Nel processo di stiro-soffiaggio (SBM: Stretch – Blow Moulding) le preforme, precedentemente realizzate su una macchina a iniezione, sono riscaldate da lampade a raggi infrarossi, poi allungate per mezzo di un’asta di stiro e gonfiate con aria compressa, in modo da ottenere un orientamento biassiale delle molecole. Questa tecnologia è comunemente utilizzata per produrre contenitori in PET trasparenti di alta qualità, come le bottiglie per l’acqua.
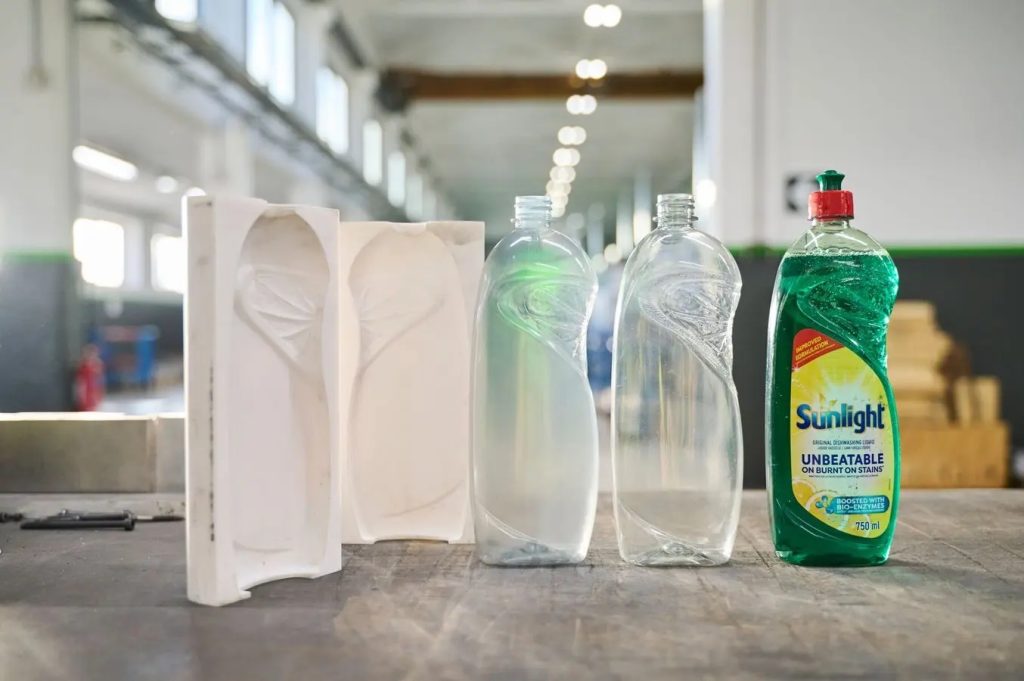
Gli stampi SBM sono tradizionalmente realizzati in metallo mediante lavorazione meccanica CNC, che richiede però attrezzature specializzate, software CAM e manodopera qualificata, con tempi di realizzazione di 4-8 settimane e costi che vanno da 2000 a più di 20000 euro.
Per rimanere un passo avanti alla concorrenza in questo settore in rapida evoluzione, la multinazionale Unilever e l’azienda bergamasca Serioplast hanno cercato metodi innovativi per accelerare la prototipazione e i test pilota. In quest’ottica, Stefano Cademartiri, responsabile del reparto CAD e prototipazione presso il dipartimento di ricerca e sviluppo di Unilever a Casalpusterlengo (Lodi), e Flavio Migliarelli, responsabile di design presso il dipartimento di ricerca e sviluppo di Serioplast Global Services, hanno lavorato fianco a fianco per testare l’idoneità degli stampi per SBM realizzati con la stampa 3D.
L’obiettivo della ricerca di Unilever e Serioplast è stato quello di sviluppare stampi modulari, in modo da accelerare lo sviluppo del prodotto, consentendo la fabbricazione rapida e a basso costo di prototipi di pre-produzione per i test pilota.
