All’insegna dello slogan “We live moulding” (“Noi viviamo lo stampaggio”), il 19 e il 20 giugno, nella Marx Halle di Vienna, il Gruppo Wittmann ha presentato ai suoi circa mille ospiti un’ampia gamma di prodotti high-tech, tra cui sei macchine per lo stampaggio a iniezione. Diverse altre isole di stampaggio erano poi esposte nello stabilimento Wittmann Battenfeld di Kottingbrunn.
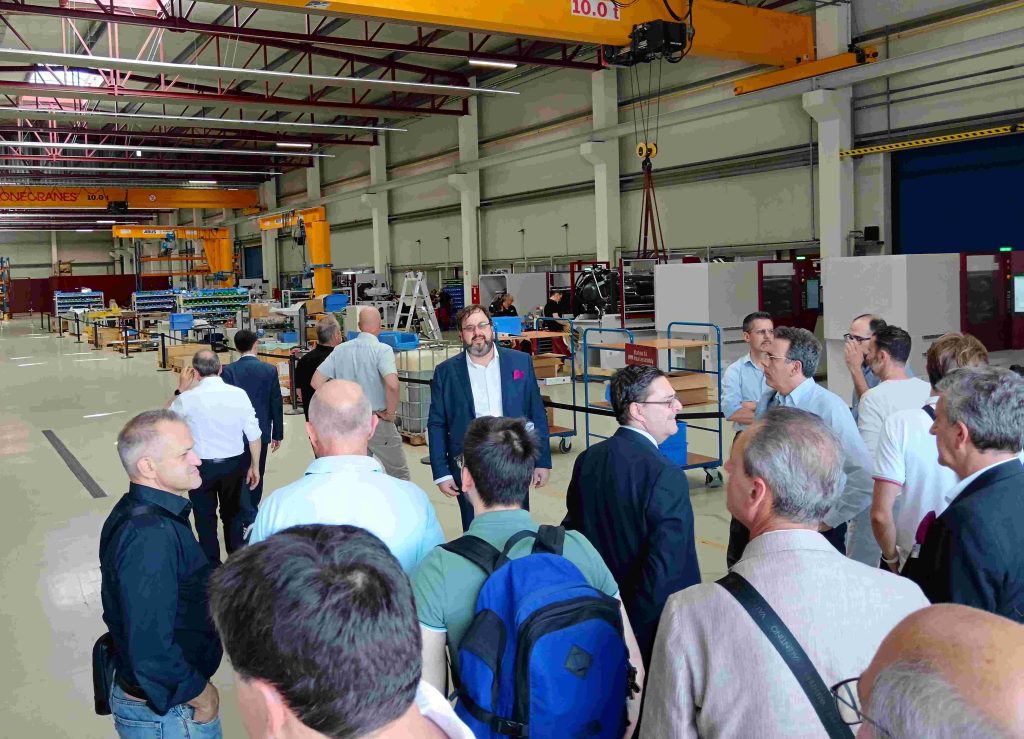
Ma il viaggio organizzato appositamente da Wittmann per i circa 60 clienti italiani e per i giornalisti della stampa specializzata (tra cui naturalmente la redazione di Plastix) è iniziato il 19 giugno, toccando innanzitutto lo stabilimento di Wittmann Hungária. Nato nel 1998, quest’ultimo è dedicato principalmente alla produzione e al collaudo di piccoli robot (il più grande è il W928, con 15 kg di portata massima) e sprue picker (robot preleva materozze), oltre a termoregolatori e flussimetri, da circa due anni.
Inoltre, attualmente si assemblano qui circa sei presse alla settimana, in dipendenza dal modello e, da poco, anche i relativi quadri elettrici, con schede Com-X per l’assistenza delle presse a iniezione. Infine, nello stabilimento ungherese sono oggi possibili anche alcune lavorazioni a CNC dei piani portastampo e vengono prodotti circa 700 telai pressa ogni anno.
