Test Lab di Oerlikon HRSflow guida l’innovazione nello stampaggio a iniezione di biopolimeri e plastiche post consumo con tecnologie avanzate per processi produttivi più sostenibili
di Nicoletta Boniardi
La sostenibilità sta trasformando il settore delle materie plastiche, spingendo le aziende a rivedere logiche e processi produttivi per rispondere alle normative dell’Unione Europea, che ha fissato precisi obiettivi per il riciclo e il riuso. E se oggi le plastiche riciclate rappresentano solo il 13,5% del contenuto di nuovi prodotti e componenti (+37% negli ultimi quattro anni), secondo una recente analisi di Boston Consulting Group, entro il 2030 copriranno il 25% della domanda europea, arrivando al 65% entro il 2050. Anche il mercato dei biopolimeri ha segno positivo, con una crescita delle capacità produttive che in Europa dovrebbe triplicare entro il 2028, sfiorando i 7,43 milioni di tonnellate (fonte: European Bioplastics).
Le plastiche sostenibili sembrano dunque destinate a un futuro roseo, con un enorme potenziale applicativo in molti settori industriali, che lasciano però questioni aperte dal punto di vista tecnologico. L’introduzione relativamente recente – e soprattutto continua – di nuovi gradi di bioplastiche comporta infatti incertezze legate alle loro prestazioni e ai modelli di degradazione durante i processi produttivi, soprattutto in condizioni operative specifiche.
Anche la lavorazione dei materiali riciclati presenta diverse criticità, principalmente dovute alla grande variabilità del materiale di partenza e alle conseguenti fluttuazioni delle sue caratteristiche. Per risolverle è necessario pensare in modo differente, imparando a trovare i limiti di questi polimeri e a superarli, sia progettando manufatti con geometrie che le compensino sia sviluppando soluzioni tecnologiche per riuscire a lavorarli nel miglior modo possibile. È questo l’obiettivo con cui Oerlikon HRSflow (San Polo di Piave, Treviso) ha inaugurato Test Lab, un centro tecnologico d’avanguardia dedicato allo sviluppo di soluzioni innovative per lo stampaggio a iniezione di plastiche “green”, che oggi guardano al mercato del packaging, della cosmetica, del Caps&Closures e, in generale, a tutte le applicazioni eco-friendly.
