Un tema poco affrontato, ma certamente importante per le aziende trasformatrici di materie plastiche, è quello riguardante la durata delle attrezzature produttive. Come sottolinea Eugenio Pederzolli di Nickerson Italia: “Un’attrezzatura che dura più a lungo significa un maggiore risparmio per l’utilizzatore, ma anche un ridotto impatto ambientale”. Vediamo come questi due concetti trovano applicazione pratica nel caso di Omfi, azienda briantea attiva nello stampaggio di articoli tecnici
di Riccardo Ampollini
Con sede a Camparada (Monza-Brianza), Omfi è nata nel 1963 come officina meccanica per lo studio, la progettazione e la costruzione di stampi e varie tipologie di attrezzature. “Dalla fine degli Anni Sessanta, stampiamo anche articoli tecnici in materiale plastico”, racconta il fondatore di Omfi Isaia Frigerio, intervistato dalla redazione di Plastix insieme al figlio Gianpietro, amministratore delegato della società. “Abbiamo però mantenuto la costruzione di stampi, seppure solamente per uso interno”.
“Attualmente possiamo contare su 11 presse a iniezione, principalmente di Haitian e Negri Bossi”, esordisce Gianpietro Frigerio. “Le altre sono state quasi tutte sostituite nel corso degli anni”. La progettazione del prodotto avviene anche su disegno del committente e la ricerca dei materiali più idonei (spesso innovativi) garantisce la massima ottimizzazione della fase di stampaggio.
I materiali utilizzati
“Come accennato, Omfi ha sempre prodotto articoli tecnici, utilizzando soprattutto tecnopolimeri e gomma”, prosegue Isaia Frigerio.
“Abbiamo realizzato articoli per vari designer italiani e, ad esempio, per Giugiaro abbiamo testato praticamente tutti i tecnopolimeri di DuPont, quali Nylon (PA), Rynite (PET), Hytrel (TPE) ecc. Inoltre, abbiamo lavorato con ottimi materiali di Sabic, Covestro e Solvay (oggi Syensqo). Nel caso della produzione di lampade, ci è pure capitato di dover selezionare materiali e additivi anti UV per ottenere un’adeguata resistenza alla luce”.
“In sintesi, abbiamo stampato tutti i migliori tecnopolimeri esistenti in commercio, testandoli per ciascuna specifica applicazione e lavorando anche a progetti particolari”, aggiunge Gianpietro Frigerio. “Vorrei inoltre sottolineare il fatto che utilizziamo solo materiali di prima scelta e certificati”.
I settori applicativi: arredamento, automotive, elettronica
La maggior parte della produzione Omfi è attualmente dedicata al settore dell’arredamento. Qui si stampano componenti per i mobili, quali: unisci rete e fermamaterasso, piastre di aggancio, piccole ruote, rondelle e distanziali, piedini, maniglie e sospensioni.
“Come noto, in Brianza ci sono molte aziende attive in questo campo e, quindi, soprattutto agli inizi, abbiamo sfruttato le opportunità fornite dal settore dell’arredamento”, spiega l’AD.
Ma Omfi produce anche cappucci, tappi e componenti nel settore dei ricambi auto (ad esempio: supporti per sospensioni, coprileva, giunti per motori) e dei camper, oltre a piccoli pezzi per tetti, lucernari e ferramenta in generale.
“Date le tirature limitate, cambiamo frequentemente materiale o colore e, a volte, sostituiamo addirittura 10-12 stampi al giorno: in pratica, uno su ogni pressa”, spiega Gianpietro Frigerio. “Purtroppo, quando si cambia materiale così spesso, ci sono anche molti scarti da gestire, prodotti durante i vari avviamenti. Inoltre, c’è bisogno di poter contare su alimentatori e dosatori precisi e affidabili nel tempo”.
Ed è qui che entra in gioco Koch Technik, rappresentata nel nostro Paese da Nickerson Italia.
