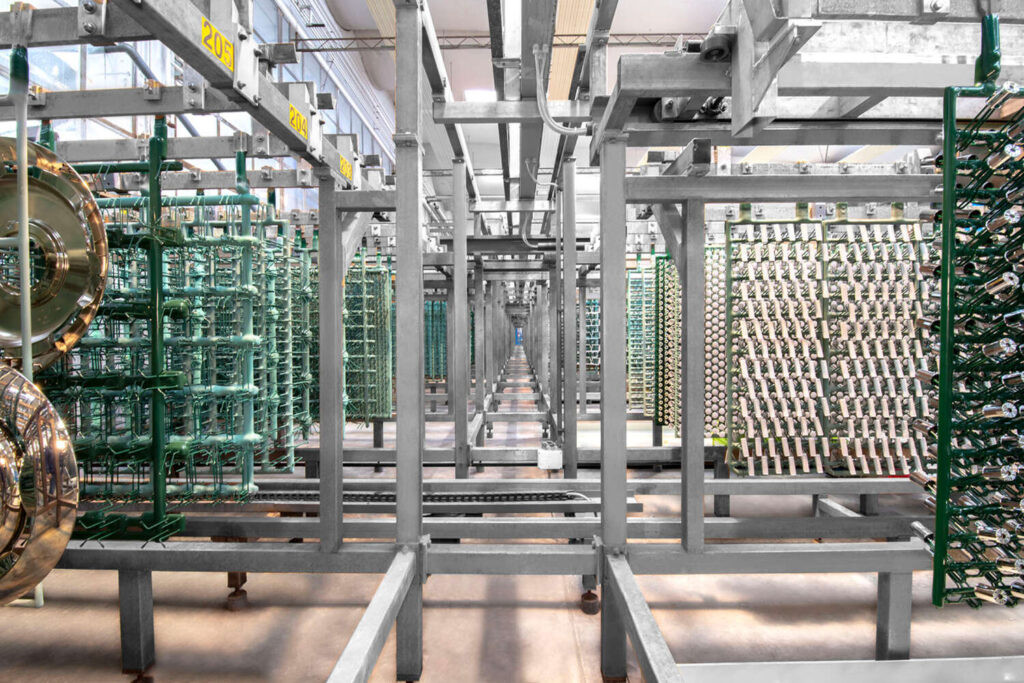
Fra i tanti distretti dislocati sul territorio nazionale quello della rubinetteria di Cusio-Valsesia riveste indubbiamente una particolare importanza, grazie alla sua capacità di creare reddito e occupazione: da solo, infatti, assicura la metà del fatturato dell’intero tessuto industriale piemontese. Tra i suoi punti di forza brillano una rete di piccole e medie imprese ricca e diversificata, caratterizzata da una forte dinamicità imprenditoriale e orientata ai mercati esteri, all’interno della quale si distinguono aziende innovative in settori ad alta tecnologia, che beneficiano dell’importante contributo del polo di ricerca di Novara, dotato di centri di eccellenza e di grande tradizione. Senza dimenticare l’efficiente sistema di riciclo degli scarti di lavorazione che permette alle realtà del distretto di operare seguendo i principi dell’economia circolare. Una di queste è Galvanoplast di Gravellona Toce (VB), nata dalla volontà dell’attuale amministratore unico, Mario Croda, e dei suoi tre soci. Lo abbiamo incontrato per conoscere meglio la tecnologia di cromatura delle materie plastiche.
Il mondo dei trattamenti galvanici
«Il nostro mercato prevalente è quello della rubinetteria, al quale oggi riserviamo il 70% delle nostre energie, mentre le restanti le dedichiamo per il 20% all’automotive e per il 10% ai settori della nautica e dei casalinghi». I pezzi trattati sono quasi tutti in ABS, articoli che, per quanto riguarda la rubinetteria, spaziano dalle maniglie per l’apertura e la chiusura dell’acqua ai soffioni e bracci per docce, dalle placche a muro ai pulsanti… Le principali richieste del settore automobilistico riguardano il trattamento di loghi ed emblemi, quelle del settore nautico il trattamento di scritte da applicare all’esterno di imbarcazioni di diverse dimensioni, mentre il comparto dei casalinghi si rivolge a noi prevalentemente per gli accessori delle macchine del caffè».
