Il policarbonato è noto per la sua eccezionale combinazione di trasparenza ottica, elevata resistenza all’impatto, leggerezza e stabilità termica, che lo rende ideale per una vasta gamma di applicazioni, dall’elettronica all’automotive, dall’edilizia ai dispositivi medici.
di Giovanni Lucchetta, Università di Padova
Il policarbonato (PC) è un polimero termoplastico ingegneristico che presenta una combinazione unica di caratteristiche quali trasparenza ottica, tenacità (elevata resistenza agli urti), durezza, stabilità dimensionale, duttilità, elevata resistenza termica ed eccellente resistenza elettrica. Questi attributi del PC ne consentono l’impiego in un’ampia gamma di applicazioni, dai tipici articoli per la casa come le lenti degli occhiali e i supporti digitali (CD e DVD; vedi foto d’apertura, ndr) alle apparecchiature e agli accessori elettronici per l’industria automobilistica e aerospaziale, ai caschi e alle lenti dei fari.
Attualmente vengono utilizzati due metodi principali per la produzione di PC:
1. Polimerizzazione interfacciale bifasica per policondensazione di fosgene e bisfenolo A (figura 1a).
2. Transesterificazione allo stato fuso di difenilcarbonato e bisfenolo A, condotta a 300°C e bassa pressione (figura 1b).
Il primo metodo, noto anche come “processo al fosgene” o “processo interfacciale”, è il più ampiamente utilizzato nella produzione industriale per diverse ragioni: maggiore efficienza produttiva, migliore controllo sul peso molecolare del polimero, temperature di reazione più basse (tipicamente intorno ai 20-40°C) e capacità di produrre PC di qualità superiore, con meno impurità.
Tuttavia, vale la pena notare che il secondo metodo, noto anche come “processo senza fosgene”, ha guadagnato attenzione negli ultimi anni a causa delle preoccupazioni ambientali relative alle materie prime fosgene e cloruro di metilene utilizzate nel processo interfacciale. Mentre il processo al fosgene rimane dominante, alcuni produttori stanno investendo nello sviluppo e nell’industrializzazione su larga scala del metodo di transesterificazione per risolvere i problemi ambientali e di sicurezza associati all’uso del fosgene, che è un gas estremamente tossico.
Le proprietà uniche dei policarbonati
Il PC è una resina termoplastica amorfa con una temperatura di transizione vetrosa di 145°C – 150°C. Ha un’eccellente trasparenza, una trasmittanza della luce dell’87%-91% e un indice di rifrazione di circa 1,586. L’amorfismo e la trasparenza del PC sono attribuibili alla rigidità della sua catena molecolare, costituita da anelli benzenici (arilici o fenilici) con i gruppi metilici (CH3) che fungono da “cunei” (figura 1). La disposizione dei voluminosi anelli benzenici è nettamente diversa da quella del polistirene ed è il motivo per cui il PC possiede proprietà meccaniche superiori a quelle dei polimeri commodity; proprietà che lo fanno entrare di diritto nella famiglia dei polimeri ingegneristici, o tecnopolimeri.
A differenza di altre plastiche, gli ingombranti anelli benzenici della sua catena e i gruppi metilici incuneati tra gli anelli conferiscono rigidità e impediscono lo slittamento della catena. Ricordiamo che la resistenza di un materiale polimerico alla deformazione è infatti legata alla capacità delle sue catene di opporsi allo scorrimento delle une sulle altre. Proprio come accade quando sciogliamo un nodo, lo scorrimento dei capi delle corde è tanto più agevole quanto più questi sono flessibili: per sfilarsi passando attraverso il nodo ciascun capo deve flettersi.