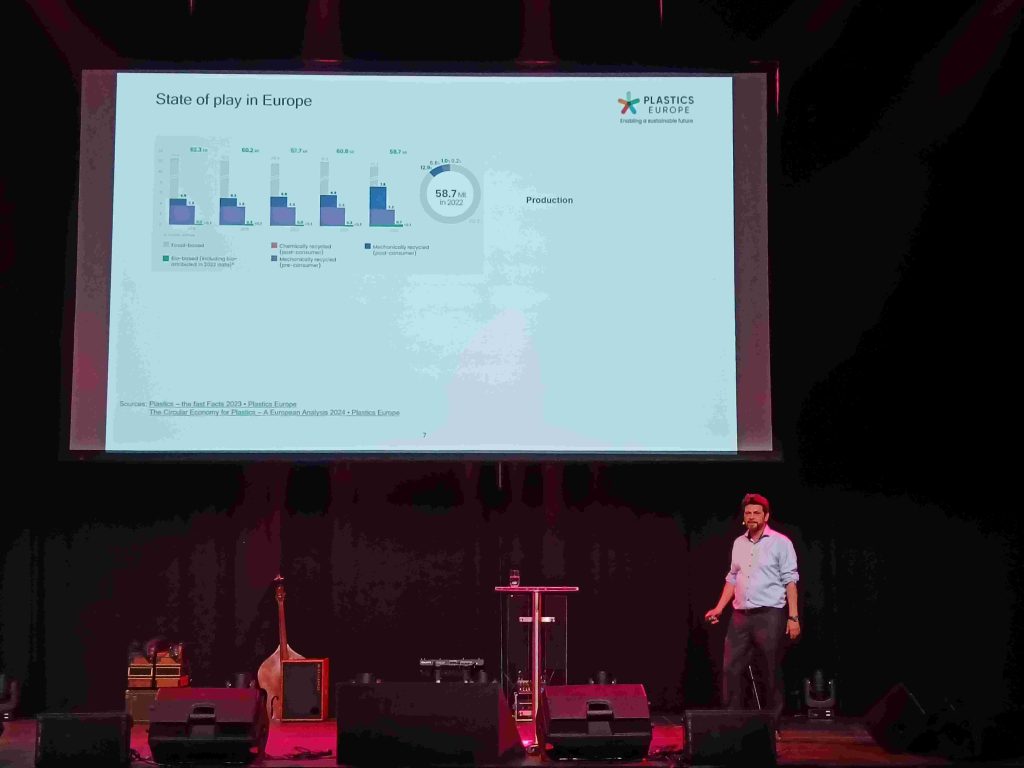
La comitiva italiana si è poi trasferita nella già citata Marx Halle di Vienna per osservare da vicino le macchine esposte, ma anche per assistere alla presentazione tema dell’evento “AI and Digitalization – The gamechangers for the plastics industry”, a cura di Alexander Kronimus, direttore generale ad interim di Plastics Europe Germany.
Il giorno seguente, 20 giugno, è invece iniziato con la visita allo stabilimento produttivo viennese del Gruppo Wittmann, dedicato soprattutto alla costruzione di robot di grandi dimensioni con le più moderne tecnologie di lavorazione meccanica e logistica.
La mattinata si è conclusa con la visita al quartier generale di Wittmann Battenfeld a Kottingbrunn, dedicato principalmente alla costruzione di presse orizzontali con forze di chiusura oltre le 180 t, che si vanno ad aggiungere alle macchine verticali, a due piani e ai molti altri modelli interessanti della casa austriaca, tra cui le MicroPower per il microstampaggio a iniezione.
Ma, tornando all’ampia esposizione di macchine e sistemi ausiliari presso la Marx Halle di Vienna, in questa occasione il Gruppo Wittmann ha dimostrato soprattutto il suo elevato livello di competenza nei settori della digitalizzazione, dell’efficienza energetica, dell’automazione e del microstampaggio.
Digitalizzazione
Nell’area dedicata alla digitalizzazione – tema importante anche nelle relazioni tecniche dei Competence Days – era in mostra una cella di produzione Wittmann 4.0, nonché sistemi di assistenza per ottimizzare il processo d’iniezione, e Holoverse, lo studio concettuale di Wittmann che si occupa di controllo vocale e “realtà mista”.