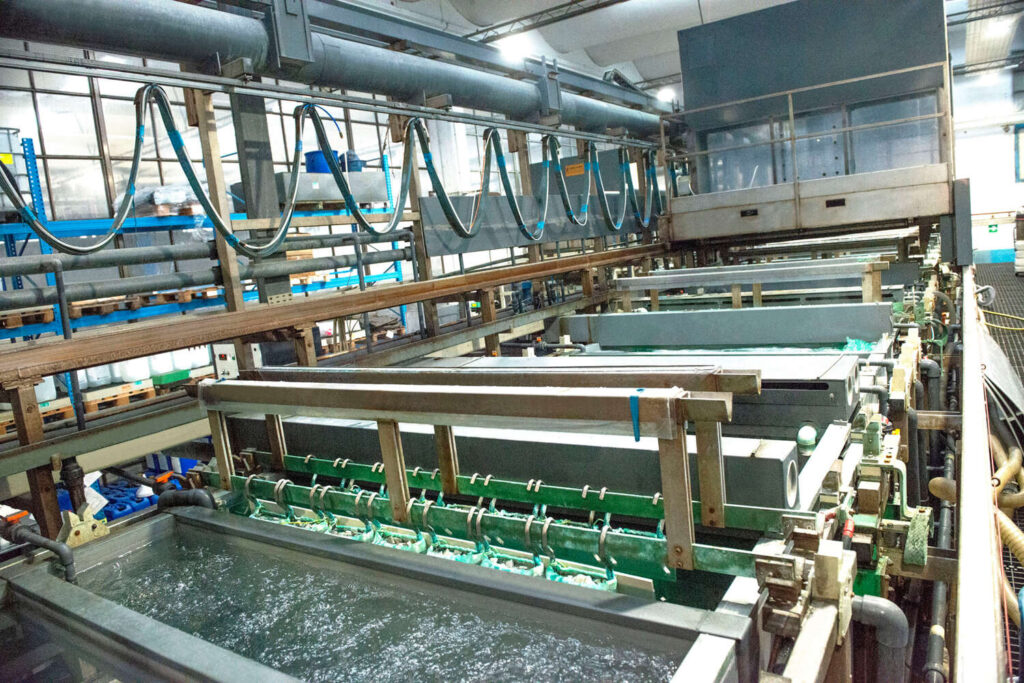
I clienti di Galvanoplastica sono soprattutto stampatori di materie plastiche che forniscono il prodotto finito a rubinetterie, case automobilistiche… e si rivolgono all’azienda piemontese per i trattamenti di cromatura (di diverse tipologie in base all’utilizzo dei particolari), nichelatura, satinatura e ramatura. «Nel 99,9% dei casi eseguiamo la cromatura e solo sporadicamente la nichelatura e la ramatura, ovviamente non prima di aver sottoposto al procedimento di metallizzazione chimica i pezzi in materiale plastico, al fine di renderli conduttivi e quindi idonei al processo elettrolitico» precisa Mario Croda. «Il processo prevede prima di tutto una fase di sgrassatura per eliminare eventuali impurità, alla quale segue la mordenzatura, che crea l’intacco superficiale della plastica affinché possano aderire i riporti successivi, prima di palladio e quindi di nichel chimico. A questo punto la superficie del pezzo diventa conduttiva ed è pronta per la fase elettrolitica di cromatura classica, nella quale al deposito iniziale di rame, con spessori da 8 a 80 micron, segue quello di nichel, con spessori fino da 4 a 40 micron e, infine, un flash di cromo, mai superiore a 1 micron, soglia oltre alla quale comincia a dare problemi».
