegnere tecnico-commerciale di Sitema. “A totale garanzia per i nostri clienti, i dispositivi anticaduta e i sistemi di sicurezza Sitema vengono ricertificati ogni tre anni, testati e collaudati prima di essere immessi sul mercato. Inoltre, per dare al cliente ancora più tranquillità sui prodotti Sitema applicati, garantiamo una forza d’arresto minima pari a due volte il carico nominale, fino a un massimo di 3,5, consentendo un grande margine di sicurezza. Alla tecnologia brevettata Sitema abbiamo dato il nome di SiForce Technology (Self Intensifying Force), che identifica il principio del serraggio autostringente”.
Oggi, su tutti gli impianti per iniezione-soffiaggio JET vengono impiegati i dispositivi anticaduta KR per carichi da 10 kN fino a 1000 kN, a seconda del modello, e i freni di sicurezza KSP per carichi fino a 30 kN; questi ultimi come soluzioni accessorie richieste da alcuni clienti.
“Dal 5 al 7 marzo, alla fiera Mecspe 2025”, concludono Gamberale e Malorgio, “abbiamo presentato il nuovo KSE, sistema anticaduta elettromeccanico funzionante a 24 V, che ben si adatta a tutte le macchine completamente elettriche. Si tratta di un prodotto che è in linea con le attuali tendenze del mercato che cercano di limitare il più possibile l’impiego dell’oleodinamica”.