Caratteristiche e vantaggi del sistema Koch di colorazione diretta
Su alcune presse a iniezione di Omfi è installato il sistema di colorazione diretta di Koch Technik (vedi figura 1): una soluzione conveniente per il dosaggio di masterbatch o additivi direttamente nell’alimentatore del materiale di una pressa o di un estrusore. Tale sistema consiste in:
- Alimentatore monofase; in Omfi è monomateriale, ma è disponibile anche il modello “bimateriale”, per alimentare sia vergine che macinato.
- Tramoggia conica intermedia, che consente un “polmone” di materiale aggiuntivo pronto a entrare nel cilindro di plastificazione.
- Dosamaster KeM volumetrico, più preciso rispetto ai dosatori a coclea, grazie al rullo di dosaggio; ruotando, il rullo carica il granulo di masterbatch o additivo e lo scarica nel tronchetto di connessione.
- Tronchetto di connessione AZ3: unisce i due flussi (materiale e masterbatch) a un solo centimetro dalla bocca d’alimentazione del gruppo di plastificazione.
“Il sistema di colorazione diretta si basa su dosatori volumetrici che, anziché possedere una coclea, funzionano con un rullo speciale che gira sulla base degli impulsi ricevuti dalla pressa, scaricando la quantità di masterbatch desiderata in modo estremamente preciso”, spiega Eugenio Pederzolli, sales & marketing manager di Nickerson Italia. “Il principio è simile a quello utilizzato dai contadini quando devono seminare: il rullo gira e, ogni “n” metri, deposita alcuni semi nel terreno (vedi figura 2)”.
Modularità e alimentazione unita di vergine e masterbatch
“Un’altra caratteristica che gioca a suo favore”, continua Pederzolli, “è che il flusso del masterbatch e quello del materiale vergine si uniscono a pochissima distanza dalla bocca d’alimentazione della pressa. Quindi, pure nel caso di due materiali con diverso peso specifico, questi non hanno il tempo di “smiscelarsi” ed entrano in macchina perfettamente insieme. Anche le vibrazioni non influiscono sul processo e viene così garantita una distribuzione ottimale dei due componenti, evitando variazioni di colore o nella concentrazione degli additivi, tipici invece del dosaggio con coclea, dove il materiale più pesante scende prima di quello più leggero”.
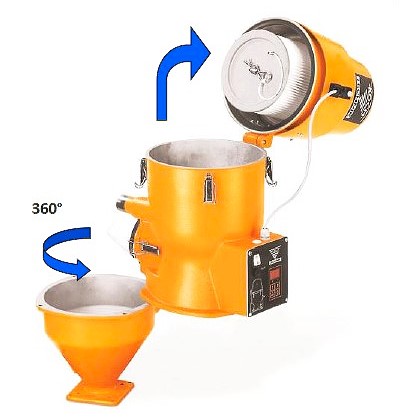
“In effetti, il sistema di colorazione diretta di Koch Technik è risultato essere molto più preciso rispetto agli altri che abbiamo testato. E questo rappresenta sicuramente un valore aggiunto. Inoltre, ha sempre funzionato perfettamente per ben trent’anni e ciò non era affatto scontato”, commenta Gianpietro Frigerio.
Un ulteriore punto di forza di questo sistema è la modularità, che consente di ridisegnarne la configurazione in funzione di eventuali nuove esigenze, integrando i componenti esistenti con quelli nuovi. La costruzione modulare rende estremamente efficiente pure la pulizia del sistema, che può sfruttare anche il getto rotante d’aria compressa su tutta l’altezza del filtro (figura 3).
“Onestamente, gli alimentatori e i dosatori di Koch sono risultati i migliori tra quelli che abbiamo provato”, aggiunge Isaia Frigerio. “Tra l’altro, la loro pulizia è davvero semplice e, quindi, porta via poco tempo alla produzione”.
