Per prendere parte come da tradizione all’appuntamento con Mecspe (la fiera internazionale di riferimento per l’industria manifatturiera in programma a Bologna dal 5 al 7 marzo) l’Associazione dei Tecnici delle materie plastiche, TMP, ha messo a punto un’iniziativa del tutto originale e di sicura attrattiva. Si tratta di un modello completo di filiera che partendo dal granulo di prodotto dalla trafila si dipana attraverso il suo utilizzo in una pressa a iniezione e allo stampaggio simultaneo di due pezzi – uno in policarbonato (PC) e l’altro in polipropilene (PP) – destinati a dar vita a un gadget esclusivo.
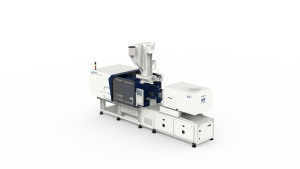
È un poggia-mestolo per la cucina con una parte in policarbonato trasparente e di dimensione più grande; e un’altra più piccola in polipropilene bianco in tre varianti di colore, una per ogni giornata di fiera. Il progetto è collaborativo e vede anche la partecipazione di un gruppo di studenti dell’Istituto salesiano San Giovanni Bosco di Sesto San Giovanni il cui compito è quello di descrivere ai visitatori le diverse fasi del processo. La loro presenza è importante perché dà ulteriore conferma di quanto TMP e il suo presidente Alan Catturini credano nel valore del dialogo con giovani e scuole.
Tutti per uno
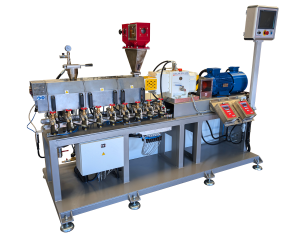
La piccola trafila è fornita dalla varesina EUR.EX.MA e la pressa a iniezione da Haitian International, con sede a Brescia. Il distributore tedesco Albis ha curato la fornitura dei materiali plastici; Brescia Master ha fornito i coloranti adatti all’uso a contatto con gli alimenti. Dalla lecchese Zeta Stampi Srl vengono, appunto, gli stampi mentre il sistema di iniezione a canale caldo bi-materia è curato da Primteck. Chiudono la serie l’altra bresciana Pedrotti Normalizzati e ML Engraving, bergamasca di Onore.
Ideatori e promotori di un modello che intende replicare fedelmente le attività in corso presso industrie che spaziano dall’auto, agli elettrodomestici e al medicale sono stati due nomi storici di TMP: Arturo Menzago e Amerigo D’Aloisio. Il primo è stato membro del comitato tecnico ed è ora revisore dei conti; il secondo è oggi socio onorario oltre che past president. Da Menzago e dalla società con la quale si presenta a Bologna ha preso il via la carrellata di Plastix fra i protagonisti di questa innovativa proposta. «Il brand è Primteck», ha detto, «ed è nata dalla collaborazione fra alcuni esperti dei canali caldi fra i quali il sottoscritto. È stata fondata in tempi molto recenti e offre soluzioni di qualità per i settori del packaging, dei materiali tecnici, la cosmetica e il medicale. Ho seguito in prima persona la progettazione del porta-mestolo, interfacciandomi con Zeta Stampi Srl e Haitian MM Italy. Portiamo a Mecspe un sistema di camera calda bi-iniezione, verticale e orizzontale, per PP e PC a uso alimentare integrata con una centralina elettronica di controllo del riscaldamento della camera calda e degli ugelli per mantenere costante il gradiente di risalita delle temperature. Per quel che riguarda poi la produzione dei pezzi, essa è eseguita con tecnologia a otturazione pneumatica». Arturo Menzago si è inoltre soffermato sull’attività dei ragazzi del San Giovanni Bosco, ritenuta a buon diritto centrale per più motivi: «Grazie a un ininterrotto impegno nella ricerca», ha osservato, «anziché essere sostituita, la plastica ha dimostrato di poter prendere in molteplici ambiti il posto dei metalli. Resta un materiale indispensabile, a dispetto della retorica, e siamo ovviamente i fautori e promotori del suo miglioramento, della sua modifica, rigenerazione rapida e di un ulteriore alleggerimento a parità di proprietà meccaniche. L’innovazione non si ferma e passa per la collaborazione con scuole e università: l’idea è consolidare nel mondo della didattica l’organizzazione e la continuità dei percorsi formativi ad hoc, convinti del fatto che le materie plastiche siano anche garanzia di attraenti opportunità occupazionali, nonostante crisi e difficoltà».
