Nella miriade di componenti presenti su una normale vettura circolante, il ricoprimento sottolunotto del bagagliaio è sicuramente uno dei meno evidenti in ottica cliente. In effetti, storicamente, per le vetture berlina (3 volumi o Sedan), tale componente è solo un rivestimento estetico interno abitacolo, conosciuto storicamente con il nome di cappelliera, di difficile accesso perché posto dietro gli appoggiatesta della seconda fila sedili, quindi spesso di scarso utilizzo e di dimensioni ridotte. Assume invece maggiore importanza con l’introduzione delle vetture a 2 volumi o dei monovolume, perché permette di nascondere il contenuto del bagagliaio dall’esterno vettura a portellone chiuso e costituisce un vero e proprio piano di appoggio a portellone aperto e chiuso. Con l’affermarsi delle vetture a 2 volumi (hatchback) e successivamente dei monovolume (ad esempio i SUV), la cappelliera esce quindi dall’ambito del solo rivestimento interno vettura, per diventare nel tempo anche un elemento di comfort acustico (filtro dei rumori presenti nel bagagliaio verso l’abitacolo), oltre che di protezione e appoggio. In questo modo crescono gli sforzi e le attenzioni dedicate al singolo specifico componente, che risulta anche sollecitato in modo severo, data l’installazione corrente a sbalzo tra due mensole e al calore in arrivo attraverso la superficie vetrata del lunotto posteriore.
Cappelliera o rollo tendina?
Una volta scoperto che le vetture moderne, siano esse Hatchback o SUV, hanno necessariamente questo componente, non fosse alto che per evitare il forzamento del portellone posteriore dovuto al tentativo di furto di quanto presente nel bagagliaio, se non è nascosto da qualcosa a vettura chiusa e incustodita, possiamo addentrarci nelle mille scelte stilistiche e contenutistiche delle diverse proposte. Sui SUV o sulle vetture station wagon è abbastanza comune l’adozione di un telo di copertura (rollo tendina) più o meno ricco, automatizzato e rifinito. Il materiale di base del telo è un tessuto polimerico con spalmatura di resine viniliche (PVC), cuciture estetiche, meccanismi, irrigidimenti localizzati e maniglie plastiche e/o tessili di manovra (fettucce). Il meccanismo di apertura/chiusura può essere manuale o automatizzato e permettere aperture complete o parziali per uno sfruttamento modulare del vano di carico, con attenzione all’ergonomia dell’operazione e all’accessibilità completa o ridotta del bagagliaio. La ricercatezza e preziosità del materiale utilizzato per il telo, unite alle complicazioni dei meccanismi di apertura e chiusura, magari motorizzati, rappresentano le possibili declinazioni del componente installato sul modello base a quello applicato sulle luxury cars.
La funzione di filtro della rumorosità del bagagliaio verso l’abitacolo risulta attenuata e meno efficiente, ma il rollo tendina rappresenta l’unica soluzione pratica di copertura del bagagliaio al crescere delle dimensioni dello stesso, perché una cappelliera rigida sarebbe troppo pesante, ingombrante, poco pratica e costosa. Si uniscono così le richieste di copertura del bagagliaio con quelle di praticità e facile accesso a vani di carico di dimensioni ragguardevoli. Con l’introduzione delle vetture medie e medio piccole a 2 volumi, dove il rollo tendina non è applicabile e, anzi, sarebbe eccessivamente costoso, si è registrato il vero e proprio boom delle cappelliere rigide a sbalzo tra le due mensole laterali montate sui fianchi del bagagliaio e il corredo dei due tiranti laterali per facilitare l’accesso al vano bagagliaio.
