I poliacetali (POM) offrono un’eccezionale combinazione di proprietà meccaniche, stabilità dimensionale e basso attrito, rendendoli protagonisti in una vasta gamma di applicazioni industriali, dall’automotive al medicale.
di Giovanni Lucchetta, Università di Padova
Le resine acetaliche, note anche come poliacetali o POM (poliossimetilene), sono termoplastiche ingegneristiche (tecnopolimeri) in grado di raggiungere un alto grado di cristallinità (70-75%), che conferisce loro elevate proprietà meccaniche. Sono spesso utilizzate per parti di precisione perché vantano un’eccellente stabilità dimensionale grazie alla loro bassa tendenza ad assorbire umidità, e mantengono una notevole resistenza all’urto anche a temperature molto basse (-50°C).
Dal punto di vista meccanico, offrono prestazioni di alto livello in termini di durezza, resilienza e rigidità, con una resistenza a trazione che si colloca tra le più elevate tra i tecnopolimeri (66-78 MPa). Le resine acetaliche si caratterizzano inoltre per buone proprietà dielettriche e un’ottima resistenza all’acqua bollente, ai solventi e agli idrocarburi, pur mantenendo una discreta resistenza ad acidi e basi. Presentano buone proprietà di scorrimento, resistenza all’usura e a fatica, oltre a un basso coefficiente d’attrito. La loro eccellente lavorabilità, unita alla natura fisiologicamente inerte che le rende idonee al contatto con gli alimenti, ne amplia ulteriormente le possibilità d’impiego.
Infine, pur non essendo principalmente noto per questa caratteristica, il poliacetale offre una discreta resistenza alla luce solare, migliorata ulteriormente dall’aggiunta di agenti stabilizzanti che contrastano l’effetto dannoso dei raggi UV. Nonostante la sua natura intrinsecamente opaca e bianca, dovuta alla struttura altamente cristallina, il POM può essere prodotto in diverse colorazioni. Tuttavia, è importante notare che i manufatti realizzati con questo materiale non possono essere verniciati successivamente; la colorazione avviene invece durante il processo di produzione, incorporando additivi coloranti direttamente nel compound fuso. La sua densità si aggira tra 1,41 e 1,43 g/cm³.
Applicazioni
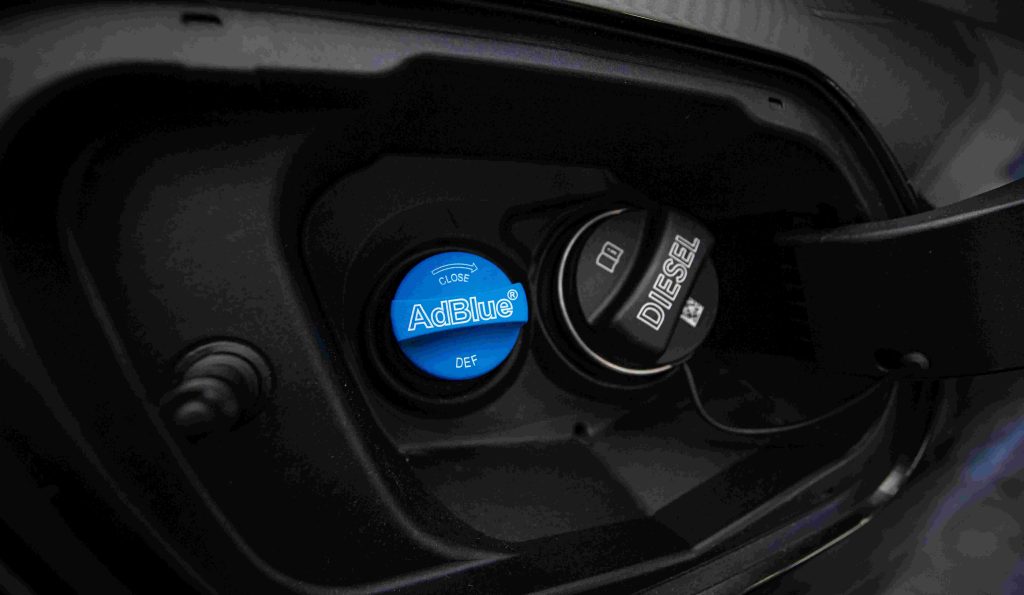
Le resine acetaliche trovano impiego in una vasta gamma di settori industriali, grazie alle loro proprietà uniche. La loro natura autolubrificante le rende particolarmente adatte per applicazioni nell’industria meccanica, dove sono utilizzate in componenti soggetti a sfregamento tra metallo e polimero, o tra polimeri.