Specialisti degli stampi
Attiva dal 1996 a Viganò in provincia di Lecco Zeta Stampi Srl si occupa da sempre di costruzione stampi e stampaggio a iniezione conto-terzi grazie ai due reparti interni di officina, dove nascono gli stampi, e di stampaggio, ove sono realizzati i manufatti in materiale termoplastico. Sono certificati entrambi ISO-9001-2015. L’azienda crea stampi di piccola-media dimensione (sino a 750 x 1.500 millimetri) che possono essere montati sulle sue 15 presse da 60 a 550 tonnellate e si rivolge soprattutto ai settori auto, del bianco, elettronica e apparecchiature elettriche, casalinghi, macchine per caffè e giardinaggio. E ancora, espositori e display, edilizia e arredi. «Per Mecspe 2025», ha detto il titolare Matteo Zoia, «ci siamo occupati della realizzazione dello stampo con cui vengono prodotti i gadget. Siamo partiti dall’idea iniziale della partner IMG e abbiamo sviluppato i file CAD tridimensionali, passando poi alla prototipazione rapida da stampa 3D e quindi allo stampo». Convinta della validità di Mecspe come «occasione di confronto con colleghi e fornitori e come vetrina per conoscere eventuali nuovi clienti», Zeta Stampi Srl è presente sia nella Piazza TMP sia con un suo stand autonomo. Come anticipato da Arturo Menzago, un contributo di rilievo all’avvio del progetto è stato quello di Haitian MM Italy, da 17 anni distributore delle presse a iniezione per lo stampaggio di materie plastiche Haitian/Zhafirnel nostro Paese e in Romania. I macchinari sono utilizzati in vari settori merceologici come l’elettrodomestico, l’elettronica, il medicale e l’edilizia. La rete vendita è composta da 20 addetti; 30 sono quelli del service su tutto il territorio nazionale.
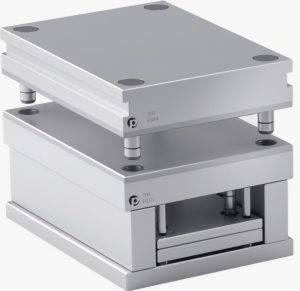
La sintonia è il valore aggiunto
Facendo un passo indietro e tornando a focalizzarci sugli stampi, È anche grazie all’ormai storica partnership in essere con la già menzionata Zeta Stampi che Pedrotti Normalizzati è entrata a sua volta a far parte della squadra delle aziende che partecipano al modello di filiera proposto da TMP. Da sessant’anni circa il marchio di Gavardo (Brescia) si occupa di progettazione e produzione portastampi e accessori, con un portfolio prodotti che indirizzano le diverse esigenze legate ai processi di costruzione stampi per iniezione e pressofusione. Forte del costante aggiornamento dei suoi prodotti e processi, effettua lavorazioni standard o a disegno monitorando passo dopo passo ogni passaggio della produzione. «Supportare i clienti nelle loro attività», ha fatto sapere Pedrotti Normalizzati tramite l’ingegner Maurizio Fiorentino, direttore delle vendite, «apre molte strade e opportunità di crescita. Riteniamo essenziali il dialogo e la collaborazione in tutte le fasi del lavoro. La nostra partecipazione alla Piazza TMP è motivata anche dalla relazione stretta con la nostra cliente Zeta Stampi. Forniamo il portastampo ed i componenti richiesti per il completamento del progetto, fieri che il nostro nome venga associato alle attività di un’azienda con la quale cooperiamo da anni». Non meno preziosa è la possibilità di essere protagonista di «uno spazio espositivo legato alla produzione; e nel quale i visitatori osservano la reale applicazione delle tecnologie al loro settore». È «un simbolo dell’esposizione», secondo Pedrotti, che confida nell’apprezzamento del pubblico nei confronti della Fiera e naturalmente «del lavoro preparato da Zeta Stampi», come espressione di tutto quel che «quotidianamente essa ripropone ai suoi clienti, con il supporto costante di Pedrotti».