La cella di produzione Wittmann 4.0 si basava su una macchina servoidraulica SmartPower B8X 60/350, che stampava morsetti in policarbonato utilizzando uno stampo a quattro cavità fornito dalla società austriaca Lechner. Grazie a questa isola di stampaggio completamente integrata è stato possibile illustrare in modo efficace le caratteristiche più vantaggiose del collegamento in rete tramite Wittmann 4.0, come ad esempio la scheda tecnica digitale per garantire un avvio regolare della produzione e il pacchetto software Temi+ MES.
Inoltre, la macchina era dotata dei pacchetti software HiQ: HiQ Flow, HiQ Melt e HiQ Metering. HiQ Flow è un sistema di regolazione dell’iniezione che si basa sulla viscosità del materiale, in grado di compensare gli effetti delle variazioni di temperatura e lotto (batch) sulla viscosità del materiale, al fine di ottenere uno standard di qualità stabile per le parti stampate.
HiQ Melt serve invece a monitorare la qualità del materiale e a consentire l’intervento in caso di deviazioni dai valori desiderati. HiQ Metering è la designazione di una funzione di chiusura attiva della valvola di ritegno (check valve), volta a garantire che ad ogni stampata venga iniettata esattamente la quantità di materiale richiesta, per ottenere la massima costanza di peso del pezzo.
Al fine di evitare sprechi di materiale plastico, pezzi di materozza e parti difettose appositamente prodotti a scopo dimostrativo sono stati rigranulati nel granulatore S-Max 2 di Wittmann e quindi rinviati nuovamente alla tramoggia della macchina tramite il dispositivo di trasporto con vuoto collegato al granulatore. I morsetti finiti erano rimossi da un robot W918, sempre di Wittmann, e inseriti in sacchetti tubolari utilizzando una confezionatrice fornita dall’azienda italiana Ravizza Packaging.
Il futuro della digitalizzazione è stato poi illustrato da Holoverse: uno studio sulle possibilità moderne e intuitive d’interazione tra macchine a iniezione e robot per la rimozione dei pezzi. In pratica, è stata dimostrata la possibilità di controllo vocale e gestuale, tramite realtà aumentata, di una SmartPower B8X 120/350 servoidraulica, dotata di un sistema di controllo Unilog B8 e di un robot W918 con controllo R9. A scopo dimostrativo, questa macchina stampava un cestino per il pranzo.
Numerosi altri sistemi ausiliari esposti nella Marx Halle erano inoltre integrati e supportati con una presentazione in realtà aumentata tramite Holoverse.
Efficienza energetica, sostenibilità, economia circolare
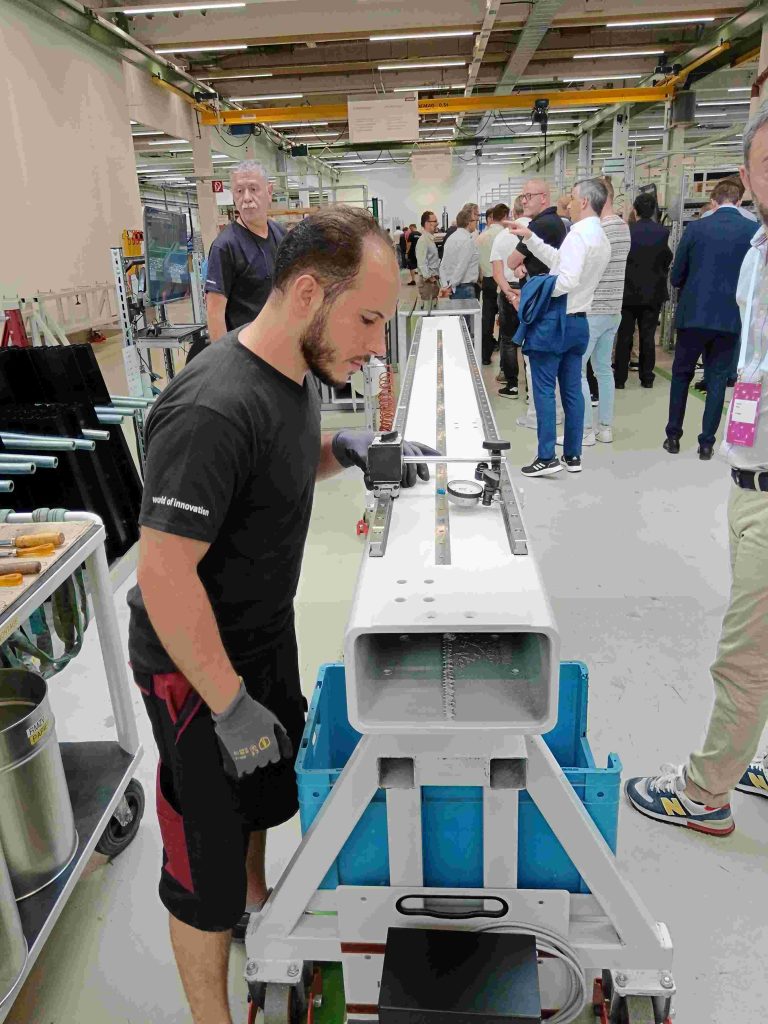