Nel settore automobilistico, queste resine sono impiegate per la produzione di ingranaggi (vedi foto d’apertura, ndr), parti soggette a frizione e vari componenti a contatto con i carburanti (figura 1). Nell’industria elettronica, i poliacetali sono utilizzati in nastri trasportatori automatizzati e componenti di precisione, inclusi alcuni impieghi specializzati nell’ingegneria nucleare, sebbene il loro uso nell’industria elettrica sia limitato a causa della loro infiammabilità.
Le resine acetaliche trovano applicazione anche nel settore degli articoli sportivi e per il tempo libero (figura 2), nella produzione di beni di largo consumo, come chiusure lampo e posateria, e stanno guadagnando terreno nel settore medicale, particolarmente nell’implantologia dell’anca, grazie alla loro resistenza all’usura.
Staudinger e la nascita della chimica macromolecolare
La storia del POM inizia negli Anni Venti del secolo scorso con un chimico visionario di nome Herman Staudinger, il cui lavoro sui polimeri, e in particolare sulla polimerizzazione della formaldeide, ha rivoluzionato il mondo scientifico dell’epoca. Staudinger sfidò infatti le convinzioni del suo tempo. Mentre la maggior parte dei chimici credeva che i polimeri fossero semplicemente aggregati di piccole molecole, lui propose una teoria innovativa: i polimeri erano in realtà costituiti da lunghe strutture a catena, che chiamò macromolecole.
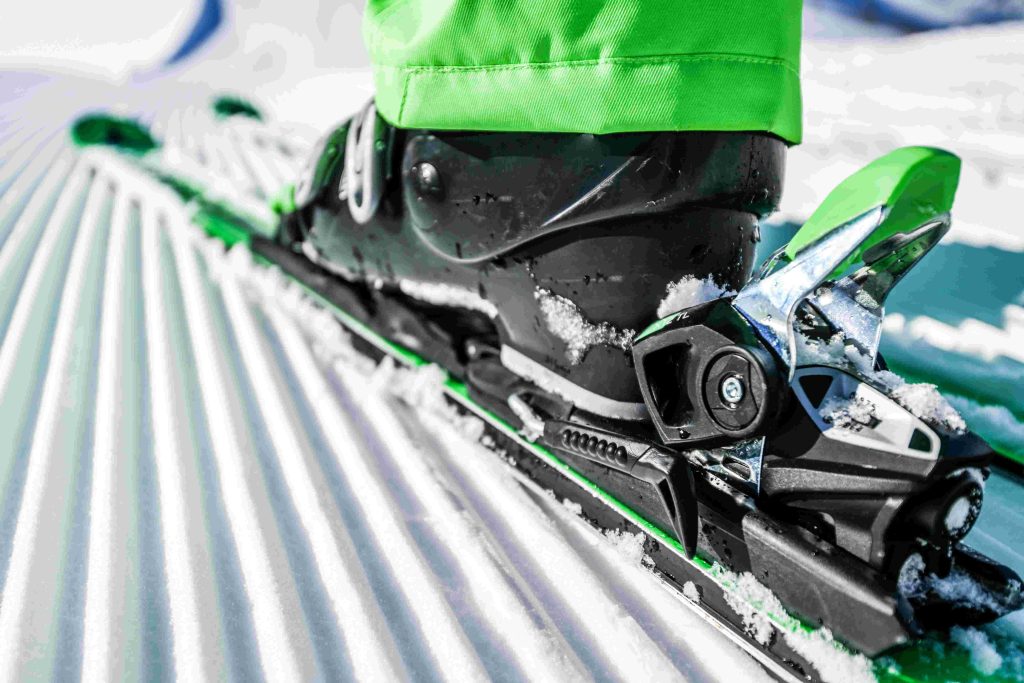
Per dimostrare la sua teoria, si concentrò sulla formaldeide, una molecola semplice capace di legarsi per formare un polimero. La sua scoperta fu rivoluzionaria: le catene polimeriche della formaldeide potevano essere più grandi dei cristalli che formavano. Questo concetto cambiò radicalmente la comprensione dei polimeri, introducendo l’idea che i componenti di base potessero essere più grandi della struttura complessiva che formavano. Per le sue scoperte nel campo della chimica macromolecolare, nel 1953 Staudinger venne insignito del Premio Nobel per la Chimica.