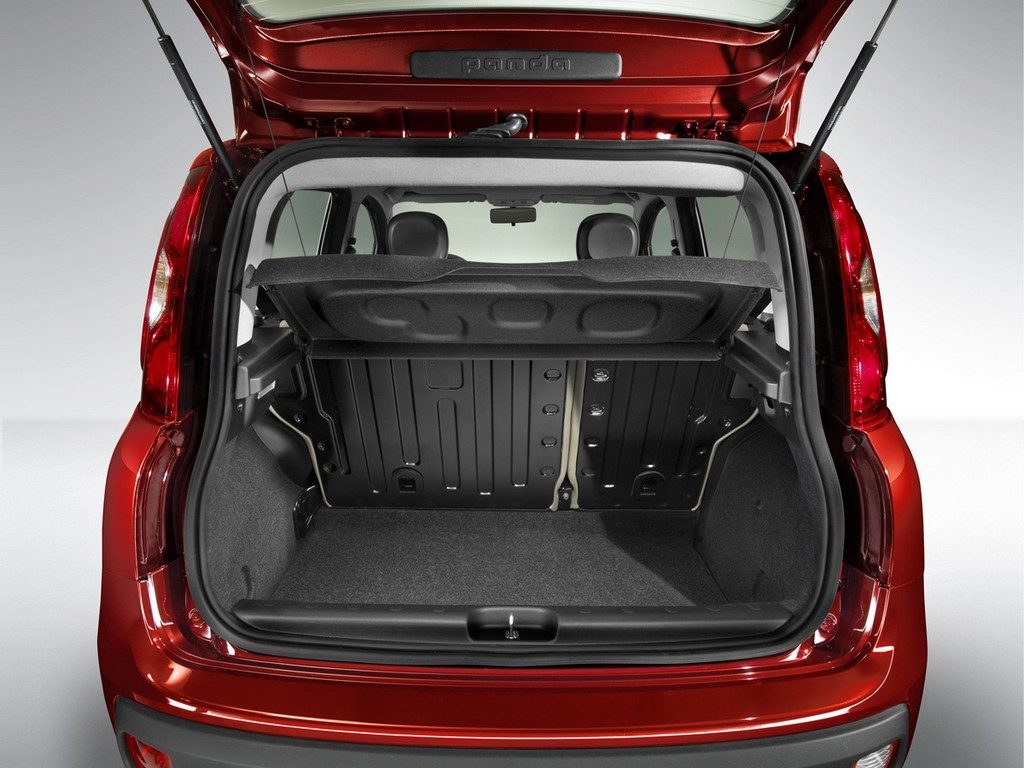
La cappelliera diventa rigida
A parte alcune iniziali esperienze nell’utilizzo di materiali poliolefinici rinforzati talco stampati a iniezione per il contenimento dei costi, come nel caso della Fiat Panda prima serie, da subito si sono cercate delle lastre poliolefiniche compatte estruse in testa piana, da rivestire con tessuto e da trasformare tramite termoformatura. Le cappelliere della Fiat Uno prima e seconda serie sono state prodotte con lastre in polipropilene rinforzato con farina di legno e quindi rivestite con tessuti coordinati agli interni. Da allora è iniziata una lunga storia, prima in Fiat e poi in FCA, di questi materiali e della relativa tecnologia, con il continuo sviluppo e affinamento di mescole, attrezzature di trasformazione e tessuti adeguati alle specifiche richieste tecnologiche ed estetiche.
Le diverse soluzioni industriali
Esistono tradizionalmente diversi materiali adatti alla tecnologia di termoformatura, via via applicati sulle vetture FCA. Una prima classe è rappresentata da lastre con matrici di materiali termoindurenti o in poroso, come storicamente avvenuto per la cappelliera della Fiat Ritmo e oggi presente su alcune applicazioni del mercato NAFTA. Tali soluzioni sono oggi un po’ trascurate, perché non permettono la riciclabilità del materiale a fine vita vettura pur consentendo la realizzazione di componenti funzionalmente validi ed esteticamente gradevoli.
La seconda classe di materiali è rappresentata dall’uso del poliuretano schiumato in stampo con rinforzi metallici. Anche in questo caso, la soluzione, ancora molto presente sulle vetture dei costruttori francesi, è oggi resa critica dalle nuove esigenze sempre più stringenti di riciclabilità dei componenti. Il poliuretano infatti, essendo un termoindurente, non può essere riciclato e il suo smaltimento, data la presenza al suo interno dei rinforzi metallici di difficile estrazione e separazione, non è assolutamente agevole. A questa oggettiva difficoltà, vanno aggiunte le complicazioni del processo produttivo, perché il rivestimento della cappelliera deve avvenire di ripresa con l’utilizzo di adesivi, con conseguente aggravio dei costi.