La competenza del Gruppo Wittmann in tutti gli aspetti dell’efficienza energetica, della sostenibilità e dell’economia circolare è stata dimostrata grazie a due macchine della serie completamente elettrica EcoPower.
In primo luogo è stata presentata una EcoPower B8X 180/750+ in versione DC, a corrente continua. Questa macchina – che funziona tramite un accumulatore di energia solare costituito da una tecnologia ultramoderna ed ecologica di batterie al sale su base nichel-sodio, fornita da innovenergy – è progettata come modello “Insider”. Ciò significa che il robot e il nastro trasportatore sono integrati nell’isola di lavoro, all’interno di apposite protezioni.
Il sistema è attrezzato con un robot WX142 e di un termoregolatore Wittmann Tempro plus D, entrambi alimentati tramite il circuito DC intermedio della macchina. Su questa macchina veniva prodotto un coperchio in polipropilene, utilizzando uno stampo a due cavità. La batteria utilizzata per alimentare il sistema ha una capacità complessiva di oltre 45 kWh, più che sufficiente per il funzionamento continuativo della macchina durante un’intera giornata. Per compensare i picchi di carico a breve termine della pressa a iniezione, vengono utilizzati condensatori elettrochimici aggiuntivi noti come supercondensatori o “supercaps”, per integrare le unità di stoccaggio a nichel-sodio.
La seconda EcoPower, modello B8X 110/525, è progettata con un granulatore integrato (“ingrinder”), per facilitare un efficiente riciclo in linea di materozze e scarti. La macchina stessa eccelle per l’estremo dinamismo e la facilità d’uso; caratteristiche dovute alla cinematica a ginocchiera altamente dinamica, alle unità d’iniezione ad altissima velocità, al sistema di controllo B8X sviluppato internamente con frequenza di clock aumentata e all’unità d’iniezione orientabile (pivottante).
Su questa macchina, dotata di robot integrato WX90 per la rimozione della materozza (“sprue picker”), scivolo “drop-out”, granulatore senza griglia S-Max e regolatore di flusso WFC120, veniva stampato un supporto per rete da arrampicata, utilizzando uno stampo a 8 cavità fornito sempre da Lechner. Le materozze erano rimosse dal WX90 e alimentate direttamente al granulatore integrato, dove venivano macinate e quindi reimmesso nel processo.
Automazione
Ai Competence Days il Gruppo Wittmann ha dimostrato anche la propria competenza nella progettazione di sistemi d’automazione complessi, grazie a una SmartPower B8X 90/350 servoidraulica dotata di una cella d’automazione sviluppata e prodotta da Wittmann Battenfeld Germany.