Il problema tecnico e la soluzione by Nickerson
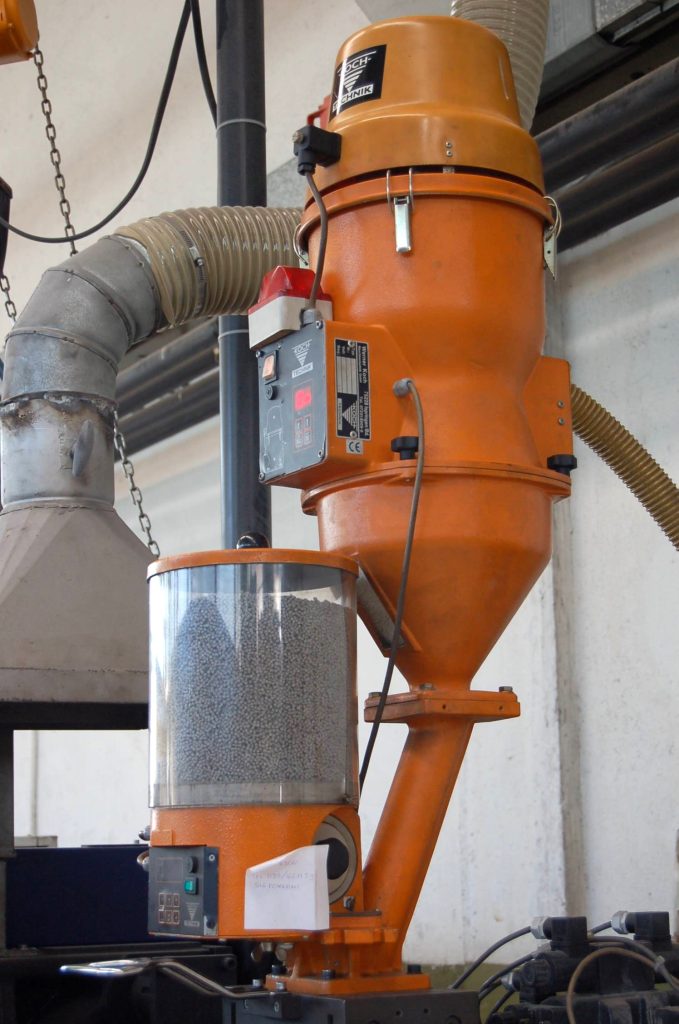
Il sistema di colorazione Koch più recente ha circa 15 anni, mentre il più vecchio è stato fornito a Omfi nel 1995 e, dopo quasi 30 anni, è ancora perfettamente integro dal punto di vista meccanico.
“Purtroppo, recentemente e in modo improvviso, si è rotta la scheda elettronica che comandava il funzionamento dell’alimentatore datato 1995 (modello 608), dedicata all’impostazione dei cicli d’alimentazione e di pulizia del filtro”, racconta Eugenio Pederzolli.
I titolari di Omfi hanno quindi chiamato i tecnici di Nickerson Italia, i quali, dopo aver verificato il numero di matricola dell’alimentatore e la lista ricambi, hanno confermato che le schede dell’alimentatore erano ancora disponibili. “Teniamo sempre a magazzino i ricambi delle attrezzature che trattiamo e anche in questo caso la scheda era disponibile in pronta consegna, ma se non fosse stata presente nel nostro magazzino in Italia, sarebbe stata comunque disponibile in Germania, presso lo stabilimento centrale di Koch Technik”, precisa Pederzolli.
La nuova scheda è stata così consegnata nei giorni successivi e, appena installata, l’alimentatore ha ricominciato a funzionare come se fosse appena uscito dalla linea di produzione.
“In un mondo che spinge sempre di più a rottamare i prodotti d’uso quotidiano (dagli smartphone alle auto) solo perché non sono più disponibili i ricambi, questo è un esempio di come il valore dell’investimento debba essere valutato nel tempo… anche a distanza di trent’anni”, commenta Pederzolli.