Tuttavia, nonostante l’importanza della scoperta di Staudinger, il polimero di formaldeide presentava un problema significativo: era termicamente instabile. Si decomponeva facilmente con il calore, rendendolo inadatto per applicazioni pratiche. Negli Anni Cinquanta, i chimici di DuPont ripresero la sfida della stabilizzazione della formaldeide e scoprirono che facendo reagire questo polimero con anidride acetica si otteneva un materiale sufficientemente stabile da resistere alla fusione e allo stampaggio. Questa svolta portò, nel 1960, al lancio dell’omopolimero Delrin da parte di DuPont. Già nel 1956, DuPont aveva depositato una domanda di brevetto per la protezione dell’omopolimero. Tuttavia, in questa richiesta, l’azienda omise di menzionare il termine “copolimero”, aprendo involontariamente la strada ai concorrenti per lo sviluppo di varianti del materiale. Quattro anni dopo, nel 1960, Celanese completò la propria ricerca indipendente sul POM copolimero e, a partire dal 1962, iniziò la produzione del Celcon, seguito un anno dopo dall’Hostaform.
L’effetto della copolimerizzazione
Le resine acetaliche si dividono quindi in due categorie principali: gli omopolimeri (POM-H) e i copolimeri (POM-C). Questa distinzione strutturale ha un impatto significativo sulle loro proprietà e applicazioni.
Gli omopolimeri sono come una successione perfettamente ordinata di unità ripetitive identiche, come quella riportata nel riquadro rosso della figura 3. La struttura uniforme conferisce loro una maggiore cristallinità, che si riflette nelle migliori proprietà meccaniche: sono circa il 15% più resistenti e il 13% più rigidi dei copolimeri, e presentano un’eccezionale resistenza all’usura. Queste caratteristiche li rendono ideali per parti soggette a frequenti attriti, come ingranaggi e boccole.

I copolimeri, d’altra parte, hanno una struttura più variegata e flessibile, perché circa il 2,5% della catena polimerica è composta da altri monomeri (il cosiddetto gruppo copolimero, segnato con il riquadro verde nella Figura 4). Questa diversità strutturale abbassa il loro punto di fusione di circa 10°C, offrendo una finestra di lavorazione più ampia e rendendoli meno sensibili alle variazioni di temperatura durante la produzione. Inoltre, la loro struttura, con maggiore spazio tra gli atomi di ossigeno, li rende notevolmente più resistenti alla degradazione in ambienti ostili, come in acqua calda, a contatto con prodotti chimici o solventi aggressivi. Questa resilienza li rende particolarmente adatti per applicazioni in idraulica e nel settore automobilistico, dove sono esposti a carburanti e fluidi tecnici.
Lavorabilità
L’elevata cristallinità del POM non gli conferisce solo migliori proprietà meccaniche (vedi tabella 1), ma garantisce anche una superiore resistenza ai solventi. Sebbene condividano con poliammidi e poliesteri una certa suscettibilità all’idrolisi, questo processo avviene più lentamente nei poliacetali, specialmente nei copolimeri. Questa caratteristica spiega perché, mentre poliammidi e poliesteri richiedono un’accurata essiccazione prima della lavorazione, la maggior parte delle resine acetaliche può essere stampata senza necessità di pre-essiccazione.
Il punto di fusione del POM è leggermente inferiore a quello delle poliammidi e dei poliesteri: 178°C per l’omopolimero e 165°C per il copolimero. Questo limita il range di temperatura in cui questi materiali possono essere impiegati e, considerando la loro suscettibilità all’ossidazione, la temperatura massima d’esercizio a lungo termine è limitata a 100-110°C. Tuttavia, presentano una temperatura di transizione vetrosa inferiore, ben al di sotto della temperatura ambiente. Questa caratteristica contribuisce al raggiungimento dell’alto grado di cristallinità, ma implica anche che le resine acetaliche possono continuare a cristallizzare a temperatura ambiente.