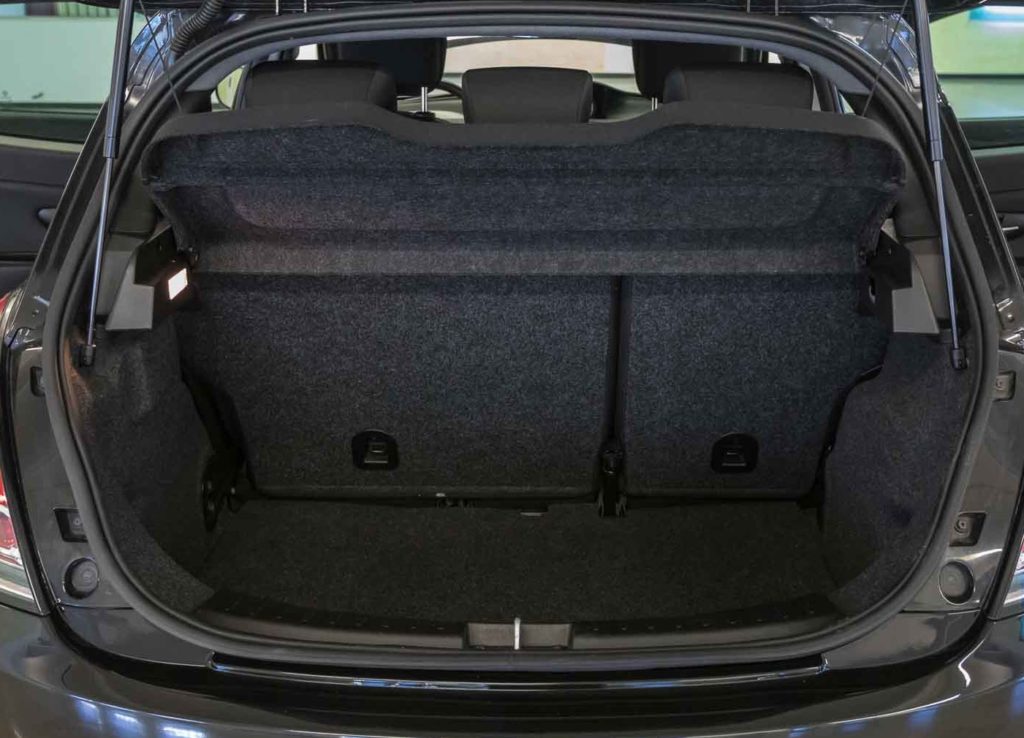
La terza classe di materiali è costituita dalle storiche lastre compatte in polipropilene e farina di legno con o senza la presenza di bacchette metalliche di rinforzo integrate. L’attuale Jeep Renegade adotta una mescola più volte aggiornata di questo tipo di materiale con la presenza dell’inserto metallico di rinforzo, mentre la Lancia Y terza serie ha una geometria tale da non richiedere alcun irrigidente aggiunto. Per anni si è sempre voluto nascondere la presenza di queste lastre in vettura, nobilitandone entrambe le facce con l’aggiunta di materiali tessili estetici, ma negli ultimi anni, sulla scia di una maggiore attenzione all’ambiente e ai materiali “bio” in senso lato, molti costruttori hanno deciso di lasciare scoperta la faccia inferiore del componente, mettendo in risalto la presenza nel polipropilene della farina di legno come motivo estetico.
Un esempio di tale indirizzo stilistico per FCA è rappresentato dalla cappelliera della Fiat Panda terza serie, che non ha nessun rivestimento sul lato affacciato al vano di carico, rendendo in tal modo estetica una superficie tecnica. Un ulteriore interessante esempio di impiego degli stessi materiali poliolefinici con farina di legno è rappresentato dalla cappelliera dell’Alfa Giulietta.