Un centro per l’innovazione sostenibile
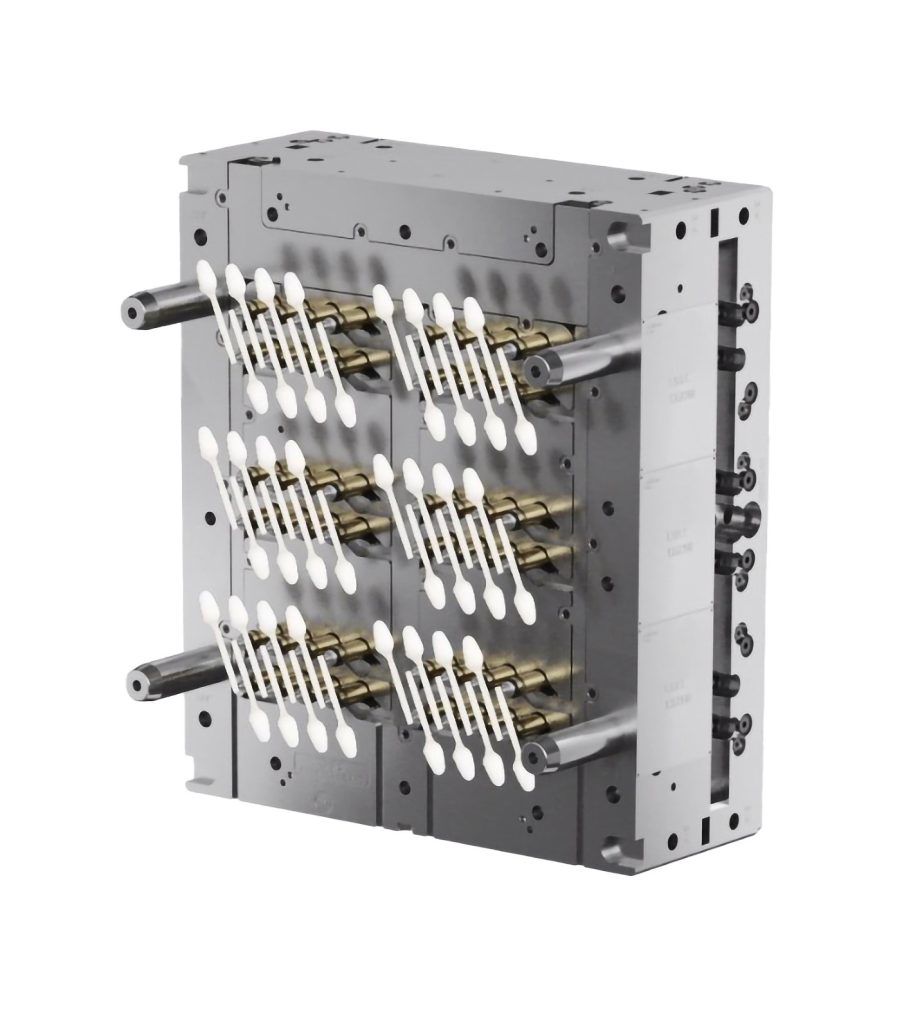
Test Lab rappresenta un punto di riferimento per l’industria, fornendo un supporto completo che spazia dall’analisi reologica e progettuale fino al collaudo, alla produzione e alla manutenzione. Oltre alla campionatura e alle prove per l’analisi preliminare, offre un servizio dedicato alle applicazioni speciali, che consente di ottimizzare la configurazione del sistema e di prevedere la qualità delle parti grazie a sistemi a canale caldo avanzati.
Il laboratorio è dotato di attrezzature all’avanguardia, che includono stampi prototipo per testare i polimeri più impegnativi, una gamma completa di ugelli e tipi di flusso personalizzati, oltre naturalmente a macchine per lo stampaggio a iniezione con forza di chiusura da 50 a 1000 tonnellate. Per incontrare le esigenze del settore del packaging e della cosmetica, dove l’attenzione nei confronti di materiali che riducano l’impatto ambientale è sempre maggiore, è stata recentemente installata una nuova pressa ibrida e-speed 280 di Engel, ottimizzata per la lavorazione di polimeri bio-based, PET e, soprattutto, rPET.
Iniezione alla velocità di 1400 mm al secondo
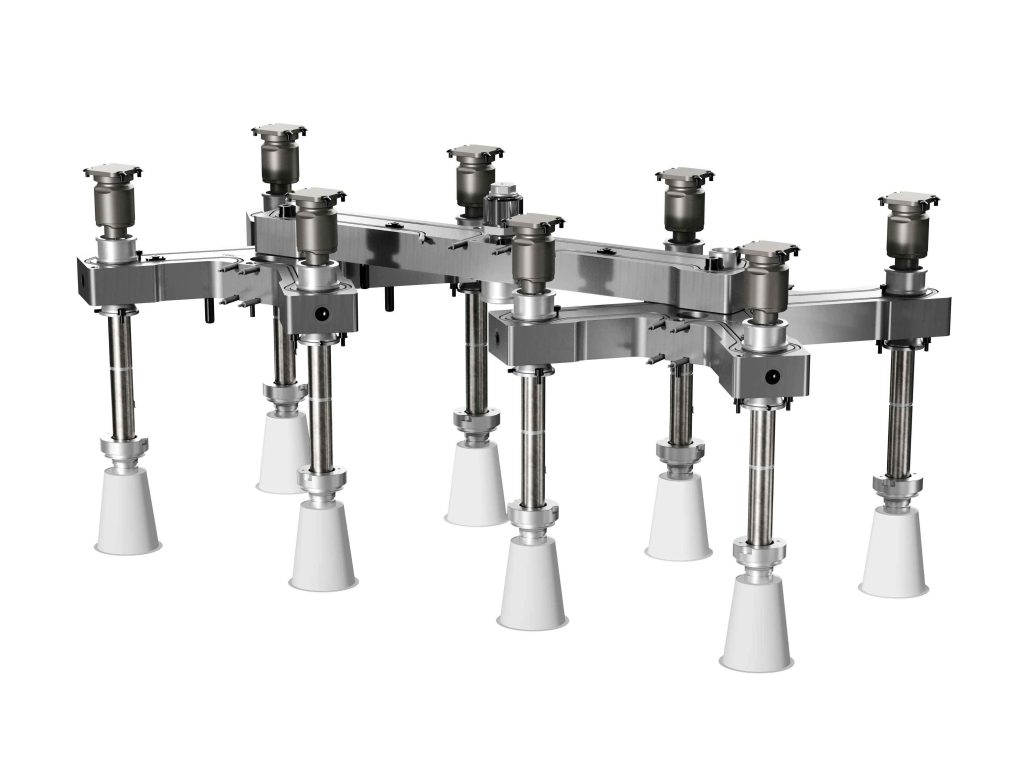
La e-speed 280 è dotata di un gruppo di chiusura elettrico e di un gruppo d’iniezione idraulico di nuova concezione estremamente potente, che raggiunge una velocità massima di 1400 mm/s e una pressione d’iniezione fino a 2600 bar con stampate di peso ridotto e un rapporto estremo tra spessore della parete e percorso del fuso. Questi parametri lo rendono uno dei gruppi d’iniezione più dinamici attualmente disponibili sul mercato a livello mondiale. Per la lavorazione di materiali post consumo e, in particolare, del 100% di rPET, Engel ha combinato il nuovo gruppo d’iniezione con un gruppo di plastificazione appositamente progettato. La configurazione della macchina permette inoltre di soddisfare gli elevati requisiti prestazionali imposti dallo stampaggio di articoli a parete sottile.
«La Engel e-speed 280 rappresenta un passo fondamentale nel nostro impegno per la sostenibilità», afferma Massimo Rossi, direttore Ricerca e Sviluppo di Oerlikon HRSflow. «Il potenziale delle plastiche bio e post consumo è enorme in molte applicazioni, ma la grande variabilità delle caratteristiche richiede particolari attenzioni. La e-speed 280 ci permetterà di esplorare nuove frontiere nel campo dei materiali e dei processi produttivi, fornendo ai nostri clienti le migliori soluzioni possibili».
Stampaggio ottimizzato di rPET e biopolimeri
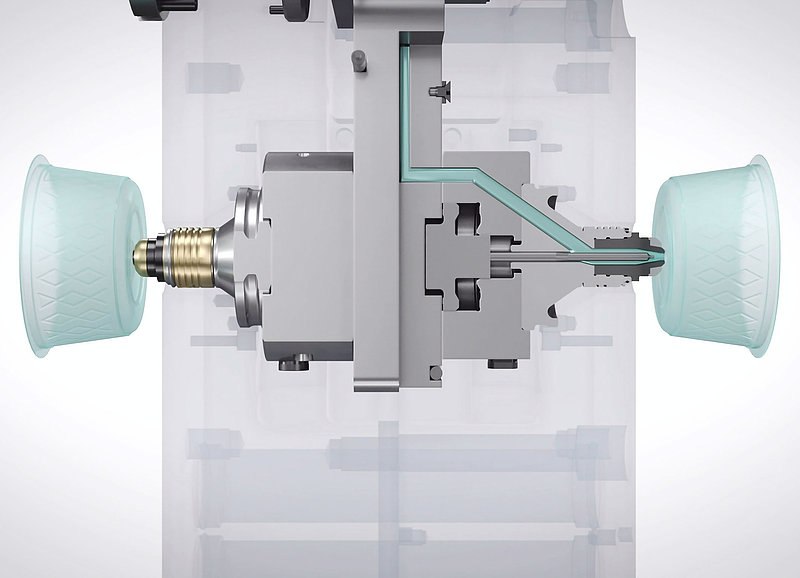
Plastiche post consumo e biopolimeri richiedono una gestione attenta durante il processo di stampaggio a iniezione, a causa di finestre di lavorazione più strette, necessità di pressioni elevate e sensibilità a stress termici e di taglio.
«Per questa ragione abbiamo sviluppato un approccio altamente personalizzato, che si adatta alle specifiche caratteristiche di ciascun materiale e applicazione», precisa Massimo Rossi. «Il nostro percorso, iniziato nel 2014 con un progetto dedicato alle capsule in PLA per il caffè espresso, ci ha permesso di acquisire competenze nella lavorazione dei biopolimeri, affermandoci tra i primi al mondo in grado di stampare capsule in PHA con stampi industriali a 32 cavità. Questo materiale del futuro, di derivazione batterica, è l’unico polimero riconosciuto dall’ente di certificazione TÜV free soil e marine biodegradable. Ora vogliamo ampliare il nostro know-how sulle plastiche riciclate, in particolare sull’rPET, con l’obiettivo di sviluppare soluzioni avanzate, tese a migliorare la qualità del prodotto finito attraverso l’ottimizzazione del processo produttivo».
I risultati delle prime prove nel Test Lab
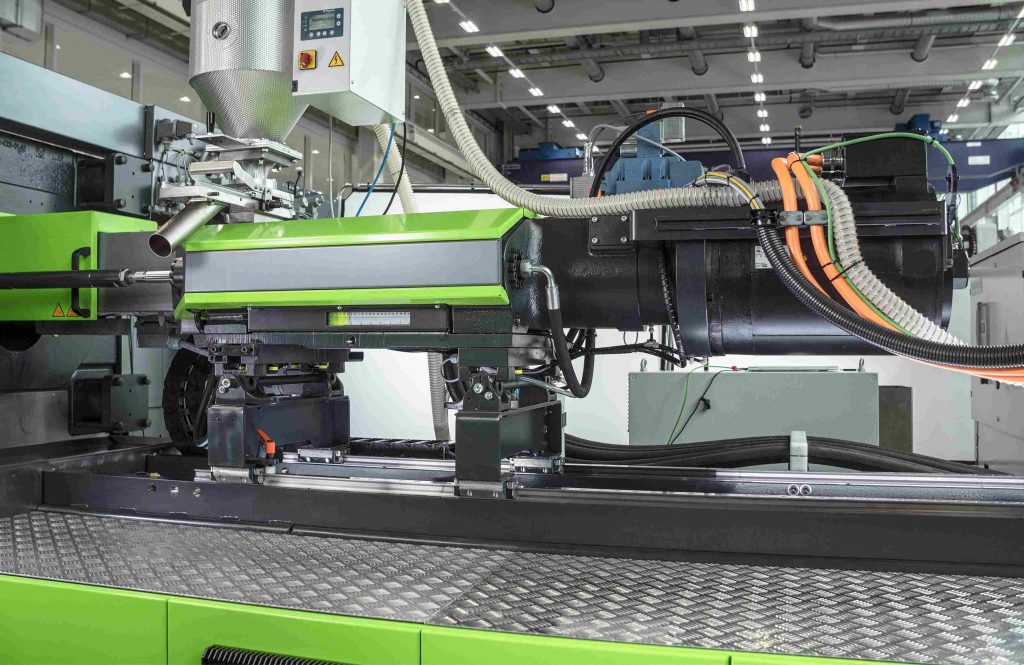
«I primi test per verificare la processabilità del PET riciclato mediante stampaggio a iniezione si sono rivelati promettenti», continua Massimo Rossi. «Durante le prove, la Engel e-speed è stata utilizzata per applicazioni in PET complesse, con un rapporto L/T molto elevato in varie configurazioni stampo». Per le applicazioni a parete sottile, Oerlikon HRSflow ha sviluppato i sistemi della serie Xp, concepiti per resistere a elevate pressioni di riempimento (fino a 2200 bar) e per consentire iniezione e tempi ciclo veloci in un processo stabile, con un’elevata uniformità del peso delle parti. Oltre alla versione appoggiata, è disponibile anche una versione stack mold per l’iniezione di spessori ridotti, denominata Xd.
Commentando l’esito delle prove, Massimo Rossi sottolinea: «Siamo riusciti a ottenere ottimi risultati grazie a diversi accorgimenti tecnici, come un rapporto ottimale tra canalizzazione del canale caldo e geometria del manufatto, unito a un layout adeguato del sistema. La nostra profonda conoscenza dei polimeri ci ha permesso di sviluppare un sistema d’iniezione che sfrutta appieno le capacità della Engel e-speed senza compromettere la qualità del polimero durante il processo. Anche con tempi prolungati della pressione di mantenimento, la qualità del prodotto è rimasta impeccabile, persino stampando PET grado bottiglia IV (0,75) ed rPET al 100%».
«La sfida sarà ora la collaborazione stretta tra tutti gli stakeholder per arrivare a un prodotto industriale affidabile. Per esperienza, stampare a iniezione PET – così come rPET – richiede la massima attenzione su tutte le variabili, senza lasciare mai nulla al caso», conclude Massimo Rossi.