Su questa macchina veniva prodotta una livella in ABS con uno stampo a 1+1 cavità fornito da Sola (Austria). Nella prima fase di produzione, venivano stampate a iniezione le parti superiore e inferiore dell’alloggiamento della livella. La parte superiore veniva quindi depositata e decorata su una stazione laser. Contemporaneamente, la parte inferiore, posizionata su un vassoio, veniva dotata di fiale per la bolla, prodotte sempre da Sola. Successivamente la parte superiore veniva premuta su quella inferiore mediante una forza preimpostata. I pezzi finiti erano poi trasportati verso una stazione di testing, dove il posizionamento delle fiale veniva controllato da un sistema di visione. Dopo il controllo di qualità, le livelle finite venivano rimosse e depositate su un nastro trasportatore da un robot WX138.
Microstampaggio a iniezione con nanostrutture
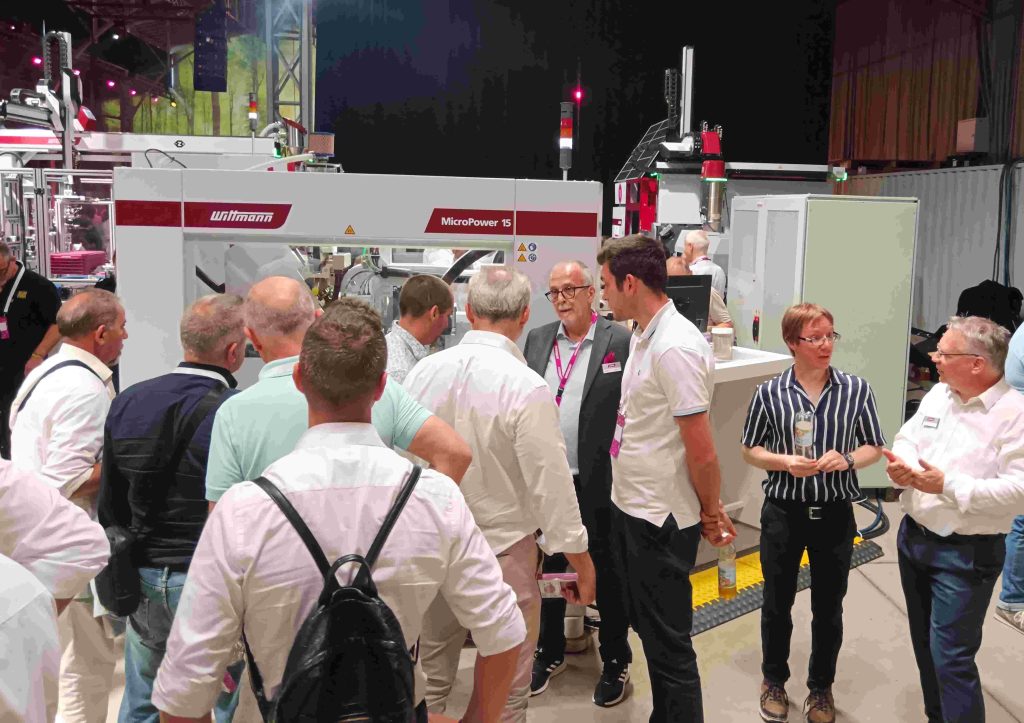
Infine, il Gruppo Wittmann ha presentato ai Competence Days le proprie capacità nel campo del microstampaggio a iniezione. La pressa MicroPower, progettata per lo stampaggio a iniezione di micro e nano parti, era dotata di un’unità d’iniezione a due fasi, a vite e pistone, mediante la quale è possibile iniettare materiale fuso termicamente omogeneo con volumi d’iniezione compresi tra 1,2 e 6 cm3. In questo modo è possibile realizzare pezzi di elevata precisione con un processo di produzione estremamente stabile e con tempi di ciclo minimi. Alla Marx Halle di Vienna, Wittmann ha mostrato la produzione di piastrine dimostrative su una MicroPower 15/10, utilizzando uno stampo a 4 cavità con nanostrutture prodotte mediante stampa 3D, provenienti dalla società NanoVoxel (Austria).
Riccardo Ampollini