Stampi pilota con tempi e costi ridotti
Uno stampo pilota standard produce da 2000 a 5000 unità conformi alle specifiche estetiche e funzionali. Questi campioni vengono generalmente utilizzati per consumer test, test di linea e convalida dei processi.
Per creare tali stampi pilota, i team di Unilever e Serioplast hanno utilizzato le soluzioni di Formlabs e, in particolare: la stampante Form 3L, la Rigid 10K Resin e il software di preparazione della stampa PreForm, grazie al supporto di SolidManufacturing, azienda di SolidWorld Group, uno dei rivenditori Formlabs in Italia.
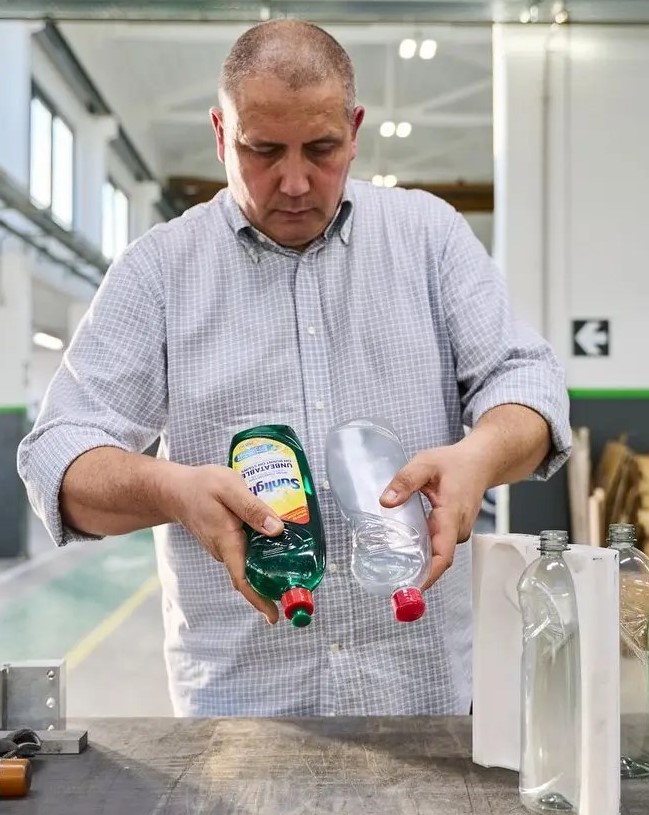
Serioplast ha testato circa 15 diversi modelli di flaconi, lavorando su due o tre iterazioni di design per ciascuno di essi. Con un solo stampo, realizzato in 3D utilizzando l’apposito materiale Rigid 10K Resin, sono state prodotte circa 200 unità senza compromettere lo stampo.
La qualità generale ottenuta è paragonabile, dal punto di vista estetico e funzionale, a quella di una produzione standard, tanto da poter sottoporre i flaconi a test di consumo. Si nota solamente un effetto finale leggermente opaco a causa della finitura superficiale meno spinta.
La stampa 3D consente di realizzare uno stampo in soli 2-4 giorni, permettendo di ridurre da sei a due settimane il tempo necessario per avviare i test di prototipazione.
Con le stampanti SLA di Formlabs e la Rigid 10K Resin, Unilever e Serioplast sono riuscite a ridurre i tempi di produzione del 70% e i costi delle attrezzature del 90% per produrre cicli pilota di 200 flaconi in PET in sole due settimane, adatti ai test di consumo.
Una marcia in più per garantire la competitività
Sviluppando un sistema modulare di attrezzature stampate in 3D, le due aziende sono ora in grado di esaminare più geometrie contemporaneamente, eseguire iterazioni e implementare rapidamente modifiche ai design dei flaconi senza notevoli costi aggiuntivi, accelerando inoltre le fasi di convalida e pre-produzione.