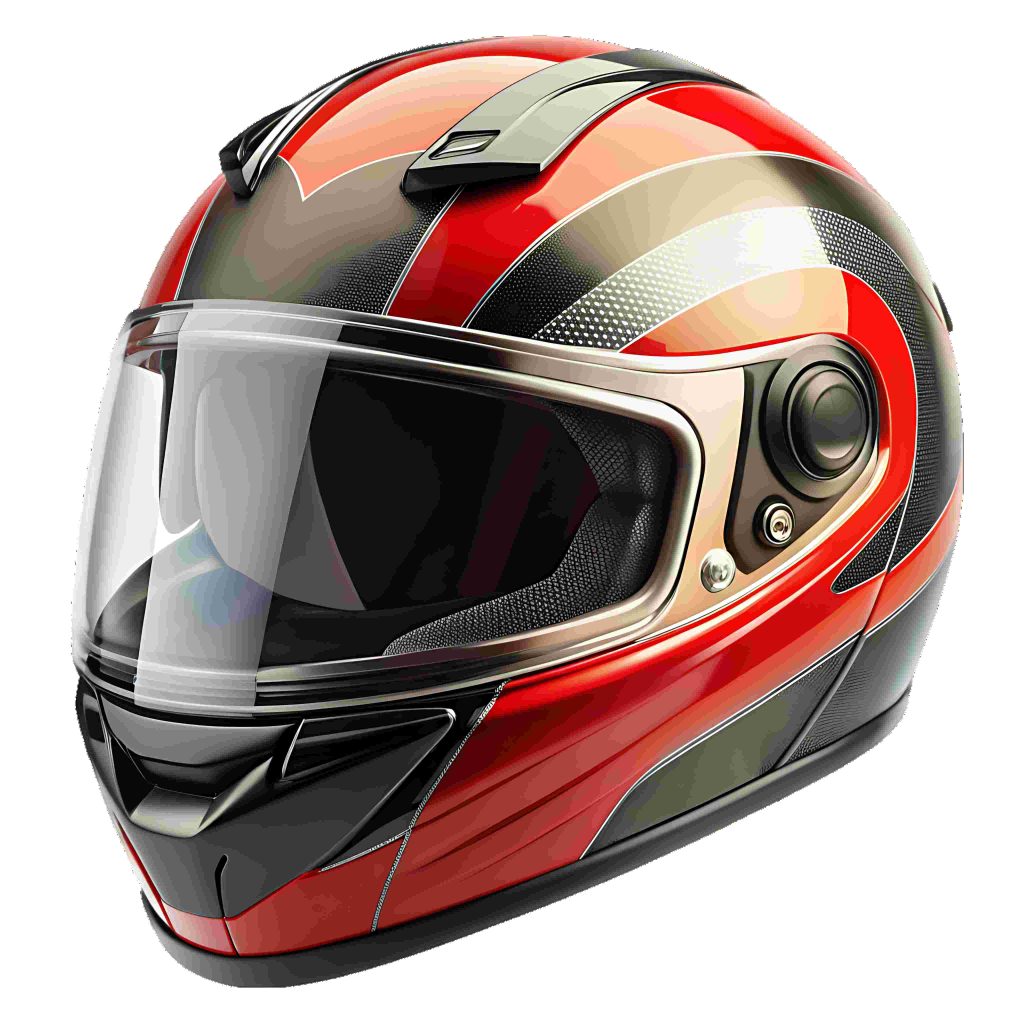
La densità relativamente bassa del PC, pari a 1,20-1,22 g/cm3, gli conferisce una rigidità specifica e proprietà meccaniche specifiche molto competitive. Anche in questo caso è utile ricordare che il prezzo d’acquisto di un materiale è valutato al peso, mentre le sue performance sono basate sul volume (spessore) impiegato. A parità di proprietà, le plastiche leggere risultano quindi più competitive.
L’eccezionale tenacità del policarbonato è uno dei suoi maggiori vantaggi (figura 2). I valori di resilienza Charpy con e senza intaglio (acN e acU), riportati in tabella 1, indicano che questo polimero vanta una resistenza agli urti eccezionalmente elevata, anche rispetto a termoplastici con rinomate proprietà d’impatto come l’ABS. Il PC presenta una resilienza molto elevata ed è praticamente infrangibile in assenza di intagli (N).
Il policarbonato ha un’ottima resistenza al calore. Ha un elevato punto di rammollimento ed è stabile a temperature comprese tra -170°C e 126°C. La temperatura di deflessione termica (HDT) del PC a 1,82 MPa è di 132°C e la sua temperatura di utilizzo in continuo (CUT) è di 126°C.