Il legame con la produzione, simbolo di Mecspe
«Nella filiera della Piazza TMP», ha detto il responsabile marketing di Haitian MM Italy Giovanni Ruggeri, «esponiamo una pressa elettrica per stampaggio termoplastici a iniezione. È il modello Zeres di Zhafir, arrivato alla quinta generazione, popolare in Europa e progettato per garantire alta flessibilità e precisione. La pressa elettrica, grazie anche a soluzioni idrauliche mirate – estrazione centrale e accostamento carro – offre precisione e ripetibilità del tutto competitive. La nostra partecipazione all’iniziativa è stata spinta dallo spirito di unione e collaborazione instauratosi tra i diversi partner. È stato realizzato in forte sintonia con i fornitori dello stampo, della camera calda, del materiale plastico e altre attrezzature stimolando così ulteriori rapporti professionali e conoscenze delle ultime tecnologie. Ci aspettiamo un ottimo riscontro da parte degli utenti finali che potranno vedere in funzione vari componenti tecnologicamente avanzati e operanti in sinergia». EUR.EX.MA (Eurotech Extrusion Machinery Srl) progetta e produce soluzioni avanzate per l’estrusione da laboratorio e pilota nel settore dei materiali termoplastici. Caratterizzate dalla flessibilità e precisione, le sue macchine coprono l’intero spettro dei processi di estrusione e trovano in particolare spazio nei laboratori e centri di ricerca e sviluppo, dove vengono utilizzate per la formulazione di nuovi materiali e lo studio delle relative proprietà. «In occasione del Mecspe 2025», ha detto il CEO dell’azienda Luca Lepori, «EUR.EX.MA porta nella Piazza TMP una linea completa da laboratorio bivite, impiegata per granulare un polimero termoplastico, successivamente lavorato in una pressa a iniezione, riproducendo il primo passaggio della filiera produttiva della plastica». Anche per Lepori un aspetto fondamentale dell’intera iniziativa è dato dal coinvolgimento degli studenti delle scuole superiori. «Avranno l’opportunità», ha proseguito, «di avvicinarsi al panorama della plastica, comprendere i principi dell’estrusione e soprattutto di appassionarsi alla ricerca di materiali innovativi e biodegradabili in un’ottica di autentica economia circolare». Terminata la fiera, la macchina esposta è destinata a fare ritorno allo EUR.EX.LAB, il laboratorio interno della società con sede a Tradate (Varese) dove imprese e ricercatori potranno continuare a testare, sviluppare e sperimentare soluzioni inedite, sempre nell’ambito dei materiali termoplastici.
Tecnologia al servizio dell’estetica
I masterbatches per la realizzazione dei prodotti nei vari colori, nel contesto della Fiera, sono forniti da Brescia Master, che da trent’anni è specializzata nella loro produzione, così come in quella degli additivi per materie plastiche. Nel suo quartier generale di Poncarale, un’area di circa 4.000 mq, si avvale di cinque linee produttive e di un laboratorio interno attrezzato con spettrofotometri di ultima generazione e strumenti moderni sia per la creazione di nuovi colori, per il controllo-qualità sia per lo studio e l’analisi delle molteplici materie plastiche. Per l’azienda, presenziare a Mecspe ed essere protagonista della Piazza di TMP è un fatto prezioso per più motivi. «Innanzitutto», ha detto il responsabile commerciale di Brescia Master Natale Gregori, «l’evento è quanto mai utile per far conoscere la nostra realtà a livello nazionale; e come nelle edizioni scorse è un potenziale contenitore di contatti. Abbiamo inoltre la possibilità di essere parte di un progetto che si pone l’obiettivo di semplificare tutto l’iter produttivo di un manufatto plastico nel quadro di una manifestazione che ospita tanto gli operatori del settore – che sovente vedono soltanto una delle attività che concorrono alla produzione – quanto numerose, possibili nuove leve, per così dire, che di quest’esperienza possono fare tesoro».