Questa cristallizzazione continua causa alcuni cambiamenti dimensionali, che possono protrarsi per 24-48 ore dopo lo stampaggio dei pezzi. È interessante notare che la cristallizzazione continua influenza anche lo sviluppo delle proprietà meccaniche, che possono evolversi per diverse settimane dopo lo stampaggio. Man mano che il polimero continua a cristallizzare, diventa più denso e rigido, il che può effettivamente modificare le dimensioni e la forma finali del pezzo. Questo aspetto è particolarmente rilevante per i progetti che necessitano di componenti con elevata precisione dimensionale.
Per gestire questo comportamento particolare, nello stampaggio a iniezione è fondamentale controllare la velocità di cristallizzazione attraverso l’impostazione della temperatura dello stampo (tra i 60 e i 130°C). Con un valore più elevato si favorisce una maggiore cristallizzazione del polimero mentre è ancora nello stampo. Questo approccio permette di anticipare gran parte del processo di cristallizzazione, riducendo così i cambiamenti dimensionali successivi alla formatura. È per questo motivo che nelle guide di progettazione per parti in POM si trovano spesso raccomandazioni a favore di temperature stampo elevate. L’obiettivo è ottenere le migliori prestazioni possibili dal pezzo e garantire che le dimensioni rimangano stabili nel tempo.
Infine, durante la lavorazione dei poliacetali, è essenziale mantenere la temperatura del fuso sotto i 220°C. Superare questa soglia può causare la decomposizione del materiale, con conseguente rilascio di formaldeide gassosa, un rischio da evitare assolutamente per garantire sicurezza e qualità del prodotto.
Rinforzi e additivi
Le proprietà delle resine acetaliche possono essere ulteriormente migliorate attraverso l’aggiunta di vari rinforzi e additivi per creare compound adatti ad applicazioni tribo-ingegneristiche. L’aggiunta di micro e nano particelle di politetrafluoroetilene (PTFE) si è dimostrata efficace nel ridurre il coefficiente di attrito e l’usura abrasiva, sebbene possa comportare una diminuzione delle proprietà meccaniche. Le fibre di vetro portano a un significativo miglioramento della resistenza e della rigidità, riducendo anche l’usura. Tuttavia, possono aumentare la rugosità superficiale e il coefficiente di attrito. Le fibre aramidiche, d’altra parte, non solo aumentano la resistenza in generale e quella all’usura in particolare, ma riducono anche il coefficiente di attrito. L’inclusione di fibre di carbonio nella matrice POM offre migliori proprietà di resistenza in generale e influisce positivamente sulla resistenza all’abrasione. Con l’aumento del contenuto di fibre, si osserva una riduzione del coefficiente di attrito e dell’usura.
Altri riempitivi utilizzati per migliorare le proprietà dei compositi di poliossimetilene includono il polietilene a bassa densità (LDPE), la fibra di legno, le particelle di rame e le fibre di basalto. Tutti questi filler modificano i compound acetalici con l’obiettivo di svilupparne la resistenza e le proprietà termiche e tribologiche. La scelta del riempitivo dipende dalle specifiche esigenze dell’applicazione, consentendo di personalizzare le proprietà del materiale per soddisfare requisiti specifici in vari settori industriali.
Le resine acetaliche presentano una sfida significativa nel campo della scienza dei materiali, in particolare per quanto riguarda la loro resistenza alla fiamma. La natura altamente infiammabile della formaldeide, componente base di questi polimeri, rende difficile conferire loro proprietà di autoestinguenza. Sebbene l’aggiunta di ritardanti di fiamma sia una possibile soluzione, questa strategia comporta il rischio di compromettere le proprietà meccaniche che rendono le resine acetaliche così apprezzate, come la rigidità e la resistenza all’usura.
La ricerca di additivi alternativi che non indeboliscano queste caratteristiche è stata intensa, ma finora non ha prodotto risultati ottimali. La situazione si complica ulteriormente considerando che non tutti i ritardanti di fiamma sono compatibili con i poliacetali. In particolare, quelli alogenati contenenti cloro o bromo sono da evitare assolutamente, poiché la loro combinazione con il POM allo stato fuso può generare reazioni estremamente pericolose. Questo problema evidenzia la complessità intrinseca nello sviluppo di materiali apparentemente semplici e sottolinea la necessità di un approccio equilibrato che tenga conto sia delle proprietà di autoestinguenza che delle caratteristiche meccaniche desiderate, evitando al contempo combinazioni potenzialmente rischiose con altri materiali.
(Articolo tratto dalla rivista Plastix di marzo 2025)