Il PC è fisiologicamente inerte e può essere sterilizzato con tecniche di sterilizzazione a vapore, con ossido di etilene, o mediante raggi gamma. È quindi molto utilizzato nel settore biomedicale con numerose formulazioni certificate disponibili per applicazioni mediche.
L’applicazione del PC per uso alimentare è facilitata dalla sua trasparenza, dall’elevata temperatura di deflessione termica, dalla resistenza agli urti e dalla possibilità di essere utilizzato nei forni a microonde.
Fin qui abbiamo elencato i punti di forza del policarbonato. Quali sono i suoi punti deboli?
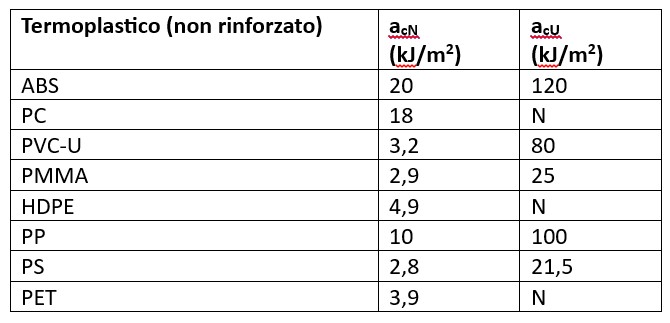
Il PC ha alcune limitazioni in termini di resistenza chimica, soprattutto rispetto agli alcali e ad alcuni solventi organici. Dimostra una buona resistenza in molte altre situazioni. Ad esempio, regge bene contro molti acidi diluiti, oli, grassi e persino alcuni idrocarburi. Non ha problemi con l’acqua fredda o le soluzioni saline, il che lo rende adatto a numerose applicazioni quotidiane. È importante considerare che la resistenza chimica del PC può variare notevolmente a seconda di fattori come la temperatura, la concentrazione dell’agente chimico e il tempo di esposizione. Se lo confrontiamo con altri polimeri, come il polietilene o il polipropilene, il PC potrebbe sembrare meno resistente in alcuni scenari. Tuttavia, l’industria ne ha sviluppato gradi speciali con resistenza chimica migliorata, dimostrando che è possibile superare alcune di queste limitazioni.
La scelta del colore: non solo una questione estetica
L’aggiunta di colore può avere un impatto significativo sulla resistenza della resina di base del policarbonato. Il grado di variazione nella resistenza all’impatto dipende da diversi fattori: il colore specifico scelto, la composizione chimica utilizzata per crearlo e la quantità di colorante aggiunto. Gli effetti sulla duttilità del materiale sono più evidenti nei campioni che presentano intagli. Questo fenomeno è particolarmente rilevante poiché molti componenti in policarbonato possono presentare geometrie complesse con potenziali punti di concentrazione degli sforzi. Per i progettisti e i produttori che lavorano con il policarbonato, queste considerazioni sono fondamentali. La scelta del colore non è solo una questione estetica, ma può influenzare significativamente le prestazioni meccaniche del prodotto finale.

Il policarbonato è generalmente considerato un materiale con una buona resistenza agli agenti atmosferici. Tuttavia, presenta una vulnerabilità significativa nell’esposizione prolungata ai raggi ultravioletti (UV). Questa sensibilità ai raggi UV può causare un graduale ingiallimento del materiale nel tempo, compromettendone non solo l’aspetto estetico ma anche, in alcuni casi, le proprietà meccaniche.
Un esempio molto comune di questo fenomeno è visibile nei fari anteriori delle automobili (figura 3). La maggior parte delle lenti dei fari è realizzata in PC grazie alla sua eccellente trasparenza, leggerezza e resistenza agli urti. Tuttavia, dopo alcuni anni di esposizione costante alla luce solare, è frequente notare come le lenti dei fari tendano ad ingiallire e ad opacizzarsi. Questo non riduce solo l’efficacia dell’illuminazione, compromettendo potenzialmente la sicurezza di guida, ma influisce anche negativamente sull’estetica del veicolo. Per applicazioni di lungo termine all’aperto, il policarbonato richiede una fortificazione contro i raggi UV. Questo può essere ottenuto attraverso l’aggiunta di stabilizzanti agli UV nella formulazione del materiale, o mediante l’applicazione di rivestimenti protettivi.