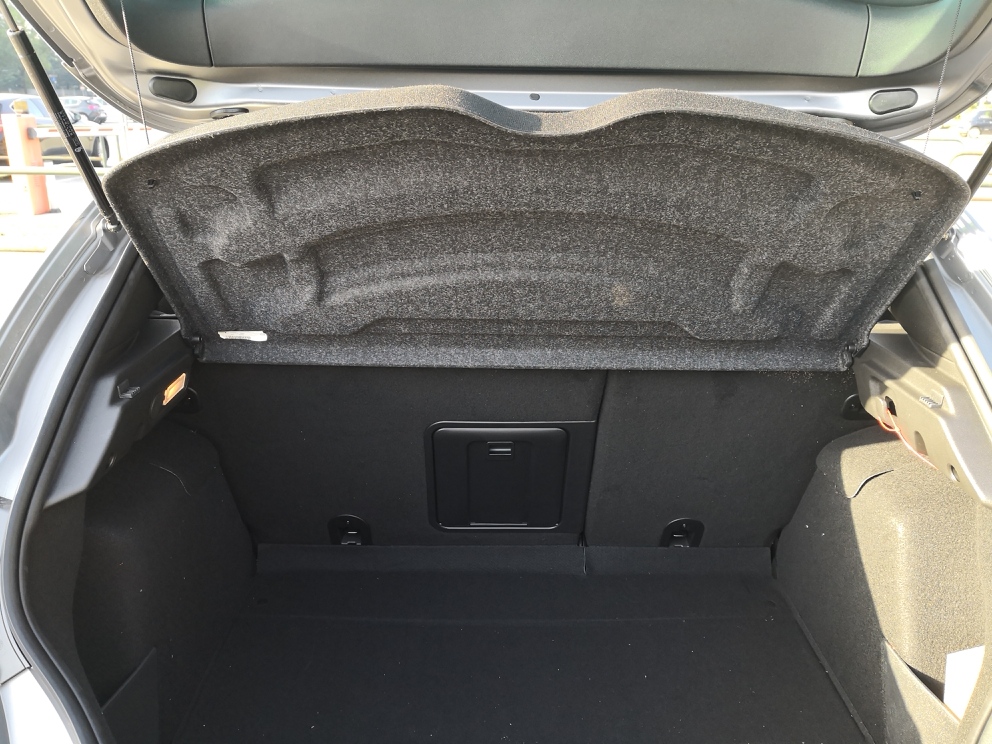
Data la rilevante distanza tra gli appoggi in vettura e il grande sviluppo longitudinale, non è stato possibile utilizzare la solita soluzione di una sola lastra termoformata con o senza rinforzo metallico, ma è stato necessario adottare la scelta di doppia lastra termoformata con l’ausilio del gas (nel caso specifico aria compressa), che ha permesso la creazione di tutti gli irrigidimenti di forma necessari, localizzati direttamente nello stampo di termoformatura one-shot. Il risultato è stato una cappelliera medio grande, a peso ridotto per la mancanza di inserti metallici, ma sufficientemente robusta per superare tutti i requisiti del capitolato di qualificazione. Nel caso di cappelliere di forme o installazioni particolarmente sfidanti si adotta invece un’ulteriore classe di lastre poliolefiniche compatte, rinforzate con fibra di vetro anziché con farina di legno. A partire dalla cappelliera della Fiat 500 si sono via via affinate le mescole e i processi produttivi che hanno portato ai materiali oggi utilizzati come prima applicazione sulla Fiat 500 X, oltre che su moltissime vetture del mercato tedesco (tra cui, ad esempio, la VW T Roc). Tali lastre compatte rinforzate con fibra di vetro stanno sostituendo alcune classi di materassini agugliati in polipropilene rinforzato con fibra di vetro, un tempo utilizzati da case costruttrici tedesche e oggi in via di sostituzione anche per l’elevato costo di acquisto del materiale semilavorato.