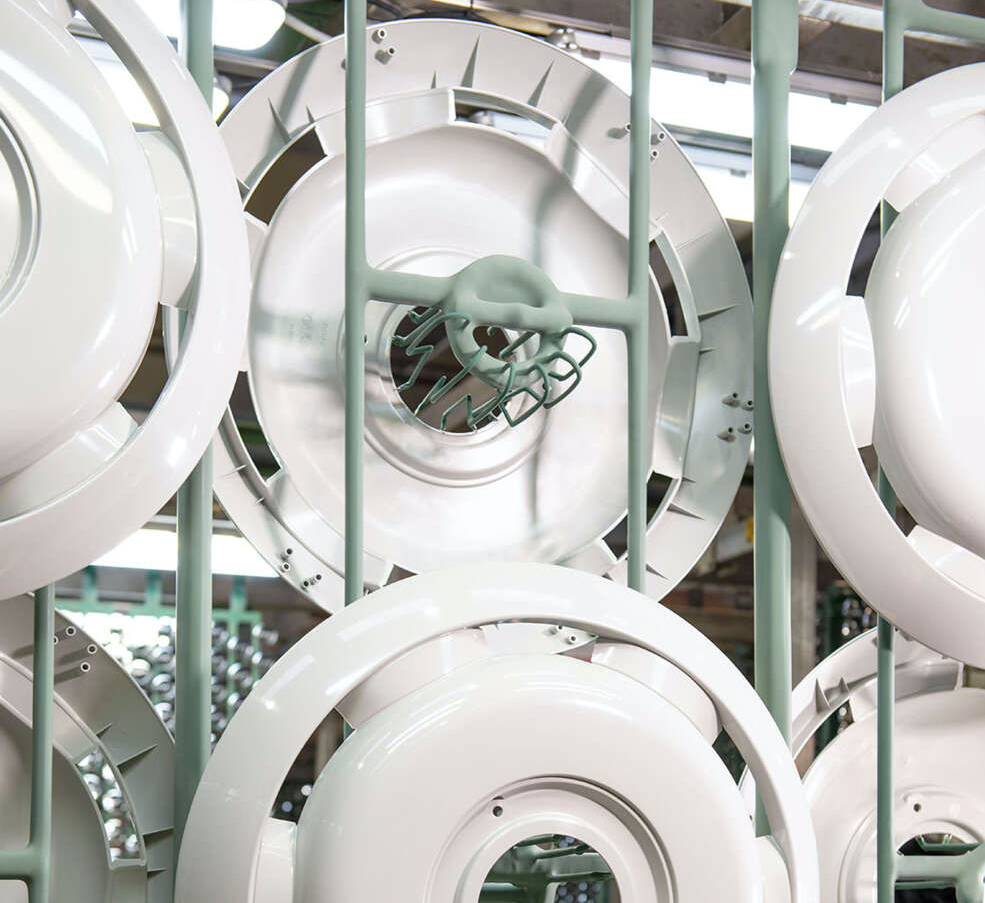
Un laboratorio all’avanguardia
Cinquantasei anni, nel mondo del lavoro da quando ne aveva quattordici, Mario Croda ha iniziato la sua attività professionale nel reparto di galvanica di una rubinetteria e oggi può vantare un know-how davvero significativo in questo segmento. Gli chiediamo di spiegarci perché sono così poche le realtà che si occupano di trattamento galvanico dei manufatti in plastica. «Applicare depositi sui materiali plastici è molto più complicato rispetto ai metalli e per ottenere risultati apprezzabili è necessario dedicare grande attenzione al controllo dei bagni galvanici. Non possiamo analizzarli una volta ogni quindici giorni sperando che tutto proceda per il meglio» spiega. «Ma non basta, perché anche il processo deve essere monitorato costantemente in ogni singolo aspetto. È quindi necessario dotarsi di un laboratorio molto attrezzato per garantire il massimo livello qualitativo. Il nostro – che riteniamo un fiore all’occhiello – dispone di sofisticate apparecchiature che ci permettono un’analisi pre-produzione della materia, step fondamentale per poter agire in modo mirato creando per ogni articolo un ciclo ad hoc». Apparecchiature che abbiamo ammirato da vicino durante la visita in Galvanoplast. Si tratta di macchine per eseguire test di sollecitazioni termiche (sia cicli termici sia shock termici), macchine per test di corrosione in nebbia salina, misuratori di spessore, sia metrici sia a raggi X, strumenti per la sezione metallografica senza inglobare con la resina, un microscopio a scansione elettronica e un microscopio digitale che arriva fino a 6.000 ingrandimenti.