Infine, val la pena di ricordare che uno dei primi e più significativi fallimenti nell’uso del policarbonato si verificò nell’industria dei piccoli elettrodomestici, quando il materiale venne impiegato per produrre componenti regolarmente a contatto con acqua calda. Inizialmente, gli effetti a breve termine di questo contatto sembravano trascurabili. Tuttavia, con il passare del tempo e l’esposizione ripetuta, il materiale cominciò a infragilirsi e a sviluppare crepe. Questo fenomeno, noto come idrolisi, comporta la rottura dei legami delle catene polimeriche, con conseguente riduzione significativa della duttilità del materiale.
Lavorabilità
Il PC può essere lavorato e “post-trattato” con tutte le tecniche di lavorazione standard per polimeri termoplastici. Alle temperature di lavorazione tipiche del PC fuso, piccole quantità di umidità possono provocare la degradazione dei legami per idrolisi e la conseguente scissione delle catene, con riduzione del peso molecolare e di altre proprietà fisiche. Per ridurre l’umidità residua al di sotto dello 0,01-0,02%, è necessaria un’essiccazione a 120°C per almeno 4 ore.
La struttura macromolecolare del PC gli conferisce un’elevata viscosità e, di conseguenza, nello stampaggio richiede elevate pressioni d’iniezione e rapporti relativamente bassi tra distanza di flusso e spessore di parete dei pezzi stampati. Essendo amorfo, il PC presenta un ritiro abbastanza uniforme nelle direzioni parallela e perpendicolare al flusso di riempimento ed è quindi adatto per pezzi di elevata precisione, che richiedono una deformazione minima. I bassi valori di ritiro (dallo 0,6 allo 0,8%) contribuiscono al diffuso utilizzo del PC nello stampaggio a iniezione di precisione, ad esempio di parti per applicazioni ottiche ed elettriche.
Le temperature a cui lavorare il polimero fuso nello stampaggio a iniezione variano da 280 a 320°C. La temperatura dello stampo deve essere impostata tra gli 80 e i 120°C. L’utilizzo di stampi a temperature elevata durante lo stampaggio del policarbonato è fondamentale, principalmente per ridurre le tensioni interne nel pezzo finale. Questo aspetto è cruciale per garantire la qualità e le prestazioni ottimali del prodotto. Quando si condizionano gli stampi a temperature più basse, il raffreddamento più rapido che ne consegue genera livelli più elevati di tensioni interne nel pezzo stampato. Questo fenomeno si verifica principalmente a causa di due fattori:
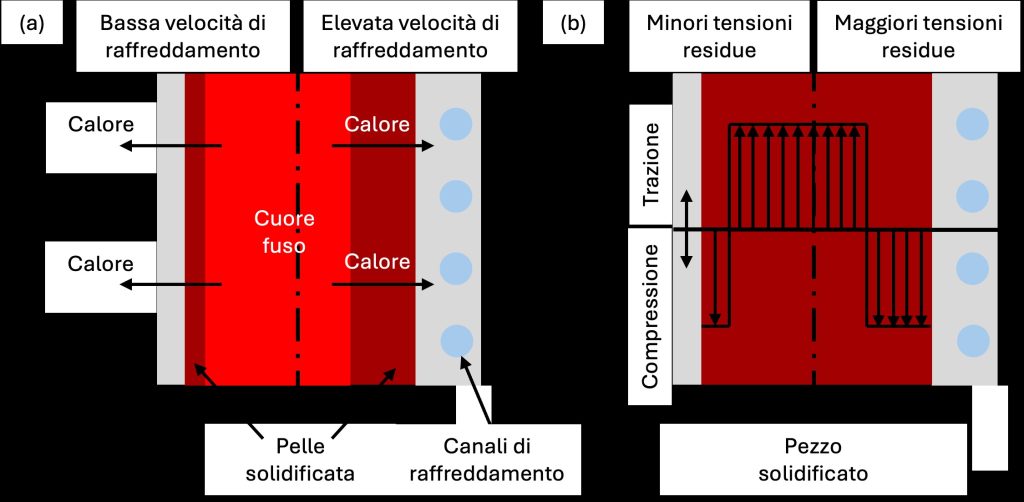
a) Differenze nel raffreddamento: gli strati esterni del componente stampato, che sono a diretto contatto con la superficie dello stampo (la “pelle”), si raffreddano più rapidamente di quelli interni allo spessore (il “cuore”), creando tensioni residue.