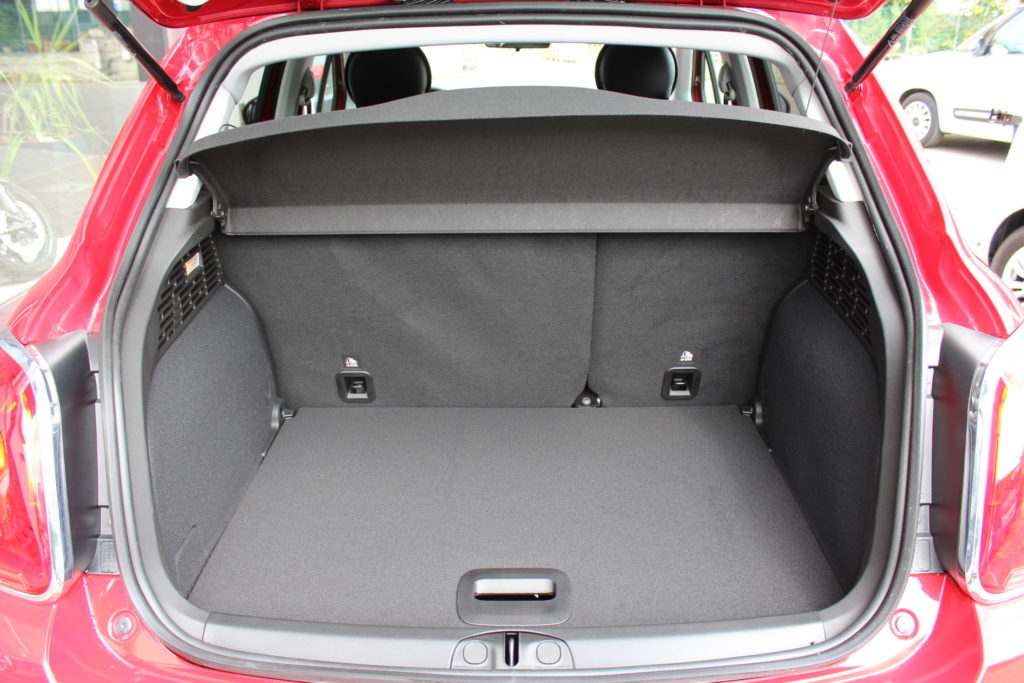
La sfida del futuro
I trend per i materiali futuri si concretizzano sostanzialmente in due famiglie che derivano dalle tecnologie con cui viene prodotto il materiale semilavorato da utilizzare. La prima è costituita dalle lastre compatte estruse in testa piana che vedono il quotidiano aggiungersi di mescole poliolefiniche sempre più sofisticate, nonché l’introduzione di rinforzi in fibra vegetale o minerale più performanti rispetto alla tradizionale farina di legno. Tali materiali, che continueranno a essere trasformati tramite termoformatura, avranno performance resistenziali migliorate e permetteranno di eliminare i rinforzi metallici e di ridurre gli spessori delle lastre necessarie, con conseguente diminuzione di peso a parità di funzionalità del componente.
L’altra famiglia, più costosa ma ugualmente promettente, è costituita da una nuova generazione di materassini agugliati in polipropilene rinforzato con fibre di vetro o naturali, che saranno un’ulteriore evoluzione di alcuni prodotti già presenti e utilizzati, volti a ridurne i costi e minimizzarne alcune criticità storiche, come l’affioramento della fibra e la sua contattabilità sul prodotto finito da parte del cliente finale. Tali sviluppi dovranno anche tenere conto della tensione sempre più importante verso la riduzione dei pesi e dei costi, con l’adozione, oltre che di materiali di supporto leggeri e poco costosi, anche di rivestimenti tessili adeguati alle nuove richieste, ma comunque estetici e di arredamento. Su alcune vetture della concorrenza si riscontrano già cappelliere costituite da un solo telo tessile, tenuto in tensione e in forma da un filo metallico perimetrale che costituisce la sola parte resistenziale del componente. Tale soluzione, pur essendo assolutamente valida in termini di contenimento dei costi e non disprezzabile come resa estetica, non coglie assolutamente le performance richieste di filtro della rumorosità del bagagliaio e di autoportanza per l’appoggio di oggetti sul componente. Tali scelte andranno attentamente valutate in fase di sviluppo della vettura nell’assegnazione dei profili di missione richiesti a ogni componente in ottica di utilizzo cliente.
I futuri scenari legati all’elettrificazione sempre più spinta del parco circolante, alle esigenze di riduzione di costi e pesi, al ridotto impatto ambientale dei materiali, ma soprattutto al mantenimento della tradizionale attenzione di FCA allo stile e alla personalizzazione della vettura da parte del cliente, rappresentano l’ennesima sfida nella direzione dell’innovazione e della ricerca di nuovi materiali e di nuove tecnologie.