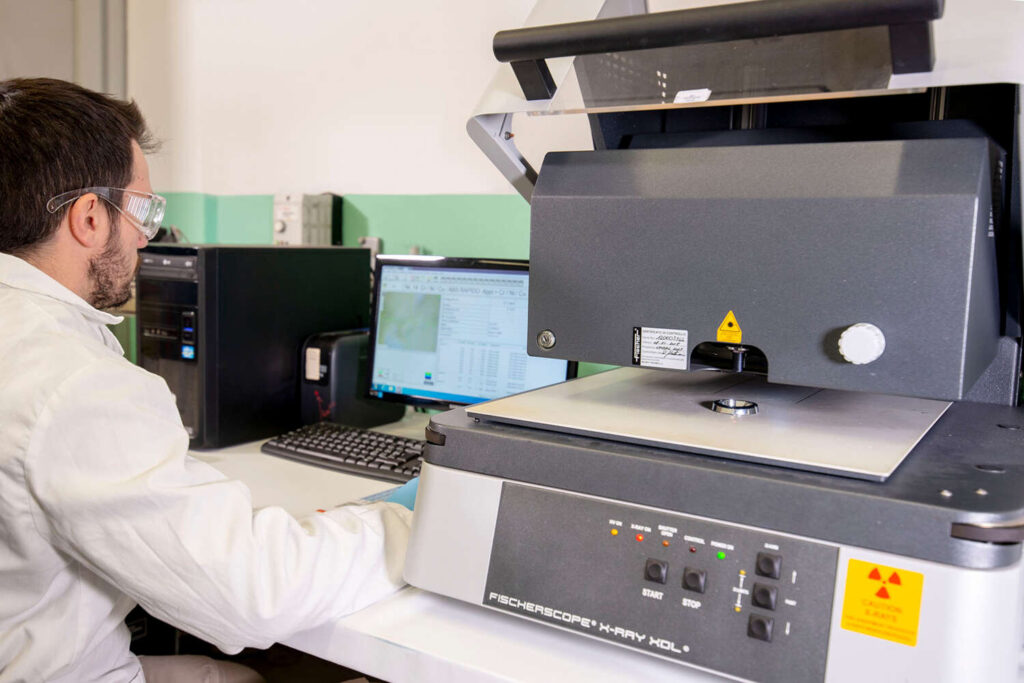
Altro vanto dell’azienda è l’imponente impianto galvanico formato da 108 posizioni (esclusa la linea di smetallizzazione dei telai) delle quali alcune per i trattamenti, altre per i lavaggi intermedi e l’asciugatura finale. Sopra le vasche, posizionate a U, su due linee parallele, scorrono su rotaie i carri ponte, i quali fanno avanzare le barre con i telai completi di pezzi in modo automatico, seguendo la sequenza e tempi di trattamento impostati mediante database integrato nel software. L’impianto è governato da un PC/software in cui vengono inseriti e richiamati i cicli di lavorazione e tutti i parametri necessari per effettuare la cromatura.