b) Orientamento molecolare: negli strati esterni, le molecole tendono a orientarsi parallelamente alla superficie dello stampo, mentre all’interno rimangono orientate più casualmente.
Il primo fattore è preponderante e dipende dal fatto che le materie plastiche, incluso il PC, sono cattivi conduttori di calore. La diversa velocità di raffreddamento tra pelle e cuore comporta un ritiro differenziale che genera tensioni tra gli strati (figura 4a): la pelle solidifica subito e smette di ritirarsi, dato che è in equilibrio termico con lo stampo; il cuore, invece, si raffredda più lentamente continuando a ritirarsi e cercando di trasferire il ritiro anche alla pelle. Il risultato è una distribuzione di tensioni residue che vede il cuore in trazione e la pelle in compressione (figura 4b). L’utilizzo di uno stampo a bassa temperatura accentua questa differenza nella velocità di raffreddamento, esacerbando il problema delle tensioni residue dovute al ritiro differenziale.
Inoltre, questo problema diventa più significativo man mano che aumenta lo spessore delle pareti del pezzo. Questo fenomeno si manifesta in modo particolarmente evidente nel policarbonato attraverso quello che è noto come “spessore critico”. Tale problema, ben documentato nel PC, si manifesta come una drastica riduzione della resistenza all’impatto (e in particolare della resistenza all’impatto Izod con intaglio) all’aumentare dello spessore della parete dei campioni di prova (tipicamente quando supera i 6-8 mm).
È interessante notare come l’utilizzo di stampi più caldi produca pezzi con proprietà migliori anche quando si utilizza un polimero amorfo come il policarbonato, sebbene il fenomeno non sia ovviamente dovuto alla formazione di una struttura cristallina. Questo prova ancora una volta che, quando si ha a che fare con le materie plastiche, il modo in cui il processo di lavorazione viene impostato può influire significativamente sulla performance finale del pezzo stampato (ad es. sulla tenacità del PC). Progettisti e ingegneri non possono basare i loro calcoli di dimensionamento solo sui valori delle proprietà riportati nelle schede tecniche dei materiali, ma devono considerare come quei valori possano cambiare in funzione del processo, dello stampo e della geometria del componente.
Purtroppo, l’abitudine a ridurre la temperatura degli stampi è molto diffusa ed è motivata dalla ricerca spasmodica del minimo tempo ciclo, che si traduce nella massimizzazione della produttività della pressa di stampaggio. Tuttavia, vorrei far notare che in molti casi è possibile aumentare la temperatura dello stampo mantenendo costante il tempo ciclo attraverso la riduzione della temperatura del fuso polimerico. Spesso, infatti, la temperatura del fuso viene aumentata per compensare una temperatura dello stampo troppo bassa, seguendo un approccio non ottimale.
Il modo migliore per evitare di spendere tempo ciclo extra nel rimuovere calore dal materiale è, in realtà, non introdurre questo calore in eccesso fin dall’inizio del processo. In altre parole, anziché aumentare la temperatura del fuso per compensare uno stampo freddo e poi dover raffreddare il pezzo più a lungo, è più efficiente ottimizzare la temperatura dello stampo. Uno stampo mantenuto alla temperatura corretta permette di lavorare con temperature del fuso più basse, riducendo così il tempo necessario per il raffreddamento del pezzo. Inoltre, questo approccio può portare a ridurre significativamente il consumo energetico complessivo del processo.
(Articolo tratto dalla rivista Plastix di febbraio 2025)