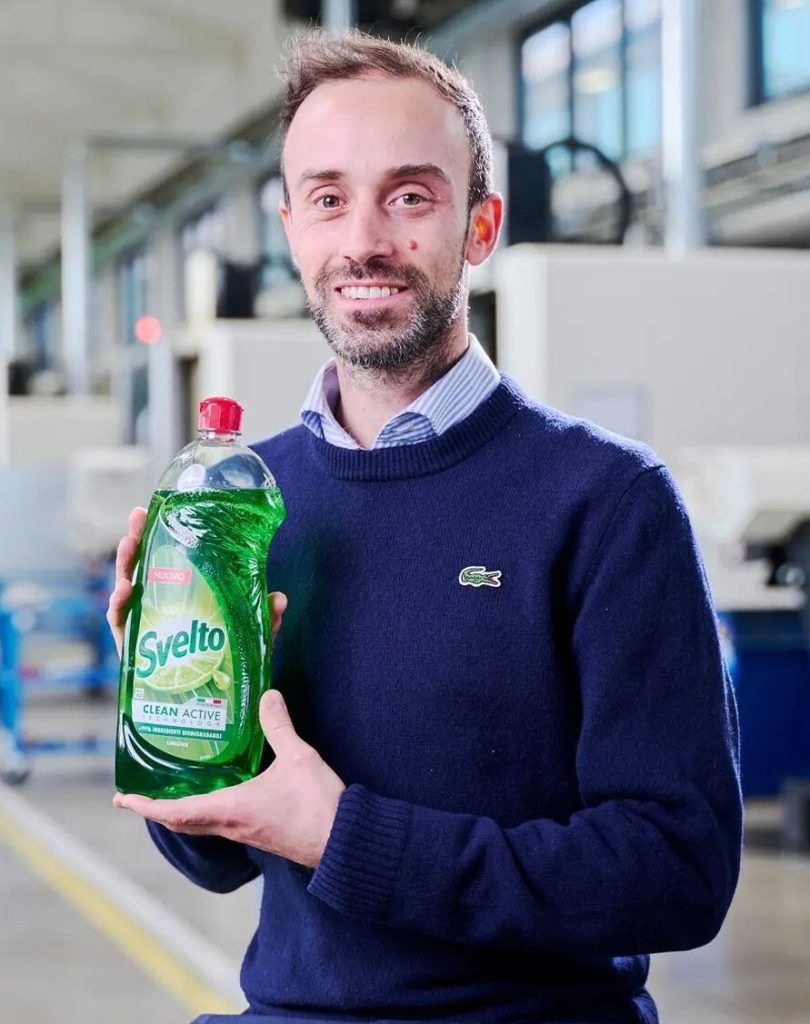
“Un’azienda di beni di consumo come Unilever deve essere sul mercato il prima possibile o prima della concorrenza, e offrire il miglior prodotto con il miglior prezzo in tempi estremamente rapidi. Le stampanti 3D di Formlabs ci aiutano a velocizzare questo processo”, ha quindi affermato Stefano Cademartiri.
“Con lo stampo realizzato in 3D, possiamo ridurre i tempi del 70% e i costi del 90% rispetto a uno stampo standard. Se in passato bisognava aspettare fino a 12 settimane per un solo design, ora possiamo realizzarne cinque”, ha aggiunto Flavio Migliarelli.
“Il nostro team di ricerca e sviluppo è costantemente al lavoro per realizzare nuovi materiali specializzati in grado di aprire nuove strade nella produzione, consentendo tanto alle grandi aziende, quanto alle piccole e medie imprese di innovare. Siamo quindi molto felici che le stampanti e i materiali Formlabs abbiano permesso a Unilever e Serioplast di sperimentare un nuovo workflow e non vediamo l’ora di conoscerne i prossimi sviluppi”, ha aggiunto Luca Valentino Colmi, product engineer a supporto della rete vendite di Formlabs.
“La competenza del team, unita alla tecnologia di stampa 3D Formlabs, ci ha permesso di mettere a punto una soluzione per la produzione industriale su misura, per soddisfare le richieste del cliente”, ha concluso Mirco Paltrinieri, Formlabs brand manager di SolidManufacturing.