1.500 telai studiati ad hoc
Un particolare che non passa inosservato varcando il cancello della sede di Galvanoplast è il magazzino telai, collocato nell’ampio spiazzo prospiciente l’ingresso. Stipate una accanto all’altra, quelle indispensabili attrezzature per l’impianto statico appena descritto sono così tante da non riuscire a contarle. «Compresi i modelli stoccati all’interno di apposite strutture numerate e gestite da database, arriviamo a circa 1.500 esemplari ognuno dei quali studiato su misura per ogni prodotto da trattare, perché raramente un telaio può essere adattato a ricevere articoli diversi fra loro» precisa Mario Croda. «Anche il telaio, quindi, è un importante ingrediente della “ricetta” di lavorazione che impostiamo per tutte le tipologie di pezzo, insieme di parametri che poi vengono memorizzati per essere eventualmente ripetuti in seguito, quando il cliente ci invierà quello stesso pezzo».
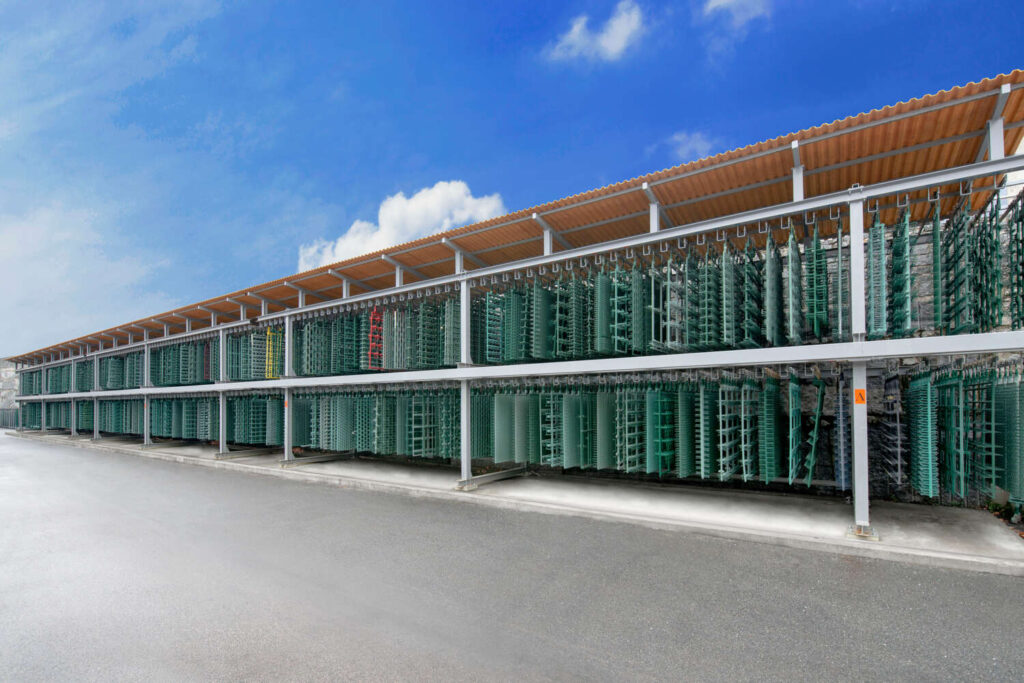
Anche sul fronte della sostenibilità ambientale l’impresa verbanese ha preso precise posizioni. «Da sempre abbiamo cercato di eliminare il più possibile le sostanze che possano risultare tossiche, e in quest’ottica siamo stati tra i pochi a eliminare l’ammonica dal trattamento di nichel chimico, fra l’altro con molti vantaggi in termini sia di esalazioni sia nel processo di depurazione. Per quanto riguarda quest’ultimo, ci avvaliamo di un impianto chimico-fisico a batch – non in continuo – con il quale trattiamo solo i prodotti concentrati; questo ci permette, nel caso in cui il processo di depurazione non dovesse risultare ottimale, di ripeterlo».
E in merito all’annosa questione del cromo esavalente e del cromo trivalente, come vi state comportando? «A chi continua a demonizzare il cromo esavalente faccio presente che, se utilizzato con i giusti criteri e precauzioni, non comporta alcun rischio» risponde Mario Croda. «Senza contare che è una delle sostanze più semplici da trattare in fase di depurazione, mentre le alternative non solo non lo sono, ma implicano consumi energetici di gran lunga superiori» conclude.