Le società Syensqo, leader nei polimeri speciali ad alte prestazioni, e ZF, fornitore Tier 1 di sistemi avanzati per la mobilità, hanno annunciato con orgoglio che l’alloggiamento sviluppato per il veicolo EX90 di Volvo, e prodotto utilizzando Xencor™ HPPA rinforzato con fibre di vetro lunghe (LGF), ha ricevuto il prestigioso premio Automotive Award 2024 dalla Society of Plastics Engineers (SPE) Central Europe.
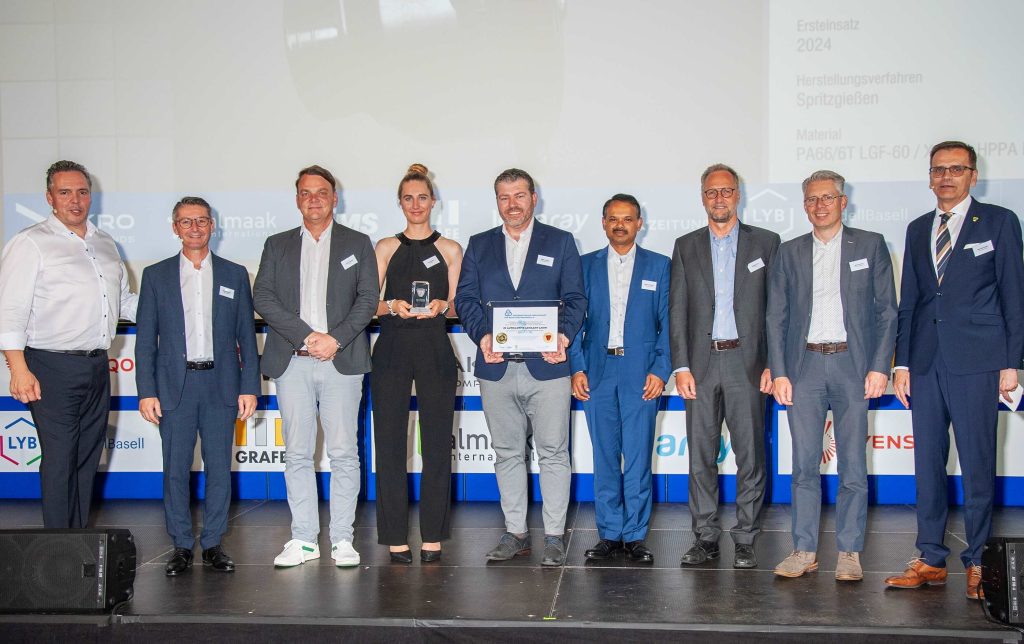
In particolare, questo involucro per l’impianto sterzante è stato premiato per la sua eccezionale rigidità, sostenibilità e stabilità dimensionale.
L’innovativo alloggiamento in termoplastico, il primo a essere utilizzato in un sistema sterzante al posto di un convenzionale componente in metallo, si è classificato al terzo posto nella categoria “Chassis Unit – Structural Component”, riconoscendo così gli straordinari progressi fatti dai materiali plastici per la tecnologia e la progettazione dei veicoli del futuro.
La combinazione della tecnologia a fibre lunghe di Xencor™ HPPA con il particolare design del componente consente di ottenere la rigidità e la stabilità necessarie per resistere a temperature estreme (da -40°C a +125°C) e a carichi dinamici, il tutto offrendo un rapporto costo/prestazioni favorevole. L’uso del termoplastico Xencor™ HPPA LGF al posto del metallo ha consentito un risparmio di peso di circa il 40% in questa applicazione.
Affidabilità sul lungo periodo
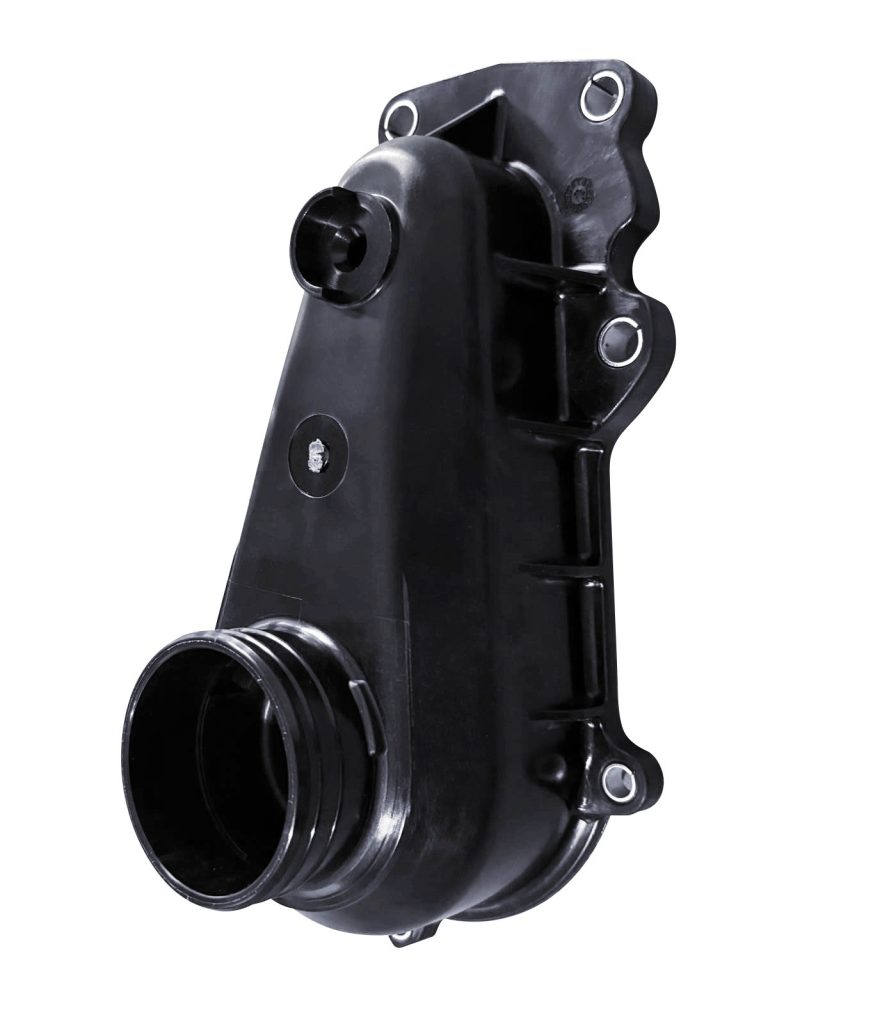
“I polimeri speciali di Syensqo hanno consentito di mettere a punto per decenni soluzioni di mobilità leggere, economiche ed efficienti in termini di consumo di carburante. Siamo onorati di ricevere questo premio come testimonianza della nostra proficua collaborazione con ZF Group e Volvo in un’applicazione automobilistica cruciale per il settore”, ha affermato Georges Houtappel, vicepresidente esecutivo della divisione Trasporti di Syensqo.
Data la natura critica per la sicurezza del sistema sterzante, Syensqo ha sviluppato modelli completi per valutare durata e invecchiamento e garantire così affidabilità sul lungo termine. L’innovativo processo di stampaggio a iniezione “one-shot” (in un’unica fase) utilizzato per questo componente consente l’integrazione di elementi funzionali, come i perni di centraggio in metallo, per un allineamento preciso, e le nervature ideate per migliorare le prestazioni di tenuta.
A differenza dei tradizionali alloggiamenti in alluminio, il materiale termoplastico fornisce un’intrinseca resistenza alla corrosione, eliminando così la necessità di effettuare l’anodizzazione.