Conclusioni – Quando la solidità conta
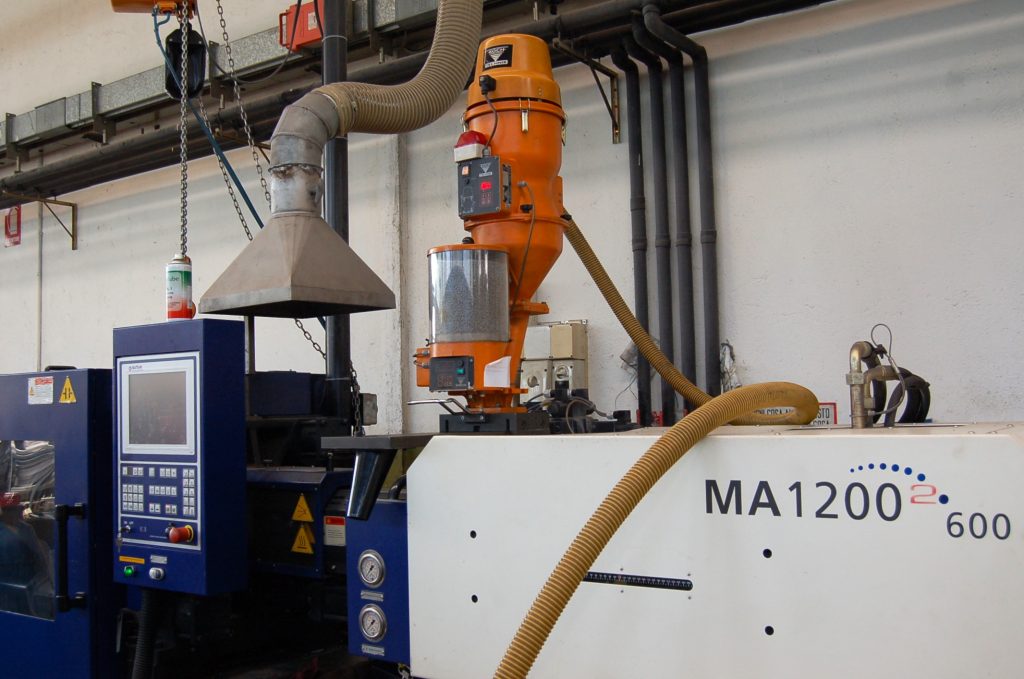
A fine intervista, Eugenio Pederzolli ha messo in evidenza anche il fatto che tutti i dispositivi Koch sono caratterizzati da una resistentissima costruzione in pressofusione, in lega d’alluminio. Caratteristica apprezzata anche da Isaia Frigerio: “La costruzione in pressofusione rende solidi e praticamente “eterni” gli alimentatori di Koch Technik, mentre, piano piano, abbiamo dovuto sostituire tutti gli altri, costruiti generalmente in semplice lamiera”.
“Per concludere, secondo me, sono due gli aspetti di valore che è possibile dedurre da questa esperienza”, dichiara Pederzolli. “In primo luogo, trent’anni fa Omfi ha deciso di investire denaro per l’acquisto di nuovi macchinari e, ancora oggi, quei macchinari funzionano bene e, in caso di guasto, sono tuttora disponibili i ricambi. Per cui, l’investimento fatto allora si è certamente ripagato nel corso del tempo.
In secondo luogo, si può parlare di sostenibilità e ridotto impatto ambientale anche nel caso di un bene strumentale durevole nel tempo. Infatti, dato che la maggior parte del costo in energia e materie prime viene speso nel momento in cui lo si costruisce, se dopo 30 anni di vita in esercizio il sistema d’alimentazione è ancora ben funzionante, significa che è stato evitato il costo per l’acquisto di una nuova attrezzatura, rottamando prima del tempo quella vecchia e producendo così più scarti da gestire”.
“Sono d’accordo: il valore dell’investimento è importante. Il fatto, poi, che i dispositivi di Koch Technik funzionino ancora dopo trent’anni e che siano tuttora disponibili i ricambi dimostra sicuramente la serietà e la continuità del servizio di quest’azienda costruttrice”, chiosa infine Gianpietro Frigerio.