Stampaggio “zero difetti” di plastiche sostenibili
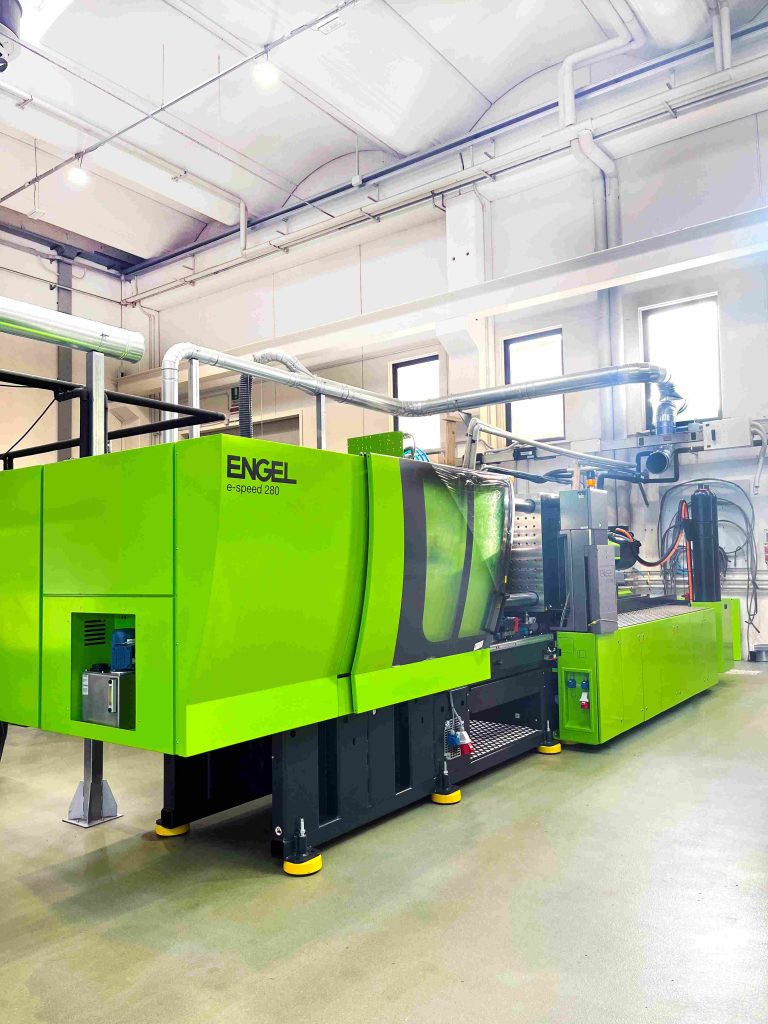
Le plastiche post consumo e i biopolimeri comportano in genere variazioni delle caratteristiche più ampie tra un lotto e l’altro rispetto alle tradizionali plastiche vergini. Ed è ben noto che, come i cambiamenti delle condizioni ambientali, anche quelli del materiale modificano le proprietà di scorrimento del fuso durante la fase d’iniezione, con un effetto negativo sulla qualità dei pezzi stampati che, nel peggiore dei casi, finiscono tra gli scarti, con spreco di risorse ed energia. Diventano quindi sempre più importanti gli assistenti intelligenti che monitorano, ottimizzano e regolano in continuo i parametri fondamentali per la qualità, rendendo i processi più stabili.
L’assistente digitale Engel iQ weight control, di cui è dotata la Engel e-speed installata nel Test Lab di Oerlikon HRSflow, è particolarmente indicato per lo stampaggio di questo tipo di materiali. Il software analizza in tempo reale la curva della pressione e della posizione della vite durante la fase d’iniezione e confronta i valori misurati con un ciclo di riferimento.
Su questa base, in modo completamente automatico e con un semplice clic sull’unità di controllo della pressa a iniezione, vengono calcolati nuovi parametri di processo e le impostazioni vengono regolate nel corso dello stesso ciclo di lavorazione.
Questo metodo di controllo del processo a circuito chiuso consente di regolare la curva della velocità d’iniezione, il punto di commutazione e la curva della pressione di mantenimento, il tutto senza prolungare il tempo di ciclo. Le variazioni delle caratteristiche del materiale possono essere così compensate automaticamente, garantendo una qualità del manufatto finale costantemente elevata e riducendo al contempo gli scarti al minimo.
Un supporto all’avanguardia
Il percorso verso una produzione più sostenibile nel settore delle materie plastiche passa attraverso l’adozione di nuove tecnologie e l’integrazione di materiali innovativi come i biopolimeri e le resine riciclate. Grazie alle tecnologie disponibili nel Test Lab, tra cui la pressa Engel e-speed 280, Oerlikon HRSflow si posiziona all’avanguardia nel supporto alle aziende che desiderano migliorare la sostenibilità dei propri processi produttivi, offrendo soluzioni su misura per affrontare le sfide dei materiali del futuro.