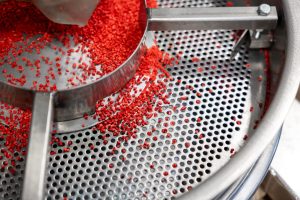
Di perfezionare il look del porta-mestolo che costituisce il prodotto finito della filiera e il gadget offerto alla platea di Bologna Fiere si è fatta carico ML Engraving. «Il nostro apporto al progetto», ha detto il project manager Fabio Barcella «consiste nell’aver migliorato l’estetica dell’oggetto. La richiesta è giunta da Zeta Stampi, che ci ha incaricati di incidere una fine satinatura nella matrice del componente più grande per dar valore al prodotto e nobilitare il materiale che, copiando la texture, si trasforma e assume un aspetto del tutto nuovo. La finitura ha anche validità funzionale perché riduce i segni dell’usura causata dall’azione frequente del comporre-scomporre le due parti».
Dotata di 25 macchine laser a cinque assi che lavorano 24×7 ML Engraving propone soluzioni customizzate e industrializzabili in base al progetto e al tipo di stampaggio per abbellire gli oggetti stampati grazie a texture e finiture che progetta e incide sugli stampi. Con un diametro di 40 micron, il raggio laser incide con grande precisione, preservando l’integrità di spigoli vivi e chiusure. «È una tecnologia versatile, sostenibile e digitale», ha proseguito Barcella, «e ciò significa: garanzia di ripetibilità, stabilità di processo e sicurezza, sia per gli operatori sia per l’ambiente. La nostra mission è proprio questa: aumentare il valore delle superfici attraverso le nostre texture. Negli anni abbiamo messo a punto servizi per migliorarne aspetto e funzionalità, ma anche per ottimizzare la filiera. Troppo spesso, infatti, dobbiamo intervenire con soluzioni di compromesso per gestire limiti e criticità tecniche nelle fasi ormai avanzate della produzione». Parlare a Mecspe con stampisti e stampatori significa quindi per ML Engraving dare visibilità ai suoi servizi di progettazione digitale e incisione di texture su stampi. «Includere le valutazioni sulla texture a inizio progetto», ha concluso Barcella, «permette di fare analisi preliminari sugli angoli di sformo, scegliere una texture su misura e addirittura migliorare lo stampaggio, grazie ai nostri esclusivi protocolli che agevolano l’estrazione del pezzo e riducono i più frequenti difetti tra i quali bruciature, mancati riempimenti o cambi di gloss, nel rigoroso rispetto di budget e tempistiche».
Un ponte verso l’università; un ponte verso gli USA
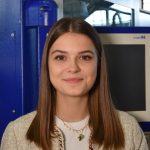
Laureata magistrale in Ingegneria meccanica presso l’università di Padova, Anna Bortoletto è attualmente dottoranda in Industrial engineering, con specializzazione in Materials engineering sotto la supervisione del professor Giovanni Lucchetta. Il tema di ricerca da lei sviluppato ha intersecato le tecnologie e i processi presentati da TMP nella Piazza di Mecspe 2025 col modello di filiera del quale si argomenta nel corpo centrale di questo articolo. «Interessa lo stampaggio a iniezione di polipropilene riciclato da post-consumo», ha spiegato a Plastix, «con l’obiettivo di sviluppare un processo produttivo avanzato per ottenere prodotti di alta qualità, studiando sia l’effetto dei parametri di processo sia l’impiego di tecnologie ausiliarie. Nel contesto di questo progetto, ho eseguito simulazioni Moldflow 2025 soprattutto per analizzare la corretta posizione del punto di iniezione nei due componenti studiati. In particolare, per quel che riguarda il porta cucchiaio in policarbonato, data l’alta viscosità del materiale, il rischio di intrappolamenti d’aria è significativo. Questi sarebbero visibili a occhio nudo, per la trasparenza del materiale, inficiando la qualità del pezzo stampato. La simulazione ha permesso di valutare dove si verifichino gli intrappolamenti e di valutare l’effetto di diversi PC con caratteristiche reologiche differenti. Quanto invece al più piccolo cucchiaio in polipropilene», ha osservato la ricercatrice, oggi negli Stati Uniti, «qui gli intrappolamenti d’aria non rappresentano una criticità, ma l’analisi ha consentito di individuare le aree in cui posizionare eventuali sfiati nello stampo al fine di ottimizzare il processo. Sono state inoltre condotte simulazioni preliminari di impaccamento e raffreddamento, così da valutare alcuni parametri di processo ottimali e varie configurazioni dei canali di raffreddamento».
